Design and manufacturing of industrial furnaces and supervisory control systems.
Infor, a leading industrial equipment manufacturer was looking to update their legacy technology to establish a platform for growth to scale their business. They needed to provide easier and better access to information, establish a single integrated system, improve communications and information flow with other systems, plus enable enhanced business processes.
Challenges
- Legacy Infor technology platform lacked a modern user interface and capabilities
- Needed advanced functionality in forecasting, project management, product configuration, and support of multiple plant environments
- Lack of integration with CRM, expense management and field service systems
- Missing a “single source of truth”, as operations were growing and becoming more diverse.
About the Company
Ipsen USA, headquartered in Cherry Valley, IL designs and manufactures industrial vacuum furnaces, atmosphere furnace, and supervisory control systems.
Founded in 1948, Ipsen supports a wide variety of thermal processing markets including: Aerospace, Commercial Heat Treating, Medical, Energy, Medical, Automotive, and Tool and Die It leads the industry in thermal processing technology.
Multiple business entities and international facilities make up Ipsen Global, with production locations in America, Europe and Asia, and representation in 34 countries.
“Ultra’s leadership in negotiation leverage with the vendor was instrumental in getting the
best total cost of ownership for software and services. Additionally, Ultra’s leadership and
independent relationship with the vendor was key to escalate project issues/risks and getting
them resolved quickly.”
—- Heather McLellan, Director of Finance, Ipsen USA
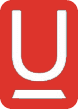
Our Mission
Plan, measure, and deliver business performance and profitability improvements to manufacturers & distributors, using our deep industry expertise and proven methodology.
Contact Us
- [email protected]
- 312-319-1411
-
Midwest Office:
939 W. North Avenue
Suite 750 Chicago, IL 60642 -
West Office:
1980 Festival Plaza Drive
Suite 300 Las Vegas, NV 89135
Learn
ERP Consulting Services