To stay competitive, constantly adapting and improving business processes is critical. One powerful strategy that helps businesses achieve this is continuous process improvement. This strategy allows your business to achieve a competitive edge and drive ongoing growth. It allows you to make incremental changes to your existing business processes thus enhancing efficiency, minimizing process variability and delivering superior customer experiences.
In this article, we will discuss:
- What continuous process improvement is
- The benefits of continuous process improvement
- The continuous process improvement model
- Strategies for continuous process improvement
- Choosing the right tools for continuous process improvement
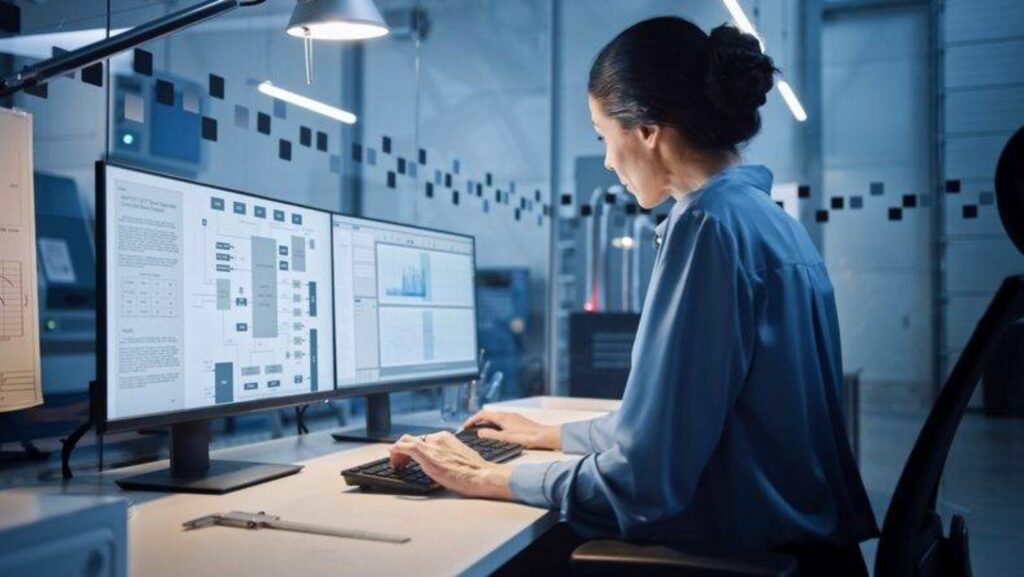
Continuous Improvement is Not Digital Transformation
Download the guide to discover how leveraging both Continuous Improvement along with Digital Transformation can help your company maintain a competitive edge.
Defining Continuous Process Improvement
A systematic approach to enhancing your business performance through ongoing growth is what continuous process improvement basically is. This process involves making small, incremental improvements to your existing processes. Rather than pursuing massive overhauls, you focus on modifications that target inefficiency.
The goal of continuous process improvement is to allow your organization to achieve operational excellence by:
- Identifying inefficiencies
- Eliminating waste
- Optimizing workflows
Continuous improvement models that are often associated with continuous process improvement are Lean, Six Sigma and Kaizen. These methodologies provide your organization with frameworks and techniques for driving improvement.
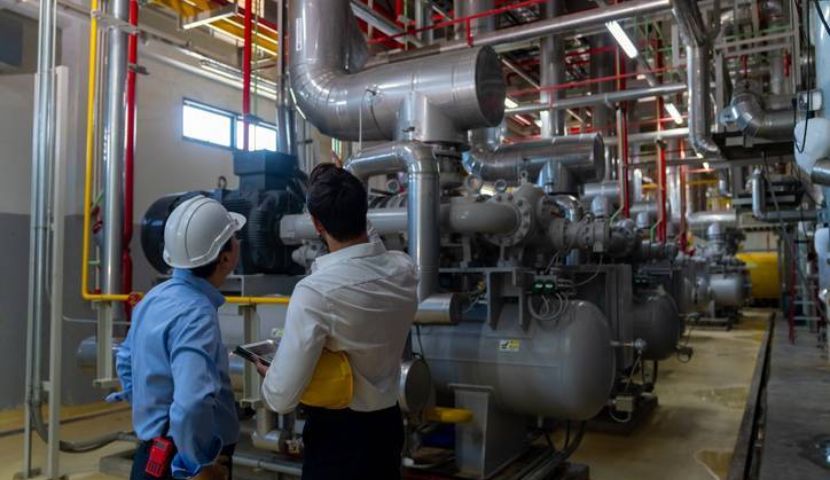
The Benefits of Continuous Process Improvement
1. Reduce Costs
One of the most immediate advantages of continuous process improvement is cost reduction. Your organization is able to identify and eliminate redundant steps that do not add value by carefully analyzing workflows. Through process mapping, your business can pinpoint bottleneck areas that result in delays, and therefore deal with these pain points.
Improving processes to cut waste directly translates to cost savings. Resources including employee time and effort, inventory and operational expenses are conserved. The savings quickly compound as refined processes are repeated, allowing funds to be allocated to other business needs. Smooth, streamlined operations prevent costly errors.
2. Improve Quality
Continuous process improvement also allows your company to improve quality by enabling you to identify root causes of defects and flaws, and therefore implement corrective and preventive measures. Through statistical analysis, you can track metrics and thus monitor and control quality levels. Refining processes eliminates inefficiencies that lead to mistakes, resulting in products or services that reliably meet specifications.
3. Enhance Efficiency
Business process mapping helps uncover redundant steps that can be removed. Analysis of workflow paths highlights areas of delay, enabling processes to be streamlined. Your organization can implement time-saving measures such as automation to boost speed and productivity.
4. Deliver Better Customer Experiences
Customers stand to gain tremendous value from your company’s continuous improvement initiatives. By eliminating inefficiencies and defects, your organization can better deliver products and services that exceed expectations. Streamlined processes prevent frustrating delays that negatively impact customer satisfaction. Consistent adherence to quality standards ensures customers receive flawless products and interactions.
Continual improvements enable your company to identify emerging customer needs as markets change. Your organization can then update processes and training to better serve those needs. Seeking customer feedback on improvements builds loyalty by demonstrating the business’s commitment to excellence. The end result is an optimal customer experience that breeds satisfaction, repeat business and positive word-of-mouth.
5. Boost Employee Engagement
An often overlooked benefit of continual process improvement is increased employee engagement. Involving cross-functional teams in improvement projects gives staff ownership of processes. Employees feel empowered to share their perspectives and ideas to shape workflows. This collaborative approach makes the workplace more participative and fulfilling.
Documenting standard procedures as part of continuous improvement provides employees with helpful guidelines for success rather than restrictive rules. As processes are refined, workers can take pride in being part of high-performing, efficient systems. The learning culture keeps job roles interesting and challenging. Appreciating employees’ process improvement contributions builds morale and motivates ongoing participation.
6. Drive Innovation
Finally, continuous improvement efforts cultivates innovation across the organization. Analyzing workflows prompts consideration of how processes could be performed differently. The cycle of incremental refinements inspires new ideas and sparks creative thinking. When employees are engaged and empowered, they are more likely to identify innovative breakthroughs.
Data-driven insights reveal market changes and evolving customer expectations that require new approaches. Leaders can then incubate innovative ideas by providing resources and support. A culture that celebrates improvement efforts makes employees feel psychologically safe to experiment and take risks. Innovation emerges organically from the foundation of continual process refinement.
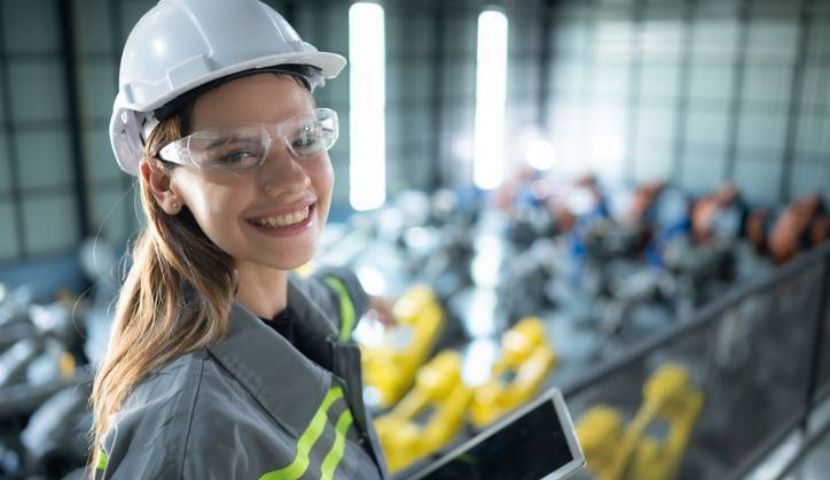
The Continuous Process Improvement Model
Step 1: Plan
The planning phase of the continuous improvement cycle involves thoroughly analyzing current processes to pinpoint opportunities for improvement. Planning begins by defining the scope of the process to be improved and identifying key performance metrics to track.
The current state assessment allows your organization to set tangible goals and targets for improvement. Examples of common objectives include:
- Reducing defects
- Speeding up cycle times
- Decreasing costs
- Improving customer satisfaction
Step 2: Do
In the “Do” phase, it’s time to implement the planned improvements on a small scale. Piloting changes on a subset of the process, a single product line or within a department allows for testing with minimal disruption and also provides an opportunity to work out any kinks before full implementation.
When pilot testing, it’s crucial for your organization to actively manage the changes and collect data. Key process metrics defined in the planning stage, such as cycle time or quality, are closely tracked. Customer satisfaction, employee engagement and other performance indicators are also monitored. The goal is to objectively evaluate the impact of the changes.
Step 3: Check
Did the implemented changes move the needle on desired performance metrics? The check phase involves comprehensively assessing and analyzing the results of process changes made during the “Do” stage. Quantitative process data collected during the pilot provides objective evidence of whether goals were met. For example, the billing error rate, throughput time or cost per unit can be compared before and after.
Gathering qualitative feedback from customers, employees and stakeholders via surveys, interviews and focus groups allows your organization to capture their perspective. This gives you information on how process changes impacted quality, service, satisfaction and ease of use. This subjective view is essential to judging true improvement.
Step 4: Act
In the final phase, your organization must determine appropriate next steps based on the evidence gathered during the “Check” stage. There are three basic options:
- Adopt
- Modify
- Abandon
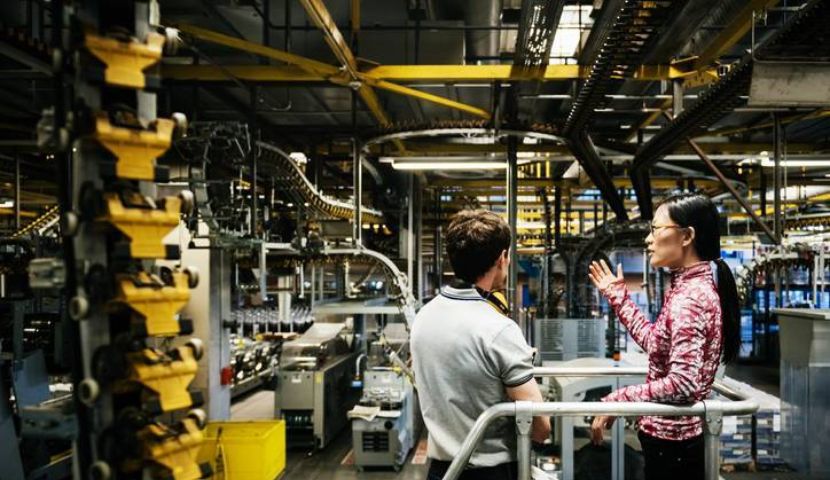
Strategies for Continuous Process Improvement
There are several strategies that can help your company implement continuous improvement:
1. Kaizen
Kaizen, a Japanese term meaning “change for the better,” is a philosophy centered on continual improvement through small, incremental changes. Kaizen methodology requires your organization to involve all employees in identifying and implementing opportunities for positive change in their daily work. This contrasts with approaches that rely on large, radical innovation projects. The Kaizen approach promotes frequent small tweaks and experiments to optimize processes vs. wholesale reengineering.
- Eliminating waste
- Improving productivity through optimized workflow
- Involving staff at all levels to contribute ideas
Uncovering areas for improvements relies on methods such as suggestion systems, brainstorming events and process analysis. Changes are made iteratively by empowering frontline teams to pilot and refine new methods. With a culture of ongoing improvement instilled across your organization, the cumulative effect of small Kaizen changes can yield substantial benefits over time.
2. Value Stream Mapping
Value stream mapping provides a visual methodology to analyze the flow of materials and information through business processes. The current state value stream map depicts how a process operates presently. Mapping out each step allows your organization to identify wasted time and effort. Process cycle efficiency, quality and speed metrics are evaluated.
Once the current state is mapped, a future state value stream map is designed to eliminate non-value added steps and optimize the workflow. This highlights opportunities for improvement through lean principles such as reducing batch sizes, balancing workloads, eliminating redundancies and smoothing material flows.
3. DMAIC
The DMAIC methodology (Define, Measure, Analyze, Improve, and Control) provides a data-driven framework for process improvement used in Six Sigma initiatives. The five phases of DMAIC guide organizations through structured problem-solving:
- Define: Pinpoint the root causes of issues to address
- Measure: Quantify the current performance of the process
- Analyze: Identify sources of defects and variation
- Improve: Develop solutions to address the root causes
- Control: Implement controls to sustain improvements
Each phase applies analytical tools and statistical techniques to dig into problems, derive insights, design solutions and establish ongoing metrics to maintain enhanced performance levels. DMAIC’s rigorous approach ensures improvement initiatives are targeted on priorities backed by hard data.
4. Five Focusing Steps
The Five Focusing Steps comes from the Theory of Constraints and provides a systematic way to identify and address bottlenecks limiting throughput. The steps involved in this strategy are:
- Identify the system constraint
- Decide how to exploit the constraint
- Subordinate all other processes to that decision
- Elevate the performance of the constraint
- If a constraint is broken, find a new one. Repeat.
5. 5S Philosophy
The 5S system creates an organized, clean and efficient working environment to improve quality, productivity, and safety. The five steps are:
- Sort: Eliminate anything not needed for the process.
- Set in Order: Organize essential items and tools for ease of use.
- Shine: Clean the workplace and equipment.
- Standardize: Develop consistent procedures and assign responsibilities.
- Sustain: Embed 5S as a new way of working through training and audits.
Conclusion
We equip your organization with the right tools and technologies to fuel your continuous improvement journey and empower you to achieve operational excellence. Ultra Consultants has deep industry experience and through a collaborative approach, we can help your organization gain a sustainable competitive advantage and thrive in the ever-evolving market.
Table of Contents
More ERP material...
AI’s Role in Digital Transformation
Data analytics holds the ability to highlight inefficient manufacturing processes and enable…
Master Data Management (MDM) Strategy: A Guide to Getting It Right
Companies currently generate vast amounts of data from their systems. But while…
Is Your HCM Platform Future-Ready? 6 Signs It’s Time for a Change
The work world is changing face and HR teams are under pressure…