Reducing operational costs, improving production and delivery, making decisions based on real and factual data and driving business growth is a key mandate for businesses in the manufacturing and distribution industries. This is where business process efficiency comes into play.
In this article, we will look at:
- What business process efficiency is
- The significance of efficient processes
- Steps for streamlining processes
- The role of process automation in efficiency
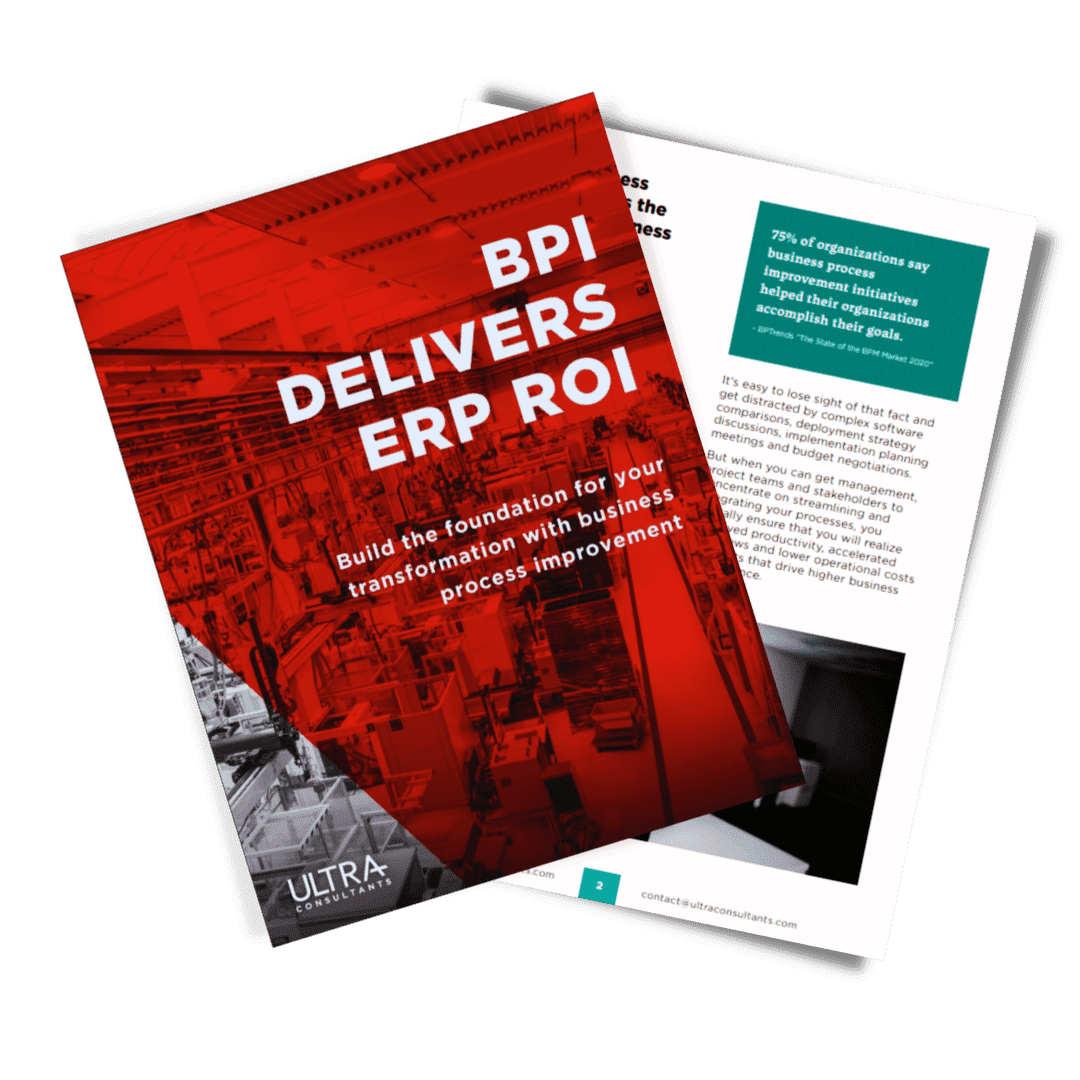
Business Process Improvement (BPI) Delivers ERP ROI
Download the guide to gain valuable insight into the BPI process, and see how to maximize the ROI of your ERP project.
Understanding Business Process Efficiency
A good business is one that has proper systems and procedures. In business process efficiency, the focus is on how effectively different workflows and operations of your organization perform in terms of time and resources invested. The objective is to streamline processes, eliminate obstacles and achieve objectives with minimum efforts.
More efficient processes enable your business to run as a single entity, enhance employee efficiency and produce high-quality products and services that meet the needs of your customers. It is important to analyze and optimize workflows in order for your organization to run smoothly, avoid delays and succeed in the dynamic business world of today.
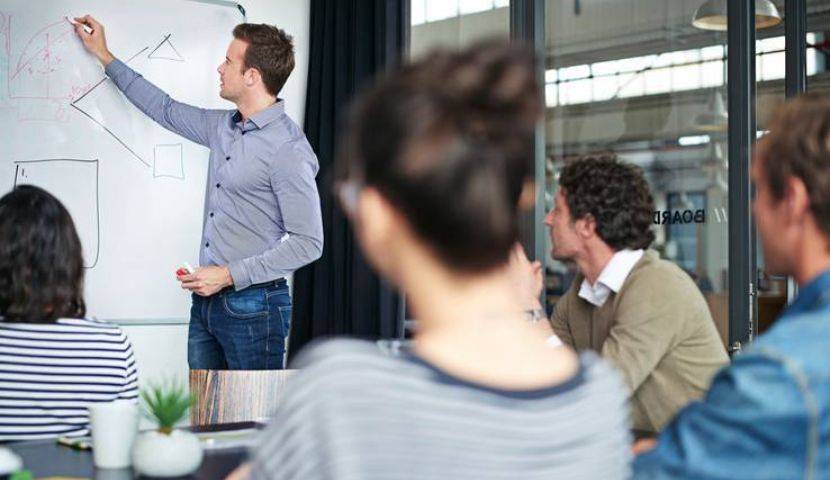
The Significance of Efficient Processes
Streamlining operations is pivotal for organizations aiming to thrive. Refining workflows and systems can spark increased productivity, fewer mistakes, lowered expenses, enhanced adaptability and happier clients. Here are reasons why having efficient business processes matters to any business:
1. Increased Productivity
Efficient processes have one of the biggest benefits: improved productivity. When your organization is able to do away with unnecessary steps and repetitive tasks, your employees can spend this time on dealing with other value-adding activities. This brings about streamlined workflows and, in turn, your employees are able to complete their core responsibilities faster.
Efficient processes also bring about the creation of standardized procedures for common tasks such as receiving procedures in inventory management which creates consistency across teams in your organization. Here, protocols are documented, and this minimizes variation in output. It also enables new hires to be brought up to speed quickly.
2. Minimized Errors
Unclear expectations often lead to mistakes and errors. Efficient processes outline exact requirements and instructions for each step. This minimizes ambiguity and ensures employees understand what needs to be done. Clear guidelines result in work being completed correctly the first time, minimizing costly errors.
Even the most skilled employees make occasional mistakes. However, when processes leverage technology solutions, there are fewer opportunities for human error. Automated systems complete tasks precisely according to programmed specifications every single time.
Implementing quality control checkpoints along the process enables errors to be identified and corrected early. Rather than defects reaching the customer, they can be addressed internally before work is marked as complete. This proactive approach enhances quality and accuracy.
3. Reduced Operational Costs
An inefficient process can bring about a major loss to your organization. Let’s use this scenario, your inventory has an inefficient process in the form of holding onto excessive inventory. Your business has to pay for the storage of this inventory which leads to high storage costs, tied-up capital and potential for product obsolescence. However, if this process were efficient, your business would not have to pay for these costs, resulting in significant savings over time.
Bloated processes require excessive amounts of labor, time and systems to complete. Slimming down workflows reduces resource utilization across the board. Less employee time, materials and infrastructure are needed to produce the same output at a lower total cost.
When errors occur, rework is often required to correct issues before work can be delivered. However, this ties up additional labor and material resources. Efficient processes minimize mistakes, cutting down on costly rework procedures. Doing the job right the first time is always the most cost-effective approach.
“Employees are prone to errors, and these errors can be detrimental to your business operations. Improving process efficiency ensures consistency and accuracy in executing tasks, eliminating the risk of human error.”
Marcus Law, Editor-in-Chief, Technology Magazine
4. Increased Flexibility to Changes
Businesses are always evolving, and standardized efficient processes set out solid foundation for adapting your business to your changing needs. Efficient workflows are designed with change in mind. When you introduce a new technology such as an ERP system into an existing business process, you do so without disrupting the wider work sequence. Your existing processes and protocols can be updated in a moment’s notice, and therefore your employees can seamlessly adjust without having to learn about new workflows.
Organizational agility is brought about by team members who are cross-trained across multiple processes. If workload distribution needs to shift quickly, existing employees have the necessary knowledge and skills to take on new assignments with minimal ramp-up time.
5. Enhanced Customer Satisfaction
Customers expect fast turnaround times and are more satisfied when work is delivered quickly. Efficient processes allow your organization to dramatically shorten production cycles and exceed customer expectations. This positively impacts brand reputation and loyalty.
When defective work reaches customers, it erodes trust and satisfaction. However, efficient procedures enable your organization to catch and correct issues before they impact customers. This allows you to increase customer satisfaction by delivering high-quality products and services.
Ready to start your digital transformation journey?
Click the button below to request your free discovery call.
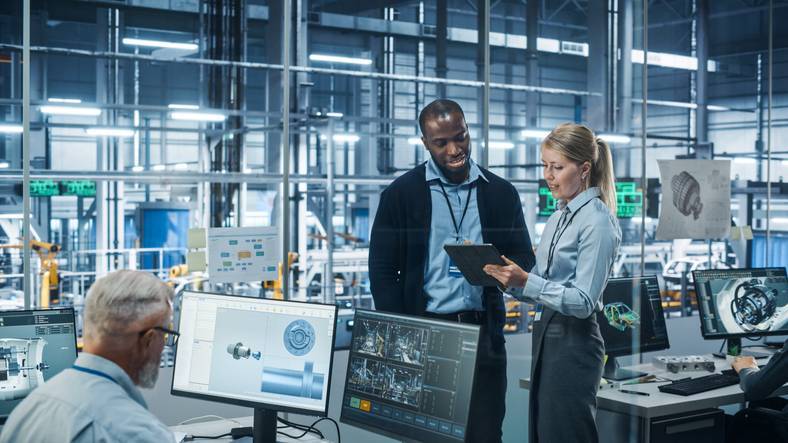
Streamlining Processes: Steps to Improve Process Efficiency
With the growth of your businesses, there are bound to be complex processes which become redundant and overly riddled with inefficiencies. For example, when your business is just starting out, your supply chain is simple to manage because you are sourcing materials from a few suppliers and in smaller volumes.
But as the business grows, you start sourcing from global and diversified vendors which requires complex transportation logistics. You cannot manage all these aspects on the same system as you were starting out.
So, to help streamline your business and avoid the challenges that come along with it, follow these five key steps:
1. Assess Existing Processes
Before your business starts thinking about implementing new technologies or processes, understanding the existing process is crucial. Current processes must be assessed thoroughly so as to identify pain points, shadow processes and areas that need improvement. Assessing the existing processes involves:
Documenting All Processes
Map out all major workflows and procedures from start to finish using models such as Business Process Modeling Notation (BPMN) diagram and Value Stream Chart (VSM). Outline each:
- Process flow
- Stakeholders involved
- Systems and tools used
- Inputs and outputs and metrics.
The information obtained in this stage allows you to have a holistic view into your actual business processes. Skipping this step will only result in your organization improving the wrong processes.
Analyzing for Inefficiencies
Look for redundancies, duplications, delays and steps that do not add value. Check for deviations from documented procedures. Gather data on cycle times, defect rates and costs associated with rework caused by ineffective processes.
Identifying Pain Points
Conduct stakeholder interviews, surveys and focus groups to uncover pain points. Look for manual workarounds, lack of adequate training and miscommunications that disrupt workflows. Deeply understand user frustrations and challenges.
Quantifying Areas of Improvement
Use process analysis techniques such as value stream mapping to quantify savings from reducing delays, defects and non-value-adding steps. Build an economic case for process changes.
“To identify areas where you need to improve your processes, regular feedback from both employees and management and vice versa is crucial.”
Gordon Tredgold, Entrepreneur Leadership Network
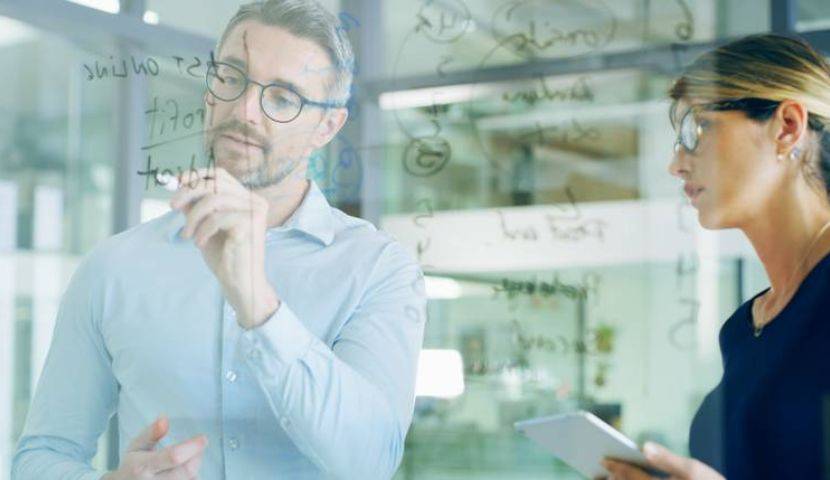
2. Define Business Goals and KPIs
This is the phase where you try to find clear objectives for improvement. To achieve this, consider asking the following questions:
What Business Goals Do You Want to Achieve?
- Are you aiming to boost sales by 15%?
- Cut production costs by 5%?
- Improve customer retention by 10%?
- Align process changes directly with your key business goals.
How Will You Track Progress?
To track progress, establishing quantifiable key performance indicators (KPIs) such as revenue growth, defect rates, cycle times and customer satisfaction scores is crucial. KPIs give you important information that is supported by data, enabling you to assess the effectiveness of improvements.
Who Are Key Stakeholders?
Get buy-in from managers overseeing each process area. With stakeholders on board, you are sure of their cooperation throughout the entire process and therefore an effective implementation process.
3. Redesign Business Processes
With goals and metrics defined, you can redesign your business processes for optimal efficiency. To improve business efficiency, you may have to implement new software and technologies. Furthermore, hiring project managers may also be needed.
Eliminate Non-Value-Adding Steps
Cut out redundancies, manual workarounds and steps that are not critical to the process goal. Simplify workflows.
Improve Process Flow
Optimize the sequential flow of process steps. Look for blockages and move bottlenecks upstream. Add parallel steps where possible.
Standardize Procedures
Document standardized procedures to ensure consistency across your organization. This boosts quality and enables easier training.
Incorporate Automation
Automate repetitive, rules-based tasks through workflows and technology such as robotic process automation (RPA). This reduces costs and improves accuracy.
Monitor with Real-Time Data
Build in real-time performance monitoring using process mining software. Access to real-time data enables agile decision-making.
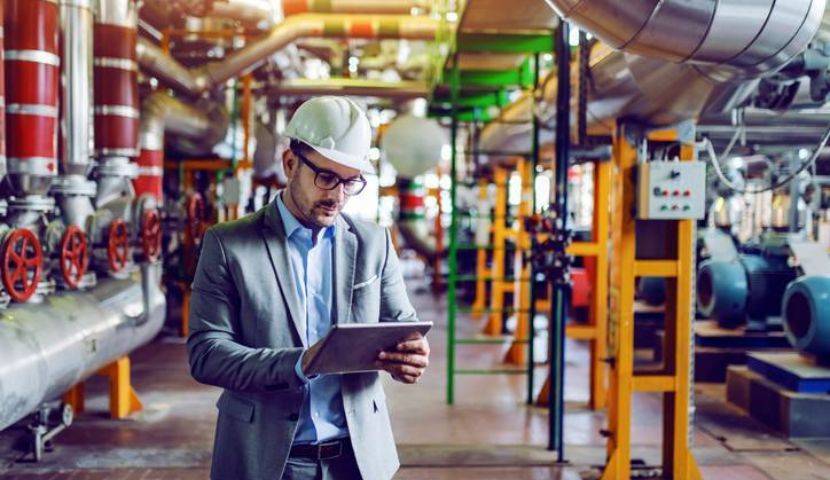
4. Implement the Improved Process
With the process redesign complete, focus on effective implementation:
Phase in Changes
Consider phased implementation, which involves piloting changes on a small scale before you can expand to full organizational implementation. Phased implementation provides an opportunity to resolve any issues that may arise before organization-wide adoption.
Provide Proper Training
Technology is only as efficient as the users who use it. Therefore, it is crucial that your staff have the knowledge to use the new technology effectively. Conduct comprehensive training so that your staff are able to follow the redesigned workflows.
Assign Process Owners
To maintain accountability, appoint process owners to spearhead changes. Provide them with authority to address implementation obstacles.
Solicit Ongoing Feedback
Actively gather feedback from frontline staff throughout and after rollout. Their insights will allow further refinements to the process.
Recognize Quick Wins
Highlight areas where the new process is working well from the start. These quick wins will generate enthusiasm and momentum for full adoption across your organization.
5. Monitor, Measure and Optimize
The work doesn’t end after implementation. You need to continuously monitor, measure and optimize the process:
Monitor KPIs
Track process performance indicators (KPI for short) in real time using visualization dashboards. Alert process owners to any metrics trending unfavorably from targets.
Conduct Audits
Perform regular process audits and self-assessments to check for adherence to standardized procedures. Check that the required controls are actually in place.
Analyze for Further Gains
Keep analyzing process data for new optimization opportunities. Look for small improvements in the process.
Keep Improving
Regard process improvement as an ongoing task, not just an isolated project. Create a continuous improvement culture to encourage a team approach to improving processes.
Conclusion
Having an efficient business process forms a backbone for any successful organization. However, to achieve this, your business needs to constantly evaluate, improve and measure process efficiency because they all tie to optimizing operations, enhancing employee productivity and delivering exceptional products and services to customers. With efficient business process management, your company cuts down on operational costs, increases efficiency and improves customer satisfaction.
At Ultra Consultants, we specialize in helping your organization assess and enhance operations and technology capabilities to maximize process efficiency. We bring seasoned expertise to identify opportunities for improvement, implement solutions such as automation and digitization and measure ongoing impact. Get started on your business process efficiency initiative by requesting your a free discovery call with the Ultra team today.
Table of Contents
More ERP material...
The Undeniable Benefits of Implementing ERP in Food and Beverage Manufacturing
Data analytics holds the ability to highlight inefficient manufacturing processes and enable…
Emerging Technologies in Manufacturing Driving Business Growth
Data analytics holds the ability to highlight inefficient manufacturing processes and enable…
How Food Production ERP Improves Manufacturing Efficiency
Data analytics holds the ability to highlight inefficient manufacturing processes and enable…