The industrial landscape continues to evolve and experience periods of significant growth. Once viewed as a luxury, the integration of automation and advanced technologies is now a necessity to align manufacturing enterprises with these rapid improvements. As manufacturers strive to remain competitive and efficient, the digital transformation of their operations becomes a key driver of success.
From optimizing workflows to streamlining initiatives and improving product quality, automation and technology are reshaping how manufacturing conglomerates conduct business. Join us as we explore the pivotal role of automation and technology integration in driving digital transformation in the manufacturing industry. We will highlight how these advancements not only optimize manufacturing processes, but also enable smarter decision-making, greater connectivity, and long-term growth.
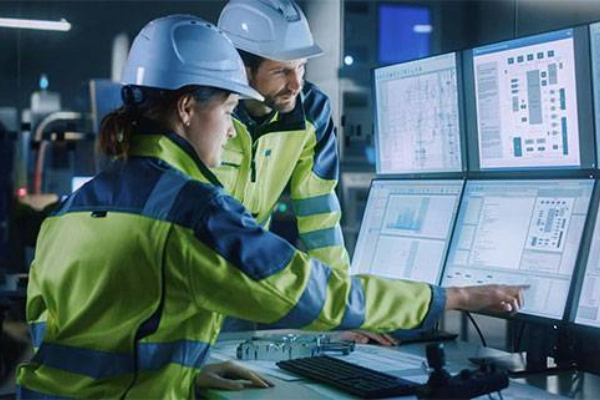
Solving Manufacturing Challenges with Smart Factory-Ready ERP Systems
Download the eBook to discover how ERP with smart factory integrated technology can help your organization overcome common manufacturing challenges.
What is Digital Transformation in Manufacturing?
Digital transformation in manufacturing refers to the adoption and implementation of digital technologies. The approach carries over into all aspects of manufacturing processes to enhance efficiency, productivity, and innovation. It involves using technologies such as Internet of Things (IoT), artificial intelligence (AI), big data analytics, automation, cloud computing, and advanced robotics to improve operations, reduce costs, and create new opportunities.
During a manufacturer’s digital transformation journey, they might utilize the following:
- Smart manufacturing factories: IoT sensors can monitor equipment in real time to improve predictive maintenance and minimize downtime.
- Robots: Machines can perform time-consuming, repetitive tasks, increasing production processes and accuracy.
- Data analytics: Collecting and analyzing data from various parts of the manufacturing process allows you to make informed decisions, predict trends, and achieve operational efficiency.
- Supply chain optimization: Digitally connecting different stages of the supply chain can improve communication, increase transparency, and reduce delays.
- Customization: Using digital design tools, 3D printing, or flexible manufacturing systems, providers can offer more personalized products.
In short, digital transformation drives competitiveness in a crowded industry by empowering manufacturers to enhance manufacturing operations, streamline time-consuming tasks, foster innovation, and improve the customer experience.
The Role of Automation in Manufacturing
Automation technologies play a critical role within the manufacturing sector by enabling smarter, more efficient, and scalable production processes. The following points demonstrate automation’s contributions to this transformation:
- Greater production: With automation, the need for manual intervention is significantly reduced, leading to increased production and less downtime. Automated machines, AI-powered systems, and robots can work continuously, ensuring manufacturing operations are optimized for maximum output.
- Improved quality control: Automated systems can perform manufacturing tasks with greater precision and consistency compared to manual labor, as well as detect and correct errors in real time. This helps produce more uniform products with fewer defects and improved overall quality.
- Cost reduction: By automating respective tasks, manufacturers not only minimize the risks of human error but also can reduce the costs associated with labor.
- Data-driven decision-making: Automated digital tools are often equipped with sensors that generate large amounts of real-time data. This data can be used to make informed decisions, predict maintenance needs, and optimize supply chains, helping to create a more agile and responsive manufacturing ecosystem.
- Workforce augmentation: Rather than replace workers, automation enhances their productivity by freeing them up to focus on more strategic, creative, or complex responsibilities where new technologies may fall short.
- Flexibility and customization: Automated technologies and systems can adapt to different production needs, enabling manufacturing companies to swiftly transition between product lines or produce customized items. This helps support greater diversity in production processes and faster time-to-market.
- Supply chain integration: Automation facilitates better integration of production lines with suppliers and distributors, improving communication and coordination.

The Impact of Manufacturing Digital Transformation
Digital transformation initiatives offer several benefits for manufacturing enterprises, such as:
Manufacturing Process Optimization
One of the most significant advantages of digital transformation in the manufacturing industry is the optimization of critical processes. With advanced analytics and machine learning algorithms, manufacturers are capable of continuously improving their processes based on performance data. These algorithms can recommend adjustments to enhance productivity, minimize waste, and make production schedules more efficient.
Predictive Quality Management
Customers rely on manufacturers to deliver products as expected. When they fail to meet expectations, providers face numerous consequences, which is why quality management is a top priority. Data collected from connected devices and sensors can predict the likelihood of quality issues before they happen. This predictive approach allows manufacturers to make preemptive corrections and adjustments to avoid defects, reducing the cost of rework, returns, and customer dissatisfaction.
Supply Chain Resilience
In many cases, manufacturing enterprises are at the mercy of supply chains, often impacted by the ripple effect of disruptions. Digital transformation improves the resilience of supply chains in the event of raw material shortages, natural disasters, or political instability. By machine learning algorithms suggesting alternative solutions based on real-time circumstances, manufacturers can pivot quickly to minimize the impact they feel. Additionally, digital transformation can help improve supply chain management by predicting potential complications before they occur.
Enhanced Collaboration
Integrating various digital transformation systems enables different teams and departments within an organization, as well as external partners, to collaborate seamlessly. Project timelines, production plans, inventory data, and quality control information can be shared with suppliers, customers, and distributors to ensure all parties are on the same page. Moreover, the flow of information enables managers to quickly make crucial business decisions based on accurate, up-to-date information and respond faster to operational challenges.
Ready to start your digital transformation journey?
Click the button below to request your free discovery call.
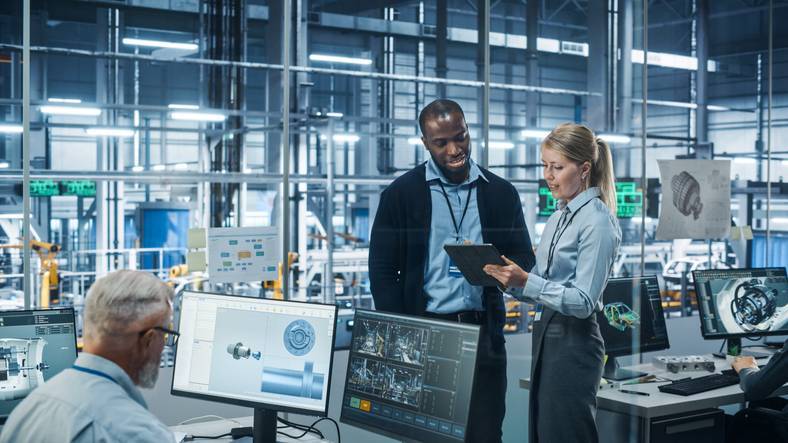
Faster Product Development
Research and development are crucial processes that influence overall manufacturing operations. Traditional methods of R&D can be time-consuming and exhaust critical resources. Digital tools like computer-aided design (CAD), simulation software, and 3D printing technology enable rapid prototyping, allowing manufacturers to design and test new products much faster. Speeding up the research and development process can aid in bringing innovative products to market quicker than ever before.
Sustainability and Environmental Impact
With digital systems in place, manufacturers can ensure the right amount of materials are being used at the right time, thus improving supply chain management, resource planning, and energy consumption. Furthermore, the data collected from industrial Internet of Things devices can help providers identify areas for improvement in sustainability, such as optimizing transportation routes to reduce emissions.
Improved Customer Satisfaction
In addition to minimizing product defects and ensuring products arrive in the customer’s hands as expected, real-time data on inventory, shipping, and product availability enables manufacturers to provide more accurate delivery estimates for greater customer satisfaction. Additionally, this information can be used to quickly respond to customer inquiries, further improving the overall customer experience.
Performance Benchmarking
With large datasets generated by production machines at your disposal, you can anticipate potential issues, trends, and distributions to avoid costly stoppages. Manufacturers can also compare performance across various aspects of manufacturing, including production lines, factories, or shifts. This helps them identify bottlenecks, inefficiencies, or under-performing assets. This advantage ensures the continuous improvement of manufacturing efforts, which can lead to long-term gains.
Potential Obstacles Standing in the Way
While transforming into a digital manufacturing environment through automation can provide immense benefits, it also produces challenges. Some of the potential obstacles include:
Resistance to Change
A common challenge to digital transformation is getting everyone on board with the concept. Employees, particularly those who have been in their positions for long periods, may have developed strong attachments to the existing operation. They might view the change as a threat to their job security.
Successfully leading employees through any transition requires clear communication, training, and reassurance, starting with management. Those in leadership positions should work hard to create a culture of continuous learning and flexibility. They should also help employees understand the long-term benefits of digital transformation, such as new career opportunities.
Data Management and Security
Digital transformation involves analyzing and utilizing vast qualities of data generated from connected devices. For manufacturers who don’t have the necessary tools or processes in place, managing this data presents a challenge.
In addition, as manufacturing operations become more intertwined with digital tools, vulnerabilities to cyberattacks increase, including ransomware, data breaches, and industrial espionage. To mitigate these risks, manufacturers must invest in robust cybersecurity systems that protect their intellectual property and sensitive stored data.
Skills Gap
The shift to digital manufacturing requires employees to not only buy into the concept but also possess specialized skills in key areas, such as data analytics, AI, robotics, cybersecurity, and cloud computing. Manufacturers must invest in ongoing training to upskill their existing workforce. Furthermore, manufacturers may face challenges attracting and retaining skilled workers, as there continues to be a global shortage of workers with these competencies.
To attract top talent and compete with not just competitors, but other industries as well, providers should develop compelling hiring offers that include competitive salaries, comprehensive benefits, and opportunities for career growth.
Legacy Systems Integration
Manufacturing enterprises operating with deeply embedded legacy systems, such as inventory management, production scheduling, and supply chain monitoring, may face challenges when integrating new digital technologies.
To bridge the gap between old and new technologies, manufacturers can implement incremental upgrades, meaning they upgrade legacy systems in stages. This method helps to minimize operational disruptions and spreads financial costs over time, making the transition more manageable. Additionally, manufacturers can invest in custom software solutions that integrate more seamlessly with existing legacy systems, facilitating a smoother transition to digital operations.
Regulatory Compliance
As digital transformation in manufacturing becomes more prevalent and operations become more reliant on data, regulators are creating new standards that must be complied with. Because these standards are continuously evolving with the industry, manufacturers may be met with significant challenges, which can complicate the adoption and integration of digital technologies.
Effectively navigating the complexities of stringent regulations and standards requires staying informed on the latest changes. Additionally, having a proactive approach that takes compliance into consideration from the onset eliminates the need for adjustments thereafter.
"Companies need to look beyond their immediate requirements and consider how the application of new technologies will help them build long-term competitive advantage."
Joe Bush | The Manufacturer
Developing a Strategic Plan for Digital Transformation Manufacturing
Successful digital transformation requires understanding best practices and strategic planning that involves the following steps:
Assess Current State
Manufacturers should begin by reviewing their existing technological infrastructure to identify gaps and areas that could be improved upon. Take a look at current processes as well to expose the areas where new technologies can improve productivity. Involving employees, managers, and department heads can provide valuable insights into pain points and opportunities for improvement.
Define Clear Objectives
Create a vision for digital transformation initiatives, ensuring they align with the company’s overall business strategy. Define clear and specific goals to measure success throughout the digital transformation journey.
Invest in Talent and Skills Development
To get existing workforces up to speed and ensure they are proficient with new technologies, manufacturers must provide effective training programs. Additionally, fostering a culture of change helps to make the transition more seamless and less daunting for workers. Do this by promoting digital literacy and encouraging employees to be open to new ways of thinking.
Integrate with Existing Systems
To avoid disruptions, ensure new technologies integrate as expected with existing legacy systems. Be strategic when selecting systems to connect with various devices, platforms, and software.
Implement Data Governance and Cybersecurity
Be ready to handle massive volumes of data generated by digital systems to ensure quality, security, and accessibility. Make sure you have implemented robust security measures to address the risks associated with digital connectivity.
Measure and Adjust
Regularly track the performance of digital transformation initiatives and established goals. Key performance indicators (KPIs), such as production efficiency, machine downtime, and product quality, can be leveraged to evolve strategies and refine tactics.
Digital Transformation in Manufacturing with Ultra Consultants
Those who embrace automation in the manufacturing industry can open the door to fundamental change, which can have massive impacts throughout an organization.
As an independent consulting firm serving the manufacturing and distribution industries in North America, Ultra Consultants aims to be your go-to when it comes to automation and digital transformation. Utilizing our exceptional enterprise software expertise, deep industry experience, today’s best practices, and rigorous, proven methodology, we can help your manufacturing enterprise experience game-changing, bottom-line results through optimizing your people, processes and technology..
For those interested in consulting services to learn more about how to make the transition to digital environments, request a free discovery call today.
Table of Contents
More ERP material...
What Is Enterprise Data Management?
From customer insights to supply chain metrics, organizations depend on accurate, timely,…
Top 10 Uses of AI in Food Manufacturing: Enhancing Safety, Quality, and Efficiency
In the face of changing consumer demands and complex supply chains, food…
AI’s Role in Digital Transformation
Digital transformation is about more than just adopting new technologies—it’s about reimagining…