It’s no secret that success in business is a constantly moving target, with demand increasing for personalized products, faster delivery, and sustainable manufacturing methods. Today’s manufacturing companies look to stay ahead of the curve—and the competition—by embracing agile manufacturing practices.
Agile manufacturing focuses on flexibility, collaboration and customer-centric practices. But what part does it play in business transformation and why is it becoming an essential part of modern manufacturing? This blog post will explore the rise of agile manufacturing, drivers of its adoption, the business impact, and some challenges with its implementation.
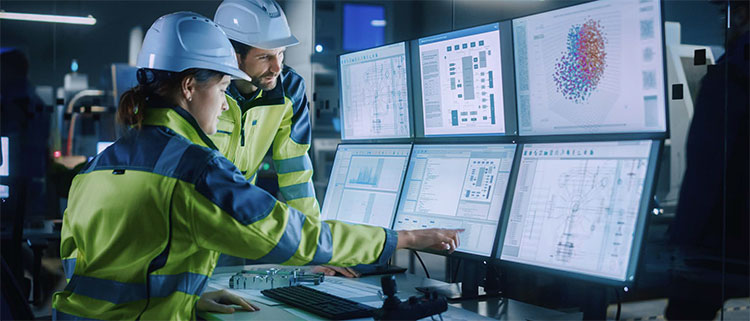
Solving Manufacturing Challenges with Smart Factory-Ready ERP Systems
Download the eBook to discover how ERP systems optimized with smart factory technology can help you overcome common manufacturing challenges.
The Rise of Agile Manufacturing
Borrowed from software development, agile manufacturing promotes the ability to quickly adapt to changes through feedback loops and iterative development. In the manufacturing environment, it brings quick decision-making, real-time adjustments and flexible production schedules, as well as increased collaboration with suppliers. In contrast to traditional manufacturing’s longer lead times, batch production and less responsiveness to customer needs, agile manufacturing promotes a fluid, responsive and efficient approach.
Today, businesses are increasingly emphasizing speed and adaptability, influenced in part by the adoption of technology including the Internet of Things (IoT), artificial intelligence (AI), and automation. Global supply chains and demand for sustainability, rapid prototyping and product customization also contribute to the push toward agile practices.
Key Drivers of Agile Manufacturing Adoption
As industries face increasing pressure to meet consumer expectations, adapt to market changes and improve operational efficiency, agile manufacturing has emerged as a key strategy for driving profitability and future-proofing businesses. By fostering flexibility and responsiveness in production, agile manufacturing helps companies stay competitive.
This approach not only accelerates time-to-market, but also enhances supply chain resilience, integrates cutting-edge technologies, and supports sustainability efforts. Understanding the key drivers behind agile manufacturing adoption reveals how companies are navigating today’s market challenges while positioning themselves for future success.
1. Demand for Customization and Personalization
Whether in their electronics, food or clothing, today’s customers expect customized products. Agile manufacturing enables companies to quickly adapt production lines to respond to shifts in customer preferences. They can be prepared to respond to individual orders or mass personalization without extended delays. This allows them to improve customer satisfaction or even expand into niche markets.
2. Faster Time-to-Market
Agile manufacturing allows businesses to reduce their time-to-market for new products. Through iterative development, it breaks down the production process into smaller, manageable tasks, accelerating product development. This lets companies quickly respond to market demands for new products.
3. Supply Chain Resilience and Flexibility
The pandemic shed light on the vulnerabilities of global supply chains. As a result, many businesses began to reconsider their approach to procurement and logistics. Agile manufacturing helps facilitate more resilient networks that are better able to adapt to disruptions. By taking advantage of real-time data through enhanced supply chain management, companies can use demand forecasting, supplier collaboration, inventory alerts and more to respond to fluctuations.
“The geopolitical shifts and trade disruptions we're set to experience in 2025 will require the creation of more agile supply chains.“
Rachel Brown | Manufacturing Digital
4. Technology Integration and Automation
New technologies like AI, robotics and IoT continue to change the landscape of manufacturing and enable to push to agile practices. They allow manufacturers to automate repetitive and manual tasks, and analyze data and metrics to make informed decisions. For example, predictive maintenance—made possible by AI—can help prevent downtime by predictive when equipment is likely to fail. Robotics and automation support agile processes by reducing production time. As these technologies become more commonplace, manufacturers can streamline operations and be able to respond rapidly to changing market demands.
5. Sustainability and Lean Manufacturing
Agile methodologies are also playing a role in sustainability initiatives and lean manufacturing processes. From minimizing waste and optimizing resource use, to being able to quickly switch to more sustainable materials or adapting more environmentally-focused production processes, agile manufacturing offers a framework for achieving these goals.
Ready to start your digital transformation journey?
Click the button below to request your free discovery call.
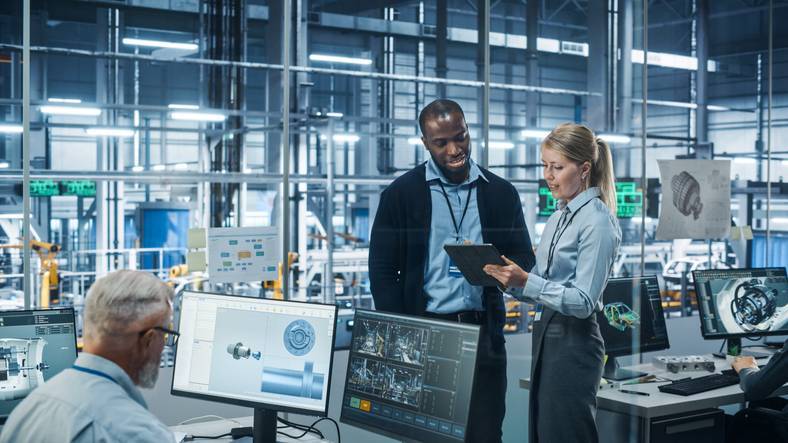
The Business Impact of Agile Manufacturing
Agile manufacturing is transforming how businesses operate, creating benefits that impact everything from efficiency to the customer experience. By embracing flexibility and continuous improvement, companies can streamline their processes, reduce waste, and improve productivity.
This approach not only helps businesses respond to changing market demands, but also drives cost reductions, enhances decision-making, and builds a competitive edge.
1. Improved Operational Efficiency
By prioritizing continuous improvement, collaboration and frequent small changes, agile manufacturing takes a unique approach to operational efficiency. Manufacturers can use real-time data analytics to identify bottlenecks, reduce inefficiency and improve throughput.
Because of its flexibility, agile manufacturing can also lead to fewer delays and more streamlined processes. By breaking down complex projects into smaller pieces, it’s easier to allocate resources, reduce waste and increase productivity.
2. Enhanced Customer Satisfaction
Agile manufacturing drives higher customer satisfaction by enabling businesses to deliver high quality products and fast response to customer demands and market trends. This agile approach helps build brand loyalty and strong customer relationships.
3.Cost Reduction
Agile methodologies can drive cost reductions by establishing more efficient production practices. This is especially relevant given the current potential for tariffs to impact the manufacturing sector in the near term.
By emphasizing flexibility, manufacturers can reduce the need to carry large inventories, minimize production delays and limit waste. Plus, advanced technologies like automation, machine learning, and predictive maintenance driven by artificial intelligence, help companies lower labor costs while establishing efficient production processes. These savings can then be reinvested in innovation or used to offer competitive pricing to customers.
4. Increased Competitive Advantage
All companies are after a way to either build or maintain their competitive edge. Businesses that can quickly produce high quality products and customize offerings are well-positioned to stay ahead of the competition.
Agile manufacturing allows businesses to quickly adapt to changes in the market, whether it’s new consumer demands, supply chain disruptions, or technological advancements. This adaptability is a key competitive advantage in meeting today’s market conditions
5. Better Decision Making
It’s well past time to say goodbye to the data silos of the past. Agile manufacturing practices rely heavily on data-driven decision-making.
The use of AI, IoT, and other technologies provides manufacturers with insights into each stage of the production process, from the shop floor to the shipping dock. With access to real-time data, decision-makers can set KPIs, make informed choices, optimize production schedules, and address issues before they become major problems. The ability to make quick, data-backed decisions leads to better outcomes and ensures that businesses remain responsive.
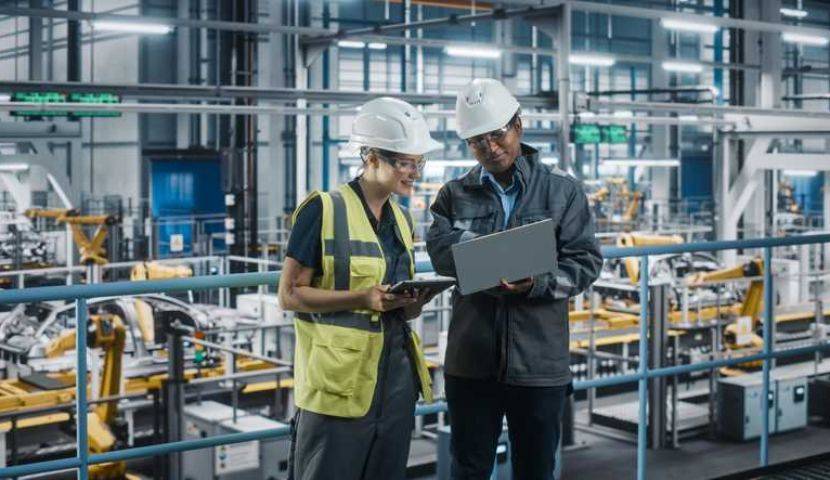
Challenges and Considerations in Implementing Agile Manufacturing
While agile manufacturing can offer benefits, businesses must consider several challenges when putting it into practice as part of a digital transformation. The shift to agile requires not just adopting new technologies but also rethinking entire production processes and workflows.
The integration of advanced systems such as AI, robotics, and IoT can disrupt existing operations and requires alignment across departments to ensure efficiency. Plus, companies need to manage the risks associated with rapid changes to their tech stack, including potential system failures or bugs. Businesses also face the challenge of maintaining production quality while adopting an agile, iterative approach that requires frequent adjustments and improvements. Here are some specific areas that should be considered when weighing the adoption of agile manufacturing methods.
1. Initial Investment
Integrating AI, robotics and IoT technology often requires significant upfront investment. Beyond the technology itself, implementation also depends on additional training programs for employees.
2. Change Management
Beyond the ins and outs of using the technology, transitioning to agile manufacturing also requires a shift in mindset. Resistance to change can be a major barrier to adoption and companies must invest in change management strategies to ensure successful implementation. A recent survey by Manufacturing Leadership Council found “the most significant roadblock to implementing a smart factory strategy is an organizational structure or culture that resists change.”
3. Supply Chain Coordination
Agile manufacturing relies on close coordination with suppliers to ensure that materials are delivered on time and meet quality standards. Building and maintaining strong supplier relationships is essential to avoiding disruptions.
4. Data Security and Privacy
The use of advanced technologies like AI, and data analytics in agile manufacturing raises concerns about data security and privacy. Manufacturers must invest in strong cybersecurity measures to protect their business data and customer information. As manufacturing systems become more interconnected, the risk of cyberattacks increases, and businesses must take steps to mitigate these threats.
Conclusion
Agile practices are transforming the manufacturing industry, driving greater efficiency, responsiveness, and customer satisfaction. With the ability to adapt quickly to changes in market demands, customize products, and streamline production processes, an agile approach to manufacturing offers companies a competitive edge.
To learn more about what’s involved in an agile transformation, schedule your free discovery call today. The Ultra experts can help build a roadmap for your business—either as part of a digital transformation or as a stand-alone process improvement project. Let’s talk about your business objectives and how you can maximize performance, reduce inefficiencies, and drive growth.
Table of Contents
More ERP material...
What Is Enterprise Data Management?
From customer insights to supply chain metrics, organizations depend on accurate, timely,…
Top 10 Uses of AI in Food Manufacturing: Enhancing Safety, Quality, and Efficiency
In the face of changing consumer demands and complex supply chains, food…
AI’s Role in Digital Transformation
Digital transformation is about more than just adopting new technologies—it’s about reimagining…