As an independent ERP consulting firm, we are often asked to guide project teams from manufacturing and distribution firms looking to work through enterprise system selection, evaluation and implementation.
Many of our engagements involve teams considering both Product Lifecycle Management (PLM) and ERP systems
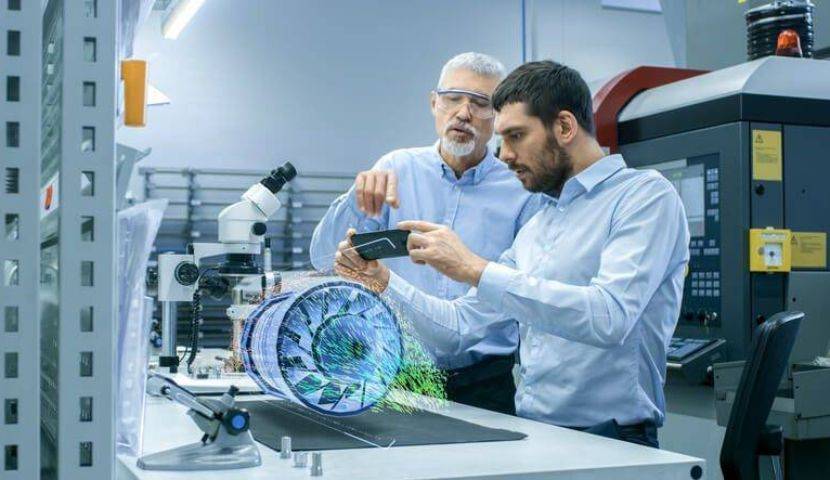
These companies typically grapple with their processes when PLM and ERP are not fully integrated. They risk mismanaging product changes and therefore creating mistakes in manufacturing or failing to correct product quality issues.
We reviewed these issues in a recent blog post entitled 3 Questions about PLM and ERP that shared how integrated PLM and ERP can improve productivity, drive a “single source of truth,” and reduce the time to develop new products.
This blog post shares recent PLM success “stories from the field” illustrating how the benefits of ERP and PLM cut across the enterprise.
PLM Success Story 1: Global Aerospace OEM
In the first PLM success story, Ultra was asked to conduct Business Process Mapping of current state and future state processes of the engineering and product development process for a global aerospace OEM.
It was clear the OEM understood that improving overall performance would entail improving business processes.
Ultra’s Business Process Improvement (BPI) services focused on understanding the company’s processes and business requirements and identifying areas of improvement based on best practices with a track record of reducing process waste.
The Ultra team conducted process workshops at the manufacturer’s engineering location in New Zealand and worked with senior executives and engineering team leaders.
As part of ERP process improvement services, Ultra also developed and presented education to the entire organization on PLM, and ERP topics. After these phases were complete, Ultra created requirements and implementation planning deliverables for PLM, ERP, configurators and lean business process Improvement.
Ultra’s engagement then turned to the evaluation and selection of five leading PLM vendors.
Ultra’s experience and leadership to hold everyone accountable to a future state focused implementation that delivers the expected ROI and enables business aspirations brought this project a successful implementation.
The company chose the most effective PLM system for their needs and achieved a faster time to value because of this thorough approach.
PLM Success Story 2: North American Electronics Manufacturer
We also had the chance to lead a project for an electronics manufacturer, once again involving process improvement methodologies along with ERP and PLM selection.
During the engagement, Ultra conducted a complete Business Process Mapping of current state and future state of engineering, product development, and manufacturing process.
As business improvement consultants, we conducted current state workshops at five factory locations and worked with executives and engineering team leaders.
In the business process review, we saw that seamless integration between PLM and ERP was a must. The company grappled with their processes when PLM and ERP were not fully integrated. They risked mismanaging product changes and therefore creating mistakes in manufacturing or failing to correct product quality issues.
Again, it was key that Ultra delivered client education on PLM, ERP, and lean product development topics. Our engagement also involved the creation of requirements and implementation planning deliverables for PLM, ERP, CPQ configurators and lean business process improvement.
After these methods, we drove the evaluation and selection of leading PLM vendors.
The company achieved value from implementing the best-fit ERP and PLM, and integrating the systems to achieve the desired future state.
PLM Success Story 3: North American Recreational Vehicle OEM
Complex and accelerated product development cycles demand that the enterprise undergo true business process transformation.
That’s what we saw at our engagement with a North American recreational vehicle OEM.
We guided the ERP project team through business process improvement and PLM selection.
We conducted Current State Workshops at their factory location and worked with team leaders throughout the process. Transforming the OEM’s business processes required creating a vision of the future state from their current state – and on to defining the business value for the project.
Done properly, this foundation established alignment of expectations with management, improved the efficiency of the team, eliminated process waste, and reduced the time to benefit for their project.
Ultra conducted a detailed analysis of the company’s Bill of Materials (BOM) management and Options and Variant BOM configuration process. We created detailed PLM requirements and implementation planning deliverables.
It was also critical that Ultra created a comprehensive multi-year, multi-phase business case and ROI model for the justification of the PLM project.
Learn More
Write your own PLM success story! See these resources.
- The role of an ERP consultant involves achieving success stories on behalf of our manufacturing and distribution clients. See additional success stories to learn more about the value Ultra delivers to our clients.
- There’s additional ERP education for deeper insight.
- Looking to achieve your own PLM success story? Contact Ultra for the best way to get started.
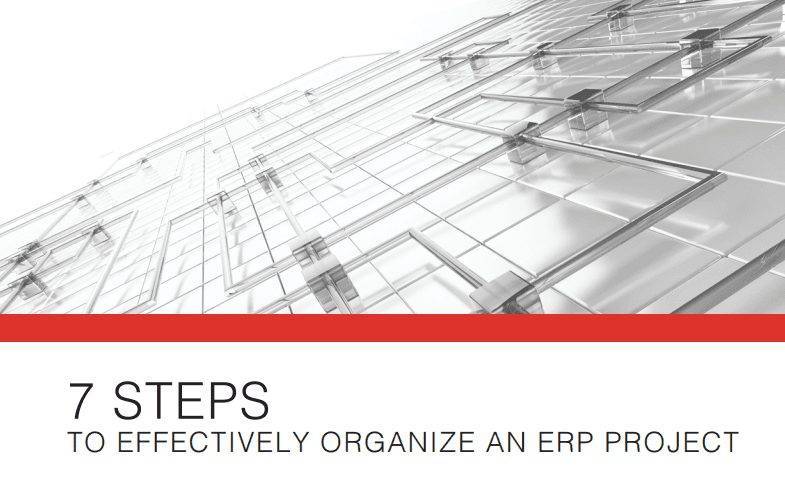
7 Steps To Effectively Organize An ERP Project
The 7 Steps to Effectively Organize an ERP Project is designed for ERP project teams from today’s forward-thinking manufacturing and distribution organizations. Read tried and true strategies for manufacturers to effectively manage an ERP selection project. See what it takes to be successful and more with this Download.
Table of Contents
More ERP material...
Choosing a CRM System for Your Business
Data analytics holds the ability to highlight inefficient manufacturing processes and enable…
The Undeniable Benefits of Implementing ERP in Food and Beverage Manufacturing
Data analytics holds the ability to highlight inefficient manufacturing processes and enable…
Emerging Technologies in Manufacturing Driving Business Growth
Data analytics holds the ability to highlight inefficient manufacturing processes and enable…