Guest Post By Jon D. Devine, Infor
The term “Industry 4.0” is a popular discussion topic in manufacturing forums. But what does the concept mean to manufacturers in real life?
To start, finding an agreed-upon definition of this concept is surprisingly elusive. According to Wikipedia, Industry 4.0 is “The on-going automation of traditional manufacturing and industrial practices, using modern smart technology.” But most industry experts will add to this, explaining how automation will allow for a never-before-seen ability to capture data, which, in turn will, unveil previously hidden truths and success paths that would otherwise not be identified.
Why do we see different perspectives on Industry 4.0? Perhaps it occurs during the conversation about a newer, shinier future – a future where some could feel lost, disconnected or, worse yet, that Industry 4.0 requires so much change that maybe they’ll just stay behind where things are comfortable, and they can keep making widgets the way they always have.
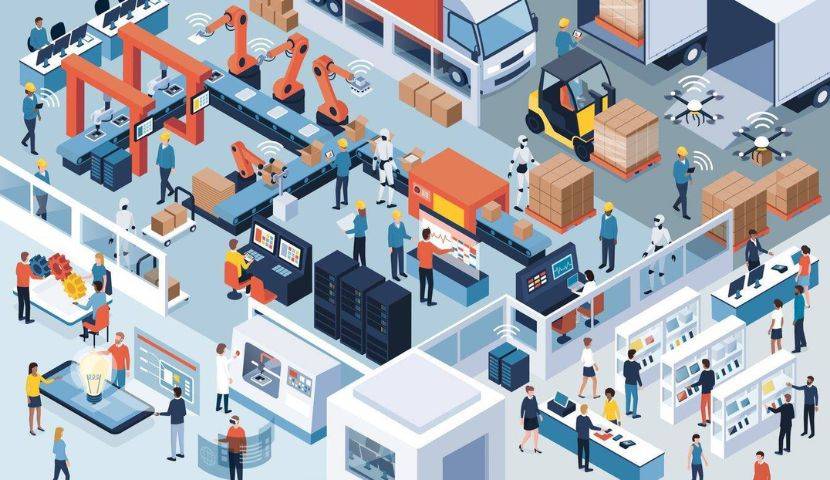
Know Why You Need Industry 4.0 Technologies
Fear of the unknown is a normal human response. Do I have to go to Industry 4.0? What happens if I don’t? Can I go a little or a lot? (And what does that even mean?) These are all valid inquiries, and we’re smart enough to know that just because we can do something with technology doesn’t automatically mean we should.
I believe we see different perspectives because people see different levels of risk and value in any changing situation. In our excitement and anticipation of a better manufacturing future, we’ve described a world full of new benefits, but we may have glossed over how to get there.
We know we want to be better. But before we pay for it, we need to know what the returns are. For sure, we want to know we’re moving in the direction of the good and the positive, not contributing to some sort of an Orwellian future or science fiction movie plot gone horribly wrong.
It is then, a necessary condition that to truly support Industry 4.0, responsible manufacturers must be able to answer why they want or need it, what they want from it, and what it requires.
If the necessary change seems too monumental, the trip gets cancelled before it even begins. As leaders in the business, we have the opportunity and responsibility to show that the shift to Industry 4.0 doesn’t have to be a radical change from one era to another. In fact, we can demonstrate how it’s more of a planned evolution than a startling metamorphosis. We’re talking little steps, not huge leaps.
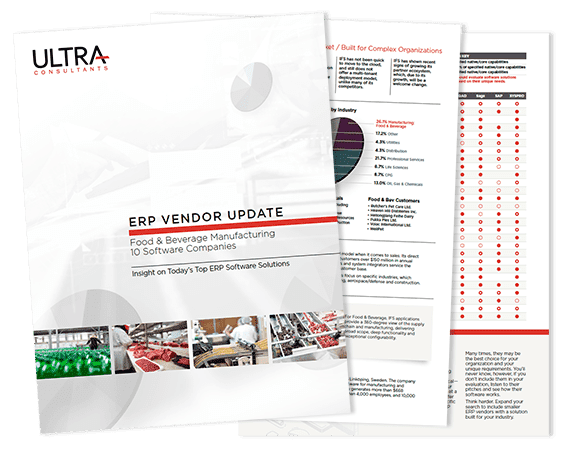
ERP Vendor Update: Food & Beverage Manufacturing
The ERP Vendor Update offers a close-up look at today’s top Food & Beverage software solutions. With more information – and more real insight – than typical software overviews, the report presents complex data clearly and enables easy analysis and comparison.
However, if you’re still feeling that the “transition” to Industry 4.0 is beyond your organization’s goals or abilities, here’s some great news: You’re probably already on your journey.
Machinery gets worn down and consumed as it is utilized, and replacement parts and maintenance protocols serve as great examples of baby-steps into the 4.0 environment. You can track what was bought or repaired, how and when, and get smarter about it every day.
Based on what you learn, over time you’ll see opportunities to optimize and become better, more cost efficient and faster. The data is there for the taking, and as we observe and improve our actions, we support and further develop the 4.0 world. Start with applying this in a few areas and expand to other operations as your comfort level rises. The forces that move us forward are already present.
The savvy manufacturer also will recognize that technology can change faster than people do. Inventions rarely come with a set of instructions, let alone a training class and slide deck for everyone to learn from. Technology and training rarely arrive on the same day.
This offset in timing often manifests as frustration in the workforce and, ultimately, a gap between required workers and fully trained and available workers. This is why training always must be viewed as an ongoing process, rather than a milestone met and surpassed. We need to learn how to change, and get better at the art of changing. It never, ever ends. Technology encourages us to improve and add more value, to become a better version of ourselves.
Market Forces Push Technology Forward
Yet, despite all this potential, some manufacturers may continue to wonder if they really need 4.0. For you, here’s two words to keep front and center while looking at the long-term health of your manufacturing business: functional obsolescence.
Functional obsolescence means there is absolutely going to come a day when your machinery no longer performs at a level the market requires, and you can’t alter it enough to make it compliant. This applies to your processes too.
Like it or not, markets sometimes mandate that only the newer kind of organization has the capacity and ability to produce the widget in the “right” or “desirable” way. At that point, you’ve either joined the technology-enhanced ranks or you haven’t, and Request For Quotes and Purchase Orders (or the lack thereof) are notoriously uncaring and unforgiving. You either win the bid or you lose the bid.
Imagine a More Efficient Future
So, is Industry 4.0 scary? Nowhere near as much as the alternative! Nor is it something we should strive to avoid. Rather, it’s something to embrace, nurture and be a part of the wonder. We are privileged to be a part of it, and we owe it to ourselves.
Imagine all the time and money that can be saved when raw materials can be obtained and shipped to you in the most efficient manner. Imagine your plants can perfectly schedule shifts and specific workforce requirements, and downtime is drastically reduced. Imagine pallets full of inventory perfectly lined up at machines in the most logical order possible. Imagine never running out of cutting tools, abrasives, drills, filters and the like.
Imagine pallets full of sub-assemblies, relaying where they are and how well they were put together, all displayed on a screen in real time. Imagine your production lines telling you exactly how much they’ve produced and what maintenance they’ll require, so you can fix something before it breaks. Imagine a truckload of perfect parts shipping out to your customer, and you both know where they are and when they’ll arrive. This is what technology is for.
Better Data Enables Better Control
How far is it from here to there? How far do we have to go to say we’ve truly entered Industry 4.0? This isn’t the right question. The proper question is worded in terms of how much additional value is desired.
And the proper measurement of this value isn’t stated in traditional terms like speed, dollars, production amounts or similar types of data groups. Rather, the answer is stated in terms of control. Control is the tangible thing of value provided by Industry 4.0, and the data is what gets us there.
Working harder and faster has been our strategy for so long, but we’ve tapped that out. Measure value in terms of control, and keep improving your controls. You’ll like the result. Isn’t that what data is for?
Jon D. Devine is an Industry Principal and Sales Director for Infor. With more than 25 years of experience in manufacturing, sales, purchasing and program management, Jon offers his expertise to Infor prospects and customers in the United States and around the world.
Table of Contents
More ERP material...
Choosing a CRM System for Your Business
Data analytics holds the ability to highlight inefficient manufacturing processes and enable…
The Undeniable Benefits of Implementing ERP in Food and Beverage Manufacturing
Data analytics holds the ability to highlight inefficient manufacturing processes and enable…
Emerging Technologies in Manufacturing Driving Business Growth
Data analytics holds the ability to highlight inefficient manufacturing processes and enable…