Take the next steps to transform your business
Business process mapping provides an easy-to-read view of your company’s business processes, including workflows and flowcharts. These maps need to be organized so they can be understood at a high level by top management and stakeholders, but also provide the detail that is needed for business process review and analysis.
We enrich all of our business process improvement engagements with our in-depth business process mapping methodology and business process mapping consulting services.
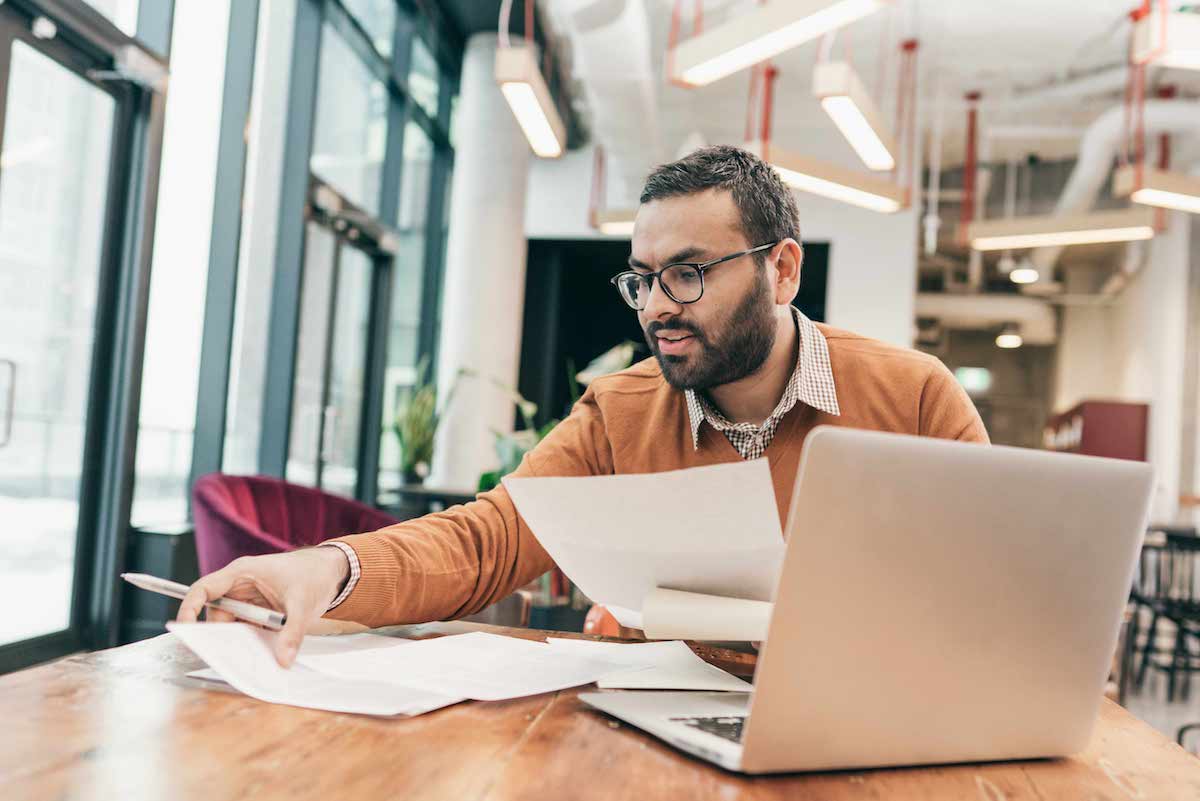