Such continuous improvement programs provide the necessary tools and resources to streamline the implementation of a continuous improvement business strategy. By fostering a culture of continuous process improvement, organizations can adapt, evolve, and thrive in today’s ever-changing business landscape.
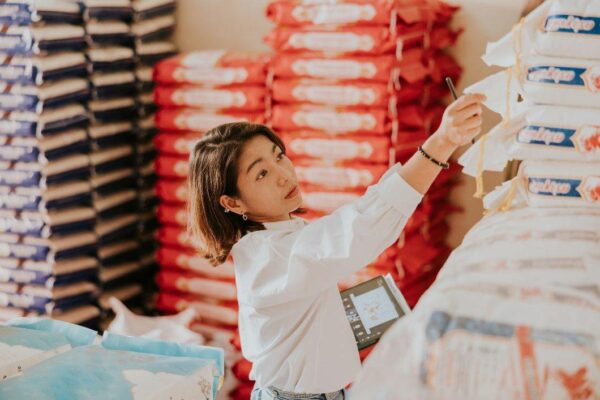
Continuous Improvement for Competitive Advantage
Download the eBook for strategies to drive change, measure progress and achieve results with continuous improvement.
What is a Continuous Improvement Process?
Continuous Improvement can help your company achieve incremental improvement over time. This ongoing effort enables the identification of areas for improvement, such as improving quality, increasing productivity or reducing waste.
Continuous Improvement Methods
There are many methods of continuous improvement, all with the goal of improving processes through establishing a company culture where employees are encouraged to seek out and identify areas for improvement. These include:
- Plan – Do – Check – Act (PDCA) – This method prescribes a problem-solving system which includes planning small improvements, reviewing the resulting data to evaluate the results, and implementing ongoing improvement through standardization.
- Lean methodology – Focuses on reducing waste and creating efficient workflows to optimize processes.
- Six Sigma – Aims to reduce defects and variability in processes in order to improve quality.
- Total Quality Management (TQM) – This method emphasizes a continual improvement process across the entire organization, focusing on getting the company’s people involved in process changes and increasing customer satisfaction.
- Theory of Constraints (TOC) – Focuses on removing constraints in order to facilitate optimized resources and workflows.
- Root Cause Analysis (RCA) – Seeks to identify the root causes of problems to implement long-term solutions.
- Benchmarking – Identifies improvement opportunities by comparing key metrics against industry standards or competitors.
Ready to start your digital transformation journey?
Click the button below to request your free discovery call.
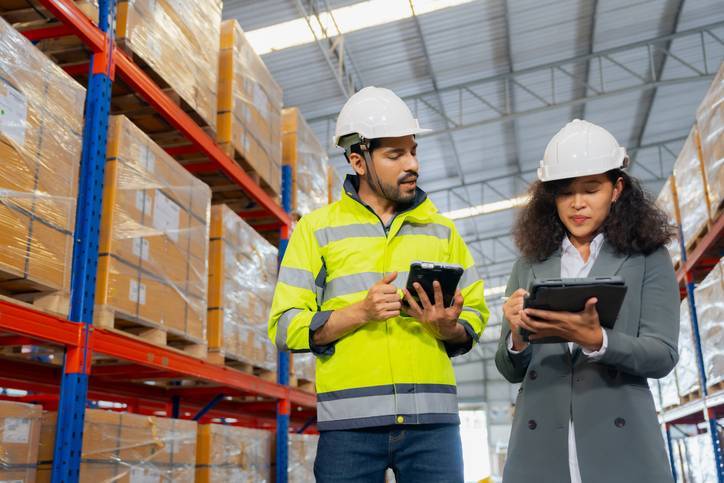
What does 5-on-5 have to do with a continuous improvement cycle?
Summer is a great time for a pick-up game of “5 on 5” basketball. When playing a game of “5 on 5”, the key to success is for the team to work well together, utilize the strengths of each of the players and repeatedly work their process as defined by the coach.
As the process is repeated through the course of the season, the really great teams develop a “chemistry,” which is something that is unseen and not quantifiable, but which gives the team an edge over its competition that leads to success.
The same is true in the business world for companies that want to improve and succeed.
A business team needs to work well together, utilize the strengths of each of the team members and use a process that is repeated over and over. The following continuous improvement cycle used repeatedly will lead to a new “chemistry” within the organization so that the culture begins to change to one of continual improvement.
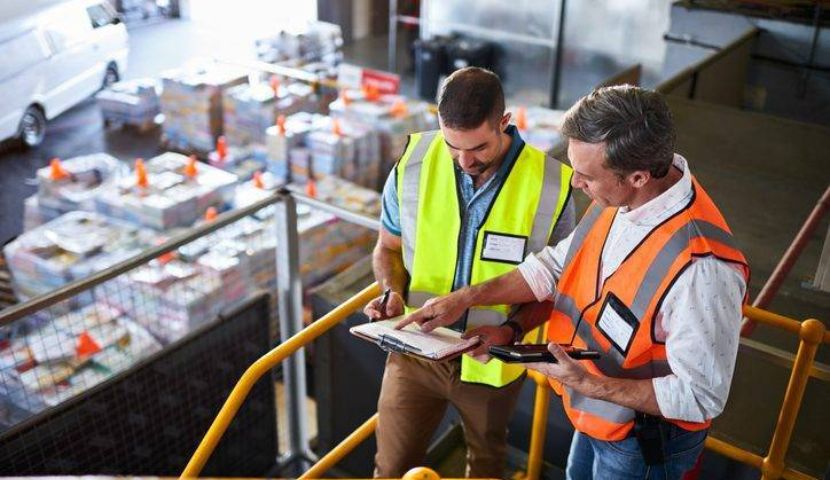
A 5 Step Continuous Improvement Cycle
Define
- Identify the target process
- Organize and empower an improvement team
- Describe the issues, concerns or opportunity
- Collect current performance data
- Create a process map
Identify
- Identify the process customers and suppliers
- Define the process inputs and outputs
- Define the process requirements
Identify wastes and value-added activities - Generate a list of potential improvements
Select
- Establish desired performance goals
- Prioritize the potential solutions
- Establish the selection criteria
- Select the best solution(s)
- Define the desired process
Implement
- Develop an action plan to achieve the goals
- Develop process performance metrics
- Document the solutions(s)
- Test the changes
- Implement per the action plan
Evaluate
- Establish ongoing feedback
- Measure progress per the action plan
- Compare results with desired performance goals
- Determine corrective actions that need to be taken
- Repeat the cycle to define new opportunities
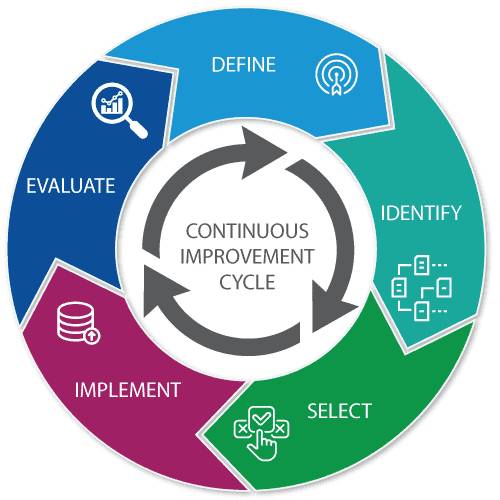
The key to really being successful using this process is the very last step – going back to the beginning and looking for new opportunities. Without this, it is a one-time change, not continuous improvement.
By using this cycle on a formal basis over and over as problems or opportunities are addressed in the organization, inherent use of the cycle will begin to occur since people will become accustomed to it and the culture of the organization will begin to embrace the idea of continuous improvement.
This resulting chemistry that begins to develop will be unseen and not quantifiable but will provide an edge for the organization so that it can succeed within itself and against the competition.
Benefits of the Continuous Improvement Cycle
Implementing a Continuous Improvement Process (CIP) can offer many benefits for manufacturers. For example, companies can see significant improvements in cost reduction through reducing waste and inefficiency which translate to better profit margins or lower operating costs. Continual improvement also leads to increased efficiencies in production and delivery time, and faster adaption to changes in the market or from customer demands.
Businesses should never stop striving to improve their manufacturing practices. While a first step may involve implementing new technology—such as a modern ERP system—continual improvement is key to achieving successful outcomes that drive long-term growth. Implementing the right process improvement methodology that aligns with the goals of the business is fundamental to success.
With so many business processes at play in any kind of manufacturing operation, it can be difficult to manage it all without systematic controls. Utilizing the right tools and techniques to monitor progress, modify plans, and implement changes makes it easier for companies to streamline their processes and continue running efficiently.
If you’d like help understanding how best to implement a continuous improvement cycle in your own business, contact us – we’re here to help you get started.
Table of Contents
More ERP material...
What Is Enterprise Data Management?
From customer insights to supply chain metrics, organizations depend on accurate, timely,…
Top 10 Uses of AI in Food Manufacturing: Enhancing Safety, Quality, and Efficiency
In the face of changing consumer demands and complex supply chains, food…
AI’s Role in Digital Transformation
Digital transformation is about more than just adopting new technologies—it’s about reimagining…