Production Quality through MES: Guest Blog from IQMS
Manufacturing Execution Software (MES) means different things to different people. I think it depends on a person’s perspective. Are they from a process manufacturing background or a discrete manufacturing background? Are they focused on complex manufacturing or highly repetitive manufacturing? Are they thinking about automation or are they thinking about monitoring, measuring and alerting.
Definition: Monitors and synchronizes the execution of real-time, physical processes involved in manufacturing intermediate and/or finished goods.
I agree with that definition. At IQMS we specialize in the managing and monitoring of highly repetitive discrete manufacturing processes.
Categories of MES
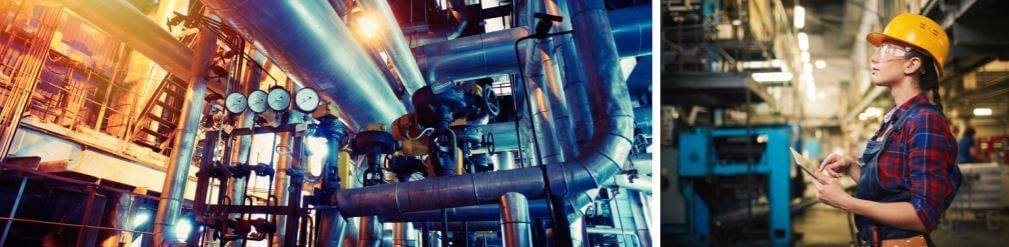
The Manufacturer’s Guide to Business Process Improvement
This eBook shares enterprise technology educational resources specifically developed for the manufacturing and distribution sector.
MES monitoring is divided into three types of measurements:
- Production monitoring – counting the rate that parts are being produced.
- Quality monitoring – examining the condition of the parts that have been produced. Typically their dimensions, weight and appearance.
- Process monitoring – measuring the process variables at the time of manufacturing. Parameters like temperature, pressure, hold time.
Each of the three monitoring types produces actionable information that can be used independently or in conjunction with other monitoring results. For instance, production monitoring by itself can inform production management that:
- The machine is running and producing parts, or the machine has stopped
- When the job that is running is forecast to complete
- If the job is running too slow or too fast (and therefore something is going wrong)
- How many parts have been made and how many parts are left to produce
The simple act of actively (in real-time) measuring the production rate generates an incredible amount of information that can then be back flushed to the plant’s ERP system.
- How much finished goods are available or when they will be available
- How much raw material was consumed and how much more will be required
- How much machine and labor time was consumed in making the parts
- When will the machine be available for the next job
Quality monitoring logically follows production monitoring. Computer measurement devices, e.g. scales, calipers, vision systems, electronic test systems are combined with human inspection to verify that parts have been made to specification. Good parts are marked as good, bad parts are culled, processes that are failing are flagged.
Quality monitoring builds upon the information provided by production monitoring. Further detailing:
- Scrap rates – wasted material, labor and machine time
- Process that are failing or out of control
- Documentation for customers that the parts meet specifications
Process monitoring measures what is happening during the actual moments of production. Was the raw material heated to the right temperature, did the die close with sufficient force, was the part baked for the proper amount of time? Key process variables are recorded in a time series format that is continuously monitored for deviations. Identifying events trending towards boundary limits that predict the production of bad parts.
Process monitoring is also essential to root cause analysis of manufacturing issues. Why is the part too thin? Was the fill time sufficient? Why did the part contain air bubbles? Was the screw pressure too low? Knowing critical process variables at the time of production allows engineers to quickly uncover were issues might have existed during the parts manufacture – root cause analysis.
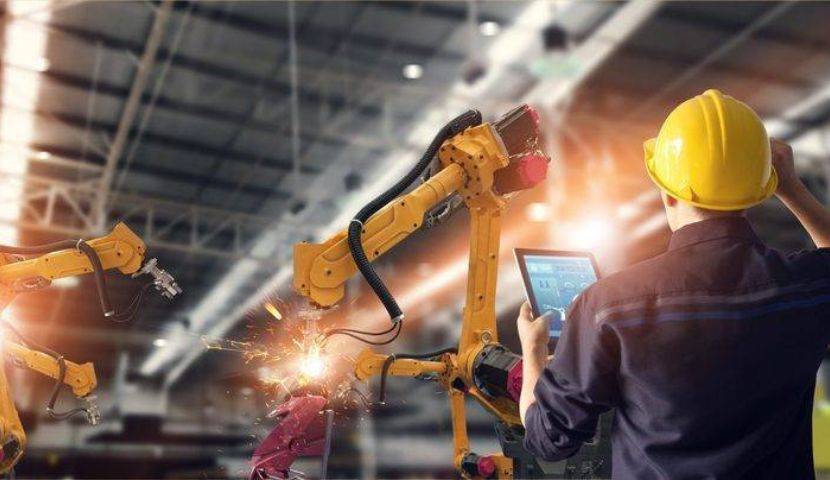
How Production, Quality and Process Monitoring Can be Used to Achieve Predictability and Efficiency on the Plant Floor
Extraordinary manufacturing control, predictability, efficiency and quality can be achieved when production, quality and process monitoring are used in conjunction with each other.
Consider the following case concerning production quality. Production monitoring is tracking the progress of a 10,000 item job. With 6,000 parts remaining to be produced, production monitoring alerts the supervisor that the production rate has slowed and the job is not predicted to complete on time. Near the same time, the supervisor receives a similar alert from the quality monitoring system, it is starting to reject one out of every twenty parts.
The supervisor calls in an engineer who examines the process monitoring data. The barrel temperature of the machines is rising to unacceptable levels, while the fill pressure remains inside the target range. Both the supervisor and the engineer agree the job should be shut down and restarted on a different piece of equipment. Production management uses historical production monitoring data to determine the next best machine to take over the job (sometimes called Runs Best Data). Because the engineer knows the fill pressure was not the issue, he advises production management that the tool itself is not the issue, it was something on the machine. He authorizes the use of the tool on the new equipment and the supervisor initiates the changeover. In 30 minutes the job is up and running with all parameters running within specification on the new equipment.
Meanwhile the engineer is reviewing the production data, quality data and process data. He quickly determines that the production rate slow down and increase in rejected parts began within one minute of the barrel temperature exceeding 950 degrees. The root cause of the failure was the barrel temperature. An inspection of the machines indicates the barrel temperature controls had prematurely failed at 425,000 cycles. The machine is repaired and the barrel temperature control inspection criteria is reset to 400,000 cycles.
MES allows for the automation of production and the visibility and control of production rates, quality and cost.
Taken separately or together, production, quality and process monitoring are at the heart of MES. They allow for the automation of production and the visibility and control of production rates, quality and cost.
Today, manufacturers of all sizes and complexity are adopting MES as a reliable and cost effective way to improve the performance of their business and to delivery top-quality products, on-time to their customers.
You can learn more from this on demand webinar with me and Andrew Bolivar from Ultra Consultants. We explore production quality through MES and more.
The recording of the session is for you to view and share on demand.
By Steve Bieszczat, Chief Marketing Officer, IQMS
Steve is responsible for IQMS’ brand management, demand generation and product marketing. Prior to IQMS, Steve held senior marketing roles at ERP companies Epicor, Activant and Triad. In addition, he has engineering experience at manufacturing companies Automotive Controls (Echlin) and DIT-MCO International. Steve has extensive ERP experience in the retail, distribution and manufacturing sectors, in both organic growth and M&A oriented businesses. Steve holds an engineering degree from the University of Kansas and a Masters in Business Administration from Rockhurst University.
Table of Contents
More ERP material...
Selecting the Right TMS System: Key TMS Features and Trends to Consider
Data analytics holds the ability to highlight inefficient manufacturing processes and enable…
Choosing a CRM System for Your Business
Data analytics holds the ability to highlight inefficient manufacturing processes and enable…
The Undeniable Benefits of Implementing ERP in Food and Beverage Manufacturing
Data analytics holds the ability to highlight inefficient manufacturing processes and enable…