In today’s manufacturing environment, every process from design to shipping yields data that holds the potential to impact product quality, operational efficiency, and profitability. Product data including information related to the product’s specifications, production process, and lifecycle management is key to boosting the bottom line and maintaining a competitive edge.
But if your manufacturing organization is struggling to manage product data, you’re not alone. A recent survey conducted by Tech-Clarity found that more than 80% of respondents indicated a significant effort is needed “to integrate and maintain the integration between MES, quality, maintenance, scheduling, IIoT, and other equipment or machine data.”
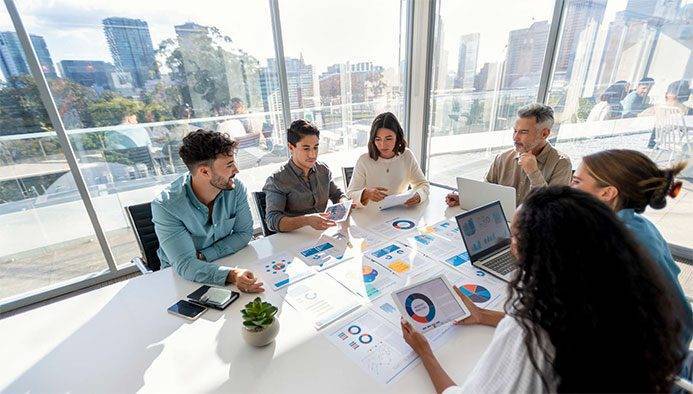
A Roadmap for Business Performance Improvement
Download the eBook to discover a roadmap for implementing process improvement programs to drive business performance improvement.
In this blog, we’ll walk through some best practices you can employ to help manage and analyze your data to gain insights, reduce errors and optimize production.
- Challenges of Managing Product Data in Manufacturing
- What is Product Data Management?
- Benefits of Managing Product Data
- Best Practices for Managing Product Data
- Master Product Data Management with the Ultra Experts
Challenges of Managing Product Data in Manufacturing
While manufacturers realize the importance of managing data, keeping ahead of the constant influx of information gathered at multiple points across the organization is easier said than done. For many companies, product data may be stored in different departments or technology systems including ERP, PLM, MES or others. This data may be isolated and inaccessible when a comprehensive view of up-to-date information is required. These data silos make it difficult for teams to collaborate, leading to inefficiencies, or uninformed decision-making.
Without a single source of truth, many manufacturers struggle with version control and tracking product changes and updates throughout the product lifecycle. The lack of an integrated system can lead to using outdated data and production errors.
Compliance is another area that can be impacted by poor data management. Incomplete or inaccurate data can result in delays, quality control issues, and regulatory problems especially in industries like aerospace, automotive and pharmaceuticals. Stringent documentation and traceability records can be very difficult to manage through manual processes and disparate systems.
What is Product Data Management (PDM)?
Product Data Management (PDM) is the process of managing the data generated during the design, production and post-production stages of a product’s lifecycle. Product data management software can help manage this product-related information in a central repository.
In short, the goal of PDM is to provide centralized access to accurate, product information for stakeholders including engineers, production teams, suppliers, or even customers. With so much data collected across departments, effective PDM prevents issues like siloed data, data duplication and inefficient workflows.

Benefits of Managing Product Data
Managing product data through a centralized platform can improve many areas of the production process. A PDM system helps ensure that all departments and teams work from the same data and promotes collaboration. It also increases efficient operations, reducing time spent retrieving, updating and sharing data. This can lead to shorter production cycles and faster time-to-market.
The right PDM software also improves quality assurance, helping manufacturers identify potential product design or quality issues early in the production cycle. Avoiding rework and material waste also reduces costs.
Finally, a PDM system helps maintain the accurate product data required for regulatory compliance. This level of data management provides full traceability of design, materials and production processes, ensuring compliance to industry standards.
Ready to start your digital transformation journey?
Click the button below to request your free discovery call.
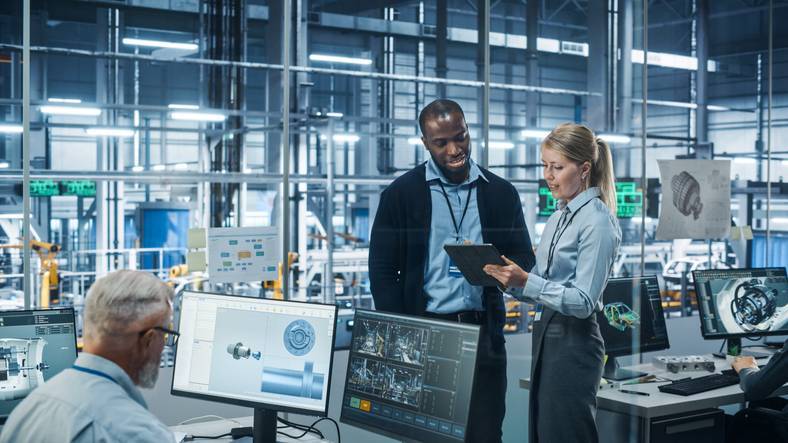
Best Practices for Managing Product Data
To capitalize on the advantages the effective product data management allows, there are some best practices to follow:
1. Implement a Centralized Product Data Management System
A Product Lifecycle Management (PLM) system can manage product data in one place, providing a single source of truth and eliminating data inconsistencies, duplication and version control issues. Key stakeholders can access critical information such as design data, specifications and manufacturing instructions for the entire lifecycle. A central repository also ensures control over access privileges, ensuring data integrity and security, protecting who can access or modify data.
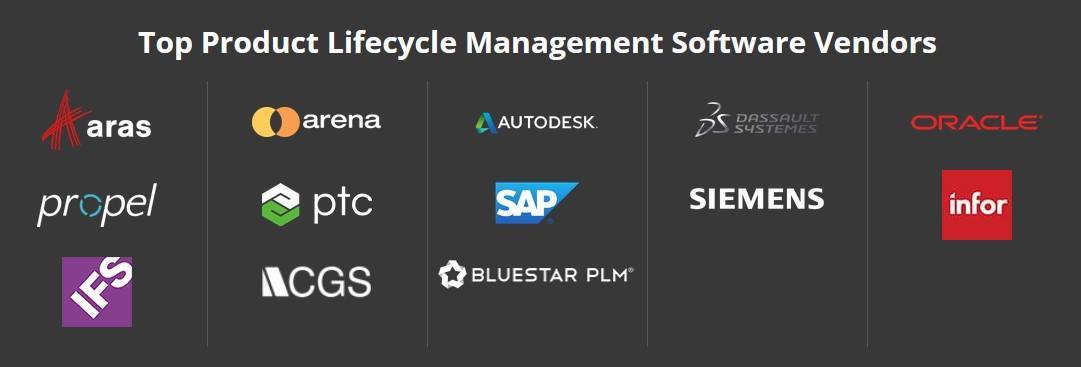
2. Standardize Data Formats and Naming Conventions
Standardizing product data goes a long way in improving data accuracy, reducing errors and facilitating collaboration among teams. Clearly defining naming conventions for product specifications (models, components, and sub-assemblies) and part numbers helps organize product information and makes it easier to locate files. Creating standard templates for data entry of materials, part numbers and tolerances, as well as formats for documentation like drawings and specs, helps ensure consistency and reduce errors.
3. Ensure Robust Version Control
Establishing effective version control ensures that product information is always current and accessible, reducing the risk of errors. Without effective version control, production teams may work from outdated or conflicting data.
Be sure to use clear version naming systems (e.g., v1.0, v1.1, v2.0) to indicate changes in technical specifications. This makes it easy to identify the latest version and track changes over time. Also consider implementing a structured process for making version changes, ensuring any modifications to product information are reviewed, approved and documented. This helps prevent unauthorized changes and maintains consistency in adhering to the naming system.
4. Integrate Product Data with Other Systems
Many manufacturers use a range of software systems like ERP, MES and SCM to manage their operations. Integrating these systems with the right PDM solution helps ensure data accuracy across departments and systems.
For example:
- ERP Integration: By linking your PDM system with your Enterprise Resource Planning (ERP) system, you can synchronize product specifications, materials, and BOMs with inventory, production schedules, and procurement.
- MES Integration: Integrating with Manufacturing Execution Software (MES) ensures that production teams are always working with the latest product data and that product specifications are communicated directly to the shop floor.
- Supply Chain Integration: Integrating PDM with supply chain systems helps ensure that suppliers have the right product data, reducing errors and improving collaboration.
As explained by the Michigan Manufacturing Technology Center, “System integration delivers information to those who need it, where they need it and when they need it.”
5. Prioritize Security and Compliance
Effective data governance can help manufacturers avoid risks from data breaches, regulatory violations, and damage to the company’s reputation. Ensuring that product related data is secure and complies with relevant standards is critical to avoid costly penalties or recalls. Here are some steps you can take to ensure security and compliance.
- Data Encryption: Encrypt sensitive product data to protect it from unauthorized access or breaches.
- Audit Trails: Maintain an audit trail of the entire history of product data modifications to ensure traceability. This is essential for compliance and reporting.
- Compliance Checks: Regularly review data quality to ensure that it complies with industry standards and regulations (e.g., ISO, GMP, or FDA).
Access Control: Implement strict user access controls to ensure that only authorized personnel can access or modify product data.
"Gone are the days when companies had to worry that the competition would copy their final product; now, they have to guard the data that controls the production process as well."
Bryan Crutchfield | Forbes Councils Member
6. Use Data Analytics for Continuous Improvement
Continuous improvement initiatives can yield significant improvements in business process efficiency, waste reduction, and product quality. Analyzing product data can help manufacturers find areas for incremental improvements.
- Performance Analysis: Analyze product performance data to identify areas for improvement, such as reducing defects, improving durability, or enhancing functionality.
- Predictive Analytics: Use predictive analytics to forecast potential issues, such as supply chain disruptions or machine failures, and take corrective action before they impact production.
- Root Cause Analysis: If product defects or production delays occur, analyze product data to identify the root cause and implement corrective actions.
Master Product Data Management with the Ultra Experts
Effective product data management helps ensure product quality, streamline workflows and optimize operations. By implementing a centralized PDM tool, standardizing data formats, enforcing version control, integrating with other systems, prioritizing data security, and using analytics for continuous improvement, manufacturers can significantly improve their product data management practices.
Ensuring accurate real time data across your organization fosters better collaboration and improved decision making among your team, while improving quality control and reducing costs. If you need to improve your processes to better capture and manage data, turn to the Ultra experts. We can help you optimize your existing processes and tech stack to enable better data management, or explore new systems to drive enhanced accuracy, automated workflows, and improved visibility to your key data.
Request your free, no obligation discovery call today to learn more.
Table of Contents
More ERP material...
Selecting the Right TMS System: Key TMS Features and Trends to Consider
Data analytics holds the ability to highlight inefficient manufacturing processes and enable…
Choosing a CRM System for Your Business
Data analytics holds the ability to highlight inefficient manufacturing processes and enable…
The Undeniable Benefits of Implementing ERP in Food and Beverage Manufacturing
Data analytics holds the ability to highlight inefficient manufacturing processes and enable…