Wondering if SCM software is right for you? Here are some basics of supply chain management and steps to learn how to choose SCM software.
With major supply chain disruptions in the not-too-distant memory, leaders are wise to consider every option for more effective supply chain management (SCM). Robust, redundant, transparent and resilient are qualities that every manufacturer or distributor wants from the supply chain management process. And these qualities aren’t luxuries. They are crucial for your organization to stay competitive and meet customer demands. As reported in Supply Chain 24/7, “as the global pandemic, labor shortages and rising freight rates forced companies to rethink their supply chain management approaches in 2021, supply chain management (SCM) rose to the top as a way to cure at least some of these woes.”
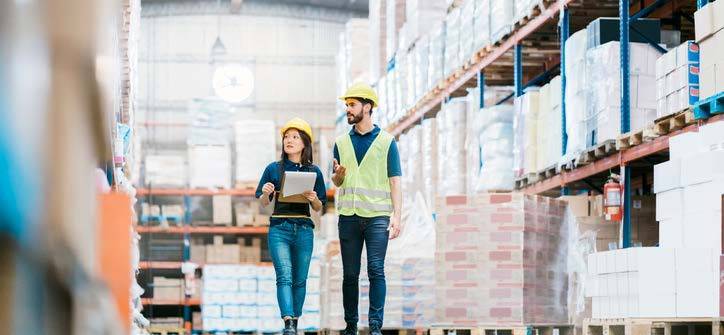
Supply Chain Risk Management
This ebook will delve into supply chain risk management strategies to minimize risks and ensure long-term success.
Introduction to Supply Chain Management
Supply chain management encompasses the coordination and integration of various processes and activities involved in the production and delivery of goods or services. It involves managing the flow of raw materials, inventory and finished products from suppliers to manufacturers, distributors, retailers and ultimately, to the end customer. The goal of SCM is to optimize these processes, minimize costs, improve efficiency and enhance customer satisfaction.
The supply chain management process involves several key activities:
- Planning: Forecasting and predicting customer demand, developing strategies and setting goals for each stage of the supply chain.
- Sourcing: Identifying and selecting suppliers, negotiating contracts and managing relationships with vendors.
- Manufacturing: Transforming raw materials into finished products through production planning, scheduling and quality control.
- Inventory Management: Managing and optimizing inventory levels to ensure efficient supply chain operations and reduce excess inventory or stockouts.
- Logistics and Transportation: Coordinating the movement of goods, selecting the most efficient transportation methods and ensuring timely delivery.
- Demand Planning: Anticipating customer demand, understanding market trends and aligning production and inventory levels accordingly.
- Analytics and Performance Management: Monitoring and analyzing supply chain performance, identifying areas for improvement and implementing data-driven strategies.
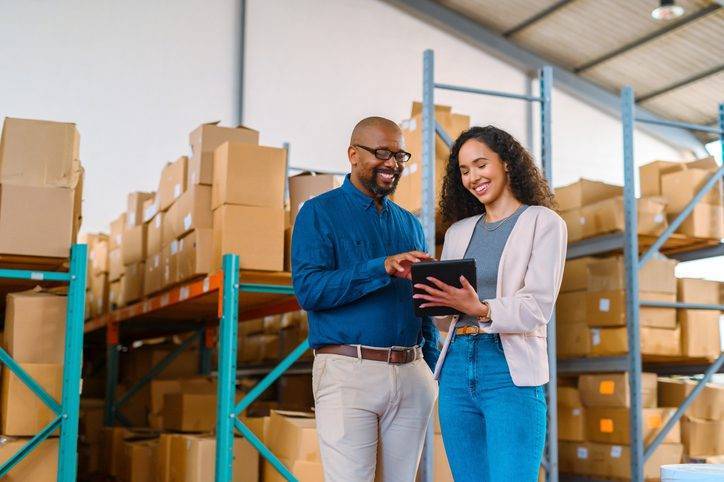
How to Choose SCM Software
Choosing the right Supply Chain Management software is crucial for the success of your supply chain management efforts. Here are some key factors to consider when selecting Supply Chain Management software:
1. Business Needs and Goals
Start by identifying your specific business needs and goals. Ask yourself the following questions:
- What are the critical areas of improvement in your supply chain?
- What are your long-term objectives?
Understanding your specific requirements will help you narrow down your options and choose the software that best aligns with your needs.
2. Scalability and Flexibility
Consider the scalability and flexibility of the SCM software.
- Can it accommodate your future growth and expansion plans?
- Can it adapt to changing business needs and evolving industry trends?
Choosing a scalable and flexible solution will ensure that your investment in Supply Chain Management software is future-proof.
3. Integration Capabilities
Ensure that the Supply Chain Management software can seamlessly integrate with your existing business systems, such as ERP, CRM and WMS. Integration capabilities are crucial for data sharing, process automation and collaboration with suppliers, customers and other stakeholders.
4. User-Friendliness and Ease of Implementation
Consider the user-friendliness and ease of implementation of the SCM software.
- Is it intuitive and easy to use?
- Does it require extensive training and technical expertise to implement?
Choosing a user-friendly and easy-to-implement solution will minimize disruptions to your business operations.
5. Vendor Reputation and Support
Evaluate the reputation and track record of the SCM software vendor.
- Do they have a proven track record of successful implementations?
- Do they provide comprehensive customer support and ongoing maintenance?
Choosing a reputable vendor with excellent customer support ensures a smooth implementation and post-implementation experience.
6. Costs and Return on Investment
Consider the total cost of ownership (TCO) of the Supply Chain Management software, including licensing fees, implementation costs and ongoing maintenance costs. Evaluate the potential return on investment (ROI) of the software in terms of cost savings, operational efficiency and improved customer satisfaction.
SCM Software Selection Experts
Ultra Consultants takes the time to know your business, your industry and your goals. This focus informs the selection process, bringing best-in-class software vendors to you. Ultra’s proven methodology helps you select the best-fit technology platform to help you achieve your goals. Get started with a free discovery call today.