BUSINESS PROCESS IMPROVEMENT
Manufacturing Q&A: Causes and Cost of Recalls, and the Role of ERP in Traceability
Why do manufacturers need a business solution that includes strong traceability capabilities? The simple response is that they can’t afford not to.
Without an effective plan to manage and mitigate a recall, a hard-earned positive reputation and brand image could be irreparably damaged. The bottom line can take a huge hit, and, in a worst-case scenario, bankruptcy and significant legal liability are possible.
Despite the significant negative impact of a recall, manufacturers around the globe often are unprepared. And, for a variety of reasons, industries of all kinds are also experiencing an increased number of recall events in the past several years.
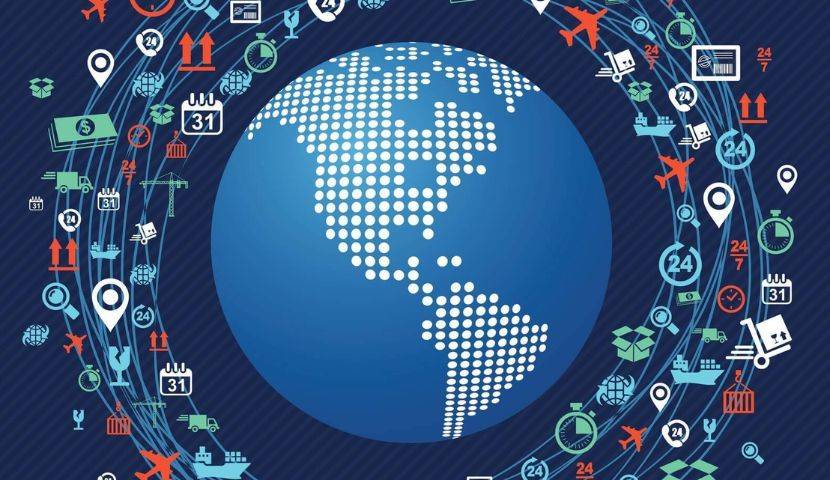
Ultra Senior Consultant Dave Lechleitner recently talked with SYSPRO Product Operations Manager Roger Landman. Here is what Roger had to say about the causes and cost of recalls:
Dave Lechleitner (DL): Why are companies seeing an increase in recalls?
Roger Landman (RL): First, there’s been a greater consolidation of suppliers. The result of this consolidation is that fewer suppliers are fulfilling more and more of the demand in an industry. This then causes a ripple effect – due to the huge volumes of sales by these select few suppliers, a single defect will affect every customer that they support. Consider Takata and their airbag issues or the more recent Boeing 737 Max issues.
- Beyond the ripple effect, it’s important to understand the reasons behind the increase:
Governments are increasing regulations across a wide variety of industry verticals. - Complex global supply chains make it difficult to accurately trace products.
- Consumers are leveraging social media to learn about, report and publicize quality problems.
- Cost-cutting pressures are leading to undisclosed replacement of original, approved parts or ingredients with substandard ingredients or parts, and cross-contamination.
The question is, ultimately, what company cannot afford to have a fully integrated traceability system that is fully functional?
DL: Exactly. We often tell our manufacturing clients that traceability, recall management and quality systems are business-critical, and that the cost of a recall is likely to be high – and will not only be financial.
RL: Every time I’ve been involved in a product recall, it was not cheap. Of course, the cost is difficult to determine up-front. It always starts off as a worst-case scenario, but then you investigate and find the root cause. Which helps you mitigate the extent of the final claim. But that is a lot of work, and requires a fully functional traceability system. Any suspect material that cannot be cleared from suspect status must be removed from the market. And this is where the costs quickly add up.
These four real-life examples show how high the financial, business and human cost of recalls can be:
In 2016, Samsung, the world’s largest smartphone maker was forced to discontinue and recall the Galaxy Note 7 after some units started bursting into flames. Samsung was forced to recall 2.5 million of the devices, some of the priciest smartphones on the market, costing the company billions.
In 2009, a salmonella outbreak at Peanut Corp. of America, an obscure, privately-held peanut processing company in Georgia, ended up killing nine people and sickening hundreds of others. More than 3,913 different products from 361 different companies had to be recalled. Wary consumers shunned peanut butter, driving down industrywide sales by 25%. Peanut Corp. declared bankruptcy and went out of business.
In another case, defective tires installed on Ford SUVs and pickup trucks were linked to 271 deaths and more than 800 injuries in the United States alone. Firestone and Ford blamed each other for the tire failures, but ultimately both companies were on the hook. In 2000 and 2001, Firestone recalled 6.5 million tires, while Ford recalled and replaced 13 million. The Firestone brand survived the scandal but its 100-year relationship with Ford was severed forever.
In the final case, known as “the recall that started them all,” seven people in the Chicago area died in 1982 after ingesting Extra-Strength Tylenol that were laced with cyanide. Tylenol maker Johnson & Johnson spent more than $100 million on recalling 31 million bottles of its best-selling product.
The bottom line: Modern ERP solutions offer powerful support for quality and traceability systems, and comprehensive visibility into supply chains – a combination that enables effective governance, drives regulatory and quality compliance, and minimizes the cost and complication of recalls.
To learn more about recalls, their causes and their costs, view this three-minute webinar excerpt.
To take a deep-dive into traceability, hear about the latest legislation and regulation around the world, and learn about SYSPRO ERP’s approach to traceability, watch this webinar – “Product Recalls: How Manufacturers and Distributors Can Stay Vigilant with Traceability.”
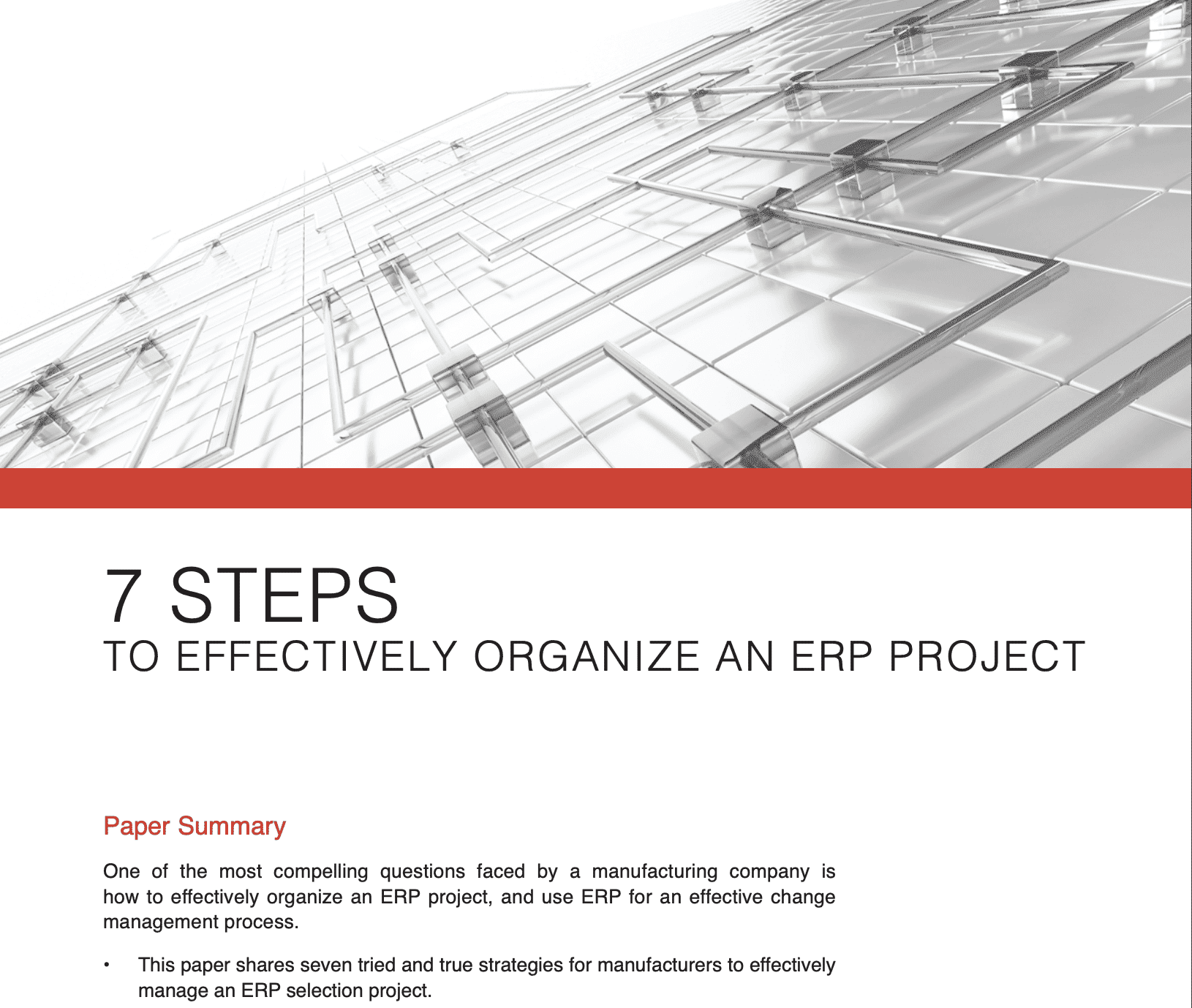
7 Steps to Effectively Organize an ERP Project
The 7 Steps to Effectively Organize an ERP Project is designed for ERP project teams from today’s forward-thinking manufacturing and distribution organizations.
Read tried and true strategies for manufacturers to effectively manage an ERP selection project. See what it takes to be successful and more with this Download.
Table of Contents
More ERP material...
Selecting the Right TMS System: Key TMS Features and Trends to Consider
Data analytics holds the ability to highlight inefficient manufacturing processes and enable…
Choosing a CRM System for Your Business
Data analytics holds the ability to highlight inefficient manufacturing processes and enable…
The Undeniable Benefits of Implementing ERP in Food and Beverage Manufacturing
Data analytics holds the ability to highlight inefficient manufacturing processes and enable…