IEM Trends for 2024
As we embark on 2024, the manufacturing industry finds itself in an exciting time of rapid change and innovation. For IEM to stay competitive, it is vital to understand the technological forces that are driving the industry forward. This year promises to accelerate several key trends, including the rise of smart factories, the push for supply chain robustness, the adoption of predictive maintenance practices and the transition to carbon-neutral operations.
By embracing these cutting-edge developments, your manufacturing company can boost productivity, optimize production processes, reduce costs and future-proof your business models. Though the manufacturing landscape is evolving, companies willing to adapt to emerging technologies and sustainability best practices will secure their place as industry leaders in the years ahead. The coming months will test firms’ agility, but those able to implement innovative solutions will thrive in 2024 and beyond.
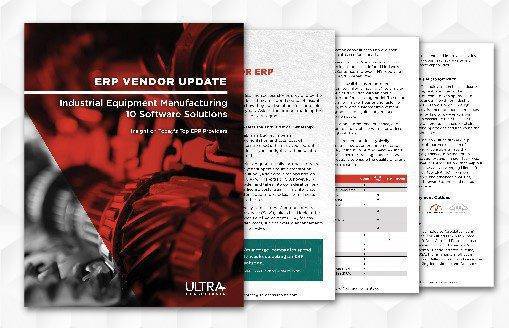
ERP Vendor Update: Industrial Equipment Manufacturing
Download this guide to get a close-up look at 10 of today’s top IEM software solutions.
1. Reshaping the Manufacturing Industry with Smart Factories
One major trend reshaping manufacturing is the emergence of smart factories, digitally integrated manufacturing facilities that leverage automation and data to unlock new efficiencies. Powered by advances in artificial intelligence, internet-connected sensors and analytics software, smart factories exemplify Industry 4.0—the ongoing Fourth Industrial Revolution centered on intelligent, flexible manufacturing. By implementing these digital transformation manufacturing trends and advanced technologies, your business gains end-to-end visibility and greater control over operations, enabling improvements in product quality, operational efficiency and sustainability.
Automated systems and AI oversight boost output quality and consistency while slashing waste. With the global market for smart factory solutions expected to exceed $320 billion by 2032¹, these intelligent plants offer a compelling path to enhanced productivity, cost savings and competitiveness. To thrive in the years ahead, embracing these smart technologies and digital integration is a must and not an option. By leveraging the promise of Industry 4.0, you can improve productivity, reduce costs and maintain your competitive advantage.
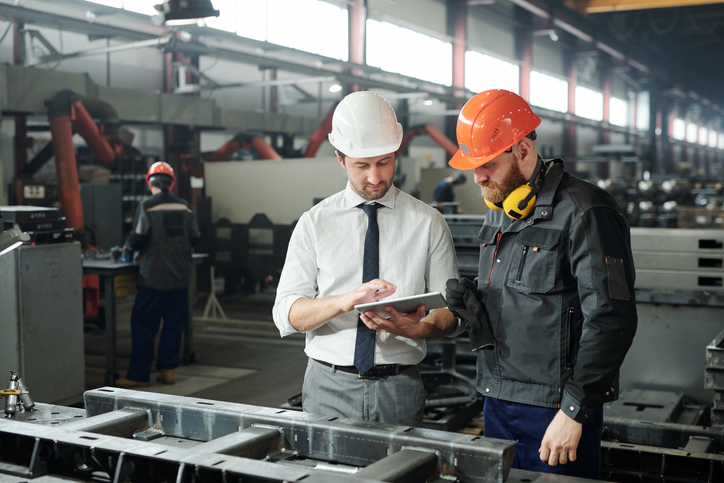
2. Harnessing the Power of Predictive Maintenance and Digital Twin Technology
Predictive maintenance and digital twin technology are transforming manufacturing processes and operations. As a manufacturer, you can shift from reactive to proactive maintenance by leveraging predictive analytics and data-driven insights. In doing so, you will be preventing failures, reducing costs and minimizing disruptive downtime. The predictive maintenance market is surging, expected to reach nearly $16 billion by 2026.
Digital twin tech takes preventative maintenance a step further by addressing larger-scale production issues before they arise. This is accomplished by creating virtual replicas of physical systems, a powerful simulation technology that enables real-time monitoring, testing and optimization. By unlocking deep insights about equipment performance, digital twins boost quality and productivity. The digital twin market is booming, projected to hit $73.5 billion by 2027.
Together, these intelligent technologies represent a seismic shift for manufacturing. Predictive maintenance substantially improves equipment reliability and availability. Digital twins unlock immense potential for process enhancements. By embracing these innovations, you can boost efficiency, reduce waste and drive competitive advantage.
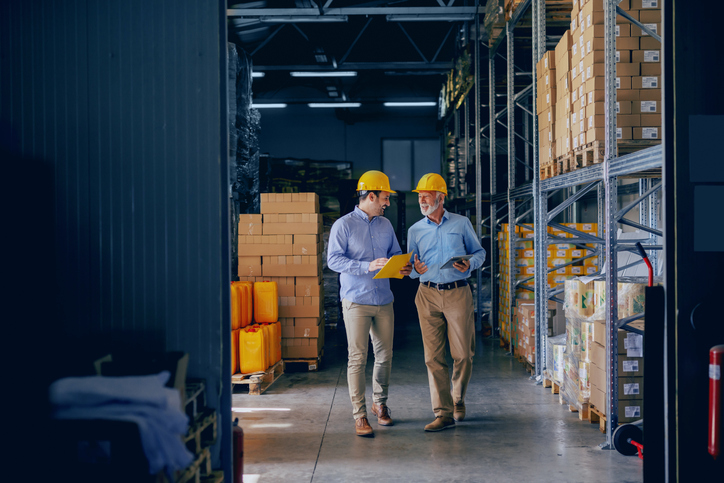
3. Building Resilient Supply Chains in the Face of Disruptions
Recent global events have put a spotlight on the susceptibility of supply chains to worldwide disturbances. From trade wars to public health crises, manufacturers have faced major hurdles that have disrupted operations and exposed crucial vulnerabilities. Supply chain disruption can impact your business negatively and result in increased costs, lost sales and damaged reputation. To safeguard supply networks and construct supply chain resilience against future shocks, manufacturers must rethink traditional supply chain models and adopt cutting-edge solutions.
Transitioning supply chains to digital platforms is a crucial step for manufacturers seeking more integrated and flexible networks. Harnessing innovations such as the Internet of Things, advanced data analytics and cloud-based solutions provides unprecedented visibility into supply chain dynamics. With real-time updates on inventory, transportation and consumer demand, your business gains the insight needed to streamline processes from sourcing to delivery.
Digitization also equips your company to regularly evaluate risks and diversify sourcing and production across various facilities and geographical regions. Rather than relying on fixed suppliers and factories, your business can dynamically shift operations to mitigate supply chain disruptions.
As global disruptions reveal vulnerabilities in far-flung supply chains, many companies are exploring reshoring—relocating manufacturing operations back to your company’s home country. This trend presents valuable opportunities. Production closer to headquarters lowers transportation expenses, enables tighter oversight to boost quality, gets goods to market faster and creates domestic jobs. With careful analysis, your manufacturing business can leverage reshoring to build more agile, resilient supply networks.
4. Addressing Labor Shortages and Upskilling the Workforce
The manufacturing sector is confronting a constrained labor pool, with projections of 2.1 million unfilled manufacturing positions by 2030. The industry is also continuing to embrace advanced technologies such as automation, robotics and AI. These technologies are presenting manufacturers with an opportunity to reshape workflows and reduce reliance on manual labor. With this comes concerns specifically on job loss. However, the reality is that technology will enable more streamlined, tech-driven processes that require upskilled talent to operate.
Attracting younger, tech-savvy employees will be critical to fully leverage these innovations. Modern workers are drawn to roles that allow them to interface with cutting-edge systems and data-driven decision making. Companies that integrate the latest automation and provide training in these emerging tech skills will have a competitive edge in recruitment and retention.
Furthermore, robots can seamlessly handle repetitive, tedious tasks, freeing employees for critical thinking and innovation. Imagine efficient, precision-oriented assembly lines directed by experts focused on optimizing processes and pioneering solutions. The result is reduced workloads for staff and boosted productivity for your business, harmoniously blending human and machine.
Rather than reducing headcount, these technologies can augment human abilities and eliminate repetitive manual tasks. Workers can be upskilled to take on more value-added responsibilities that machines cannot replicate, such as critical thinking, customer service and creative roles. Adaptable training programs and cultural readiness for changes will ease this transition.
By embracing technology’s possibilities and retraining employees to thrive in a tech-enabled landscape, your company can boost productivity while empowering people. Investment in human capital remains vital—equipped with the right skills, human ingenuity and innovation will still be manufacturing’s greatest asset.
5. Embracing Sustainability and Carbon Neutrality
As environmental awareness grows globally, manufacturers have a timely opportunity to showcase leadership by embracing sustainability targets. The manufacturing industry is responsible for substantial greenhouse gas emissions worldwide, positioning it to meaningfully address climate change through operational commitments. Carbon neutrality policies, while ambitious, can boost reputation, enable cost savings and open new markets.
The transition to carbon neutrality rests on deploying clean energy sources, enhancing efficiency and mitigating environmental impacts across manufacturing processes. Renewable energy adoption, energy optimization and clean technology represent carbon reduction pathways that also spur bottom-line savings and productivity gains.
Manufacturers that create sustainability roadmaps and carbon neutrality goals can appeal to eco-conscious buyers and gain competitive advantage. With environmental issues increasingly affecting consumer and investor decisions, carbon-conscious manufacturing creates lasting value. Overall, operational sustainability allows manufacturers to take part in vital climate action while future-proofing growth.
6. Harnessing the Power of Artificial Intelligence (AI) in Manufacturing
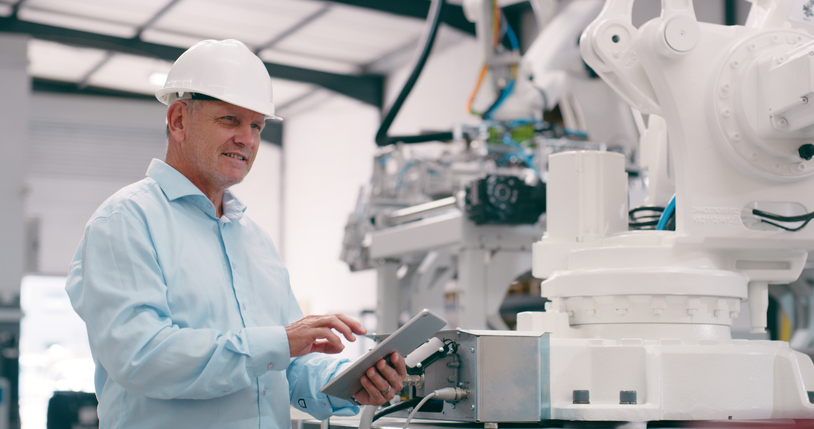
Exciting innovations in artificial intelligence are revolutionizing manufacturing operations and ushering the industry into a new era. Intelligent technologies such as machine learning, robotics and automation are being implemented across factory floors to optimize workflows and production lines, reduce costs, boost productivity, encourage innovation and enhance competitiveness.
These AI solutions provide your company with actionable insights to minimize downtime through predictive equipment maintenance. Immersive training simulations are facilitating safe and effective skills development among workers. Intuitive sensors paired with powerful data analytics tools also enable remote oversight capabilities and instant troubleshooting for managers.
With finely-tuned monitoring from afar and data-driven decision-making on-site, AI unlocks future manufacturing facilities that are safer, smarter and more efficient. Manufacturers that leverage these emerging capabilities today become more agile, productive and competitive players in the industry tomorrow. By welcoming AI transformation, the manufacturing industry can realize long-term gains in innovation, efficiency and sustainability overall.
7. Embracing 3D Printing and Additive Manufacturing
3D printing is another emerging technology that is going to have a major impact on the manufacturing production process. Additive manufacturing, commonly referred to as 3D printing, is transforming the way products are made by allowing for the creation of intricate and personalized components with remarkable efficiency and accuracy. Unlike conventional techniques such as die casting or CNC machining, this innovative technology does away with excess tooling and setup and grants manufacturers extraordinary freedom and flexibility when designing parts.
With 3D printing, the time from concept to finished product is drastically reduced. This emerging process promises to enable the on-demand production of components too complex or low volume to be economically produced through traditional means. As the capabilities of 3D printing platforms continue to advance, they are proving invaluable for industries aiming to deliver high-mix, customized orders in record time.
8. Harnessing the Power of the Industrial Internet of Things (IIoT) in Manufacturing
The Industrial Internet of Things ushers in a seismic shift for manufacturing, interconnecting the physical machinery and devices on factory floors with data networks and analytical tools. With IoT, your business can collect sensor measurements and performance metrics in real time, bringing critical and timely knowledge about operations in the production line.
Some common uses for IIoT devices are:
The location and utilization of equipment and tools is monitored ensuring efficient deployment and optimizing production schedules.
Smart sensors embedded in production lines monitor product quality parameters in real-time.
Sensor-equipped machines continuously monitor their own health and performance, providing real-time data on vibration, temperature, and other key metrics.
Connected sensors track raw materials and finished products throughout the supply chain, providing real-time supply chain visibility and inventory levels, enabling just-in-time delivery and streamlined logistics.
Smart meters and sensors monitor energy consumption across different sections of the manufacturing facility.
Wearable sensors track worker movement and environmental conditions, helping to identify potential safety hazards and ergonomic issues.
With these insights, which have been collected through connected sensors and equipment, your firm is placed in a compelling advantage—one that enables you to optimize your production processes, initiate predictive maintenance protocols and make strategic decisions that can be markedly sharpened. Simply, IoT offers your company the opportunity to elevate processes, enhance quality control, minimize idle time and remove doubt from managerial decisions.
Conclusion
The manufacturing industry is going through major changes due to advances in technology and shifting global forces. Advanced manufacturing technologies are revolutionizing how manufacturing companies run operations. Your IEM business must keep up with the latest developments and trends if you want to adapt and succeed in this changing situation. From intelligent factories and predictive upkeep to supply chain flexibility and carbon neutrality, these trends will define the manufacturing industry’s future.
We have expertise driving digital transformation across a variety of sectors, thanks to our diverse understanding of emerging manufacturing industry trends. At Ultra Consultants, we are uniquely equipped to help manufacturers implement digital transformation manufacturing trends and advanced technologies, navigating current industry challenges, while leveraging these trends to your benefit.
Our proven ability to successfully modernize businesses with forward-looking solutions such as smart factory adoption for production efficiency and technological advancements throughout the manufacturing sector positions us to guide companies into the next era of operations optimization and growth in 2024 and for years to come. Get started today by requesting your free discovery call to learn more about IEM trends for 2024 and how modern technology can help you maintain your competitive edge.