Enterprise Resource Planning (ERP) systems are essential to modern utility operations, allowing data to flow seamlessly across departments, improving efficiency and supporting regulation compliance. But the complexity of ERP implementations can lead to disruptions to operations and unexpected costs if not carefully managed. It’s all too easy for the project to stall or scope creep to set in, derailing progress and delaying ROI.
To help you avoid these setbacks, we explore the top 5 ERP implementation pitfalls in the utility industry.
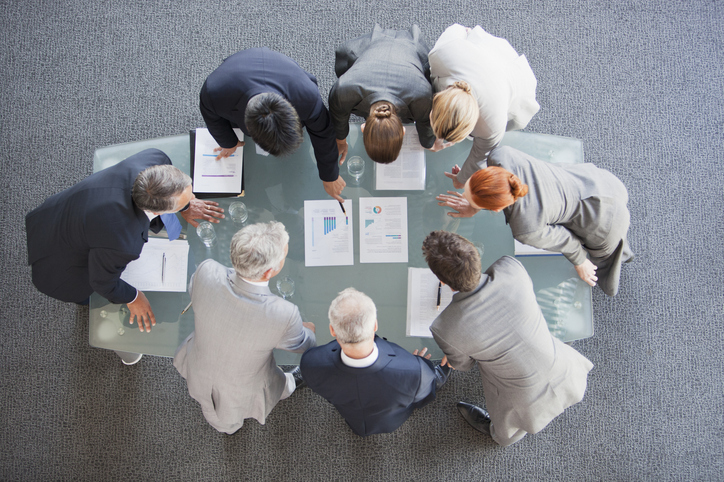
How to Create an ERP Implementation Project Plan
Download this guide to discover a roadmap for starting on your digital transformation journey with ERP.
What Are the Top 5 Pitfalls of ERP Implementation for Utilities?
1. Underestimating Change Management
The Pitfall:
ERP projects aren’t just about technology; they’re also about people. The new ERP will change the way your team works. For your project to be successful, you need to ensure that your team adopts to the new system. But many utility companies overlook formal change management plans as an integral part of their ERP implementation.
The Lesson:
Resistance to change often contributes to hidden costs from ERP adoption. Overcoming it requires a comprehensive organizational change management (OCM) plan which includes strategies for stakeholder engagement, as well as ongoing training and support.
2. Inadequate Data Migration Planning
The Pitfall:
Is your data ready for the new ERP? Poor data quality along with a rushed migration can hinder ERP performance. Whether from legacy systems, inconsistent data formatting, or siloed information from disparate department, utilities often deal with decades of data that’s not ERP-ready.
The Lesson:
Start planning your data cleansing and mapping efforts early in the project. Establish strong data governance processes and ensure users are involved in validating critical data. Be sure to include both IT and Operations teams. Neglecting to clean your data before migration can lead to system errors, inaccurate reporting and lack of trust in the new ERP. By performing trial migrations and test reports in sandbox environments can help ensure accuracy and completeness before go-live occurs.
3. Ignoring Cybersecurity Implications
The Pitfall:
ERP systems contain sensitive information including financial, operational and customer data. As utilities move to integrated digital platforms, their risk of cyber attack increases. Don’t assume that it’s only the software vendor’s responsibility to mitigate the risk.
The Lesson:
A security breach can lead to fines, service disruptions and even loss of public trust. Integrate cybersecurity plans from the start of your ERP project, keeping vendor selection, system design and implementation planning in mind from a security point of view. This can include role-based access, data encryption and third-party risk assessments.
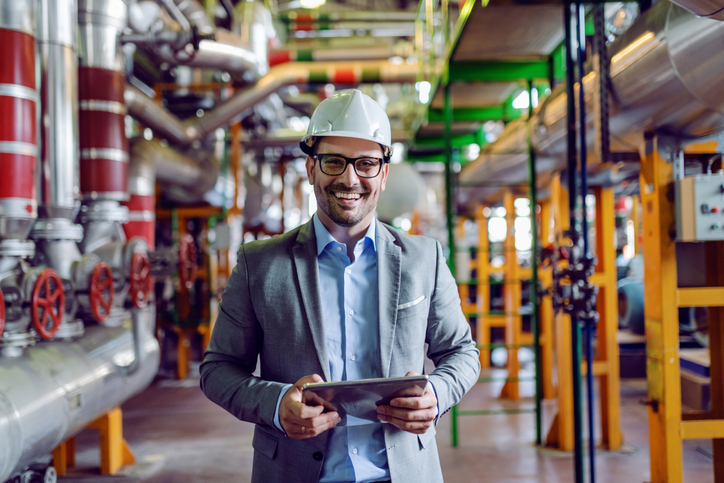
4. Choosing Customization Over Configuration
The Pitfall:
It might be tempting to try to customize your new ERP to follow your current workflows. But heavily customizing your system can increase project costs and limit scalability; not to mention enforcing workflows that may be inefficient.
The Lesson:
It’s key to start your project with an in-depth business process improvement phase to identify inefficiencies, optimize workflows and zero-in on your requirements for the new ERP. Then, carefully select an ERP solution that meets those needs without major customization.
5. Lack of Post-Go-Live Planning
The Pitfall:
Your ERP project shouldn’t come to a stop after go-live is completed. It’s really just the beginning! As you move forward, you’ll need to plan for continuous improvement to realize the full potential of your new system.
The Lesson:
Post-go-live support should include help desk resources, bug tracking systems and a focus on continuous improvement. Allocate resources for necessary system stabilization and enhancements. Also, be sure to establish and track KPIs to measure success and identify areas for improvement.
Ready to start your digital transformation journey?
Utilities ERP Success is Possible—with the Right Approach
For utility companies, implementing a new ERP comes with high risks and high rewards. The key to success lies in a proactive approach to risk management, based on thoughtful strategies and a clearly defined project plan. ERP isn’t just about adding better software, it’s about using the right technology, deployed correctly to enable smarter decision-making, reliable service delivery and agility to prepare for the future.
Need Help With Your ERP Rollout?
Whether you’re just starting the journey, stuck in a stalled implementation or looking to maximize value from your existing system, having the right guidance can make all the difference. Consider partnering with consultants who specialize in utility ERP systems to avoid costly mistakes and build a roadmap tailored to your organization’s needs. Put Ultra Consultants’ decades of experience to work for you. Request your free discovery call today.
Table of Contents
More ERP material...
What Is Enterprise Data Management?
From customer insights to supply chain metrics, organizations depend on accurate, timely,…
Top 10 Uses of AI in Food Manufacturing: Enhancing Safety, Quality, and Efficiency
In the face of changing consumer demands and complex supply chains, food…
AI’s Role in Digital Transformation
Digital transformation is about more than just adopting new technologies—it’s about reimagining…