According to the latest Warehouse Vision Study from Zebra, 80% of organizations are planning to invest in new technologies to be competitive. This result stems from increasing challenges faced by warehouses and distribution centers in delivering on demands for faster delivery, on-demand fulfillment, and an ongoing worker shortage.
The study continues, “over the next five years, decision makers will upgrade or add additional modules to their existing WMS or migrate altogether to full-featured, best-of-breed systems. These systems will enhance the mobile-user experience and allow for new inputs that enable data-driven performance.”
How do you know if your current warehouse management system (WMS) will see you through these challenges or if you need to make the investment in something new? Here are 5 signs you need a new WMS.
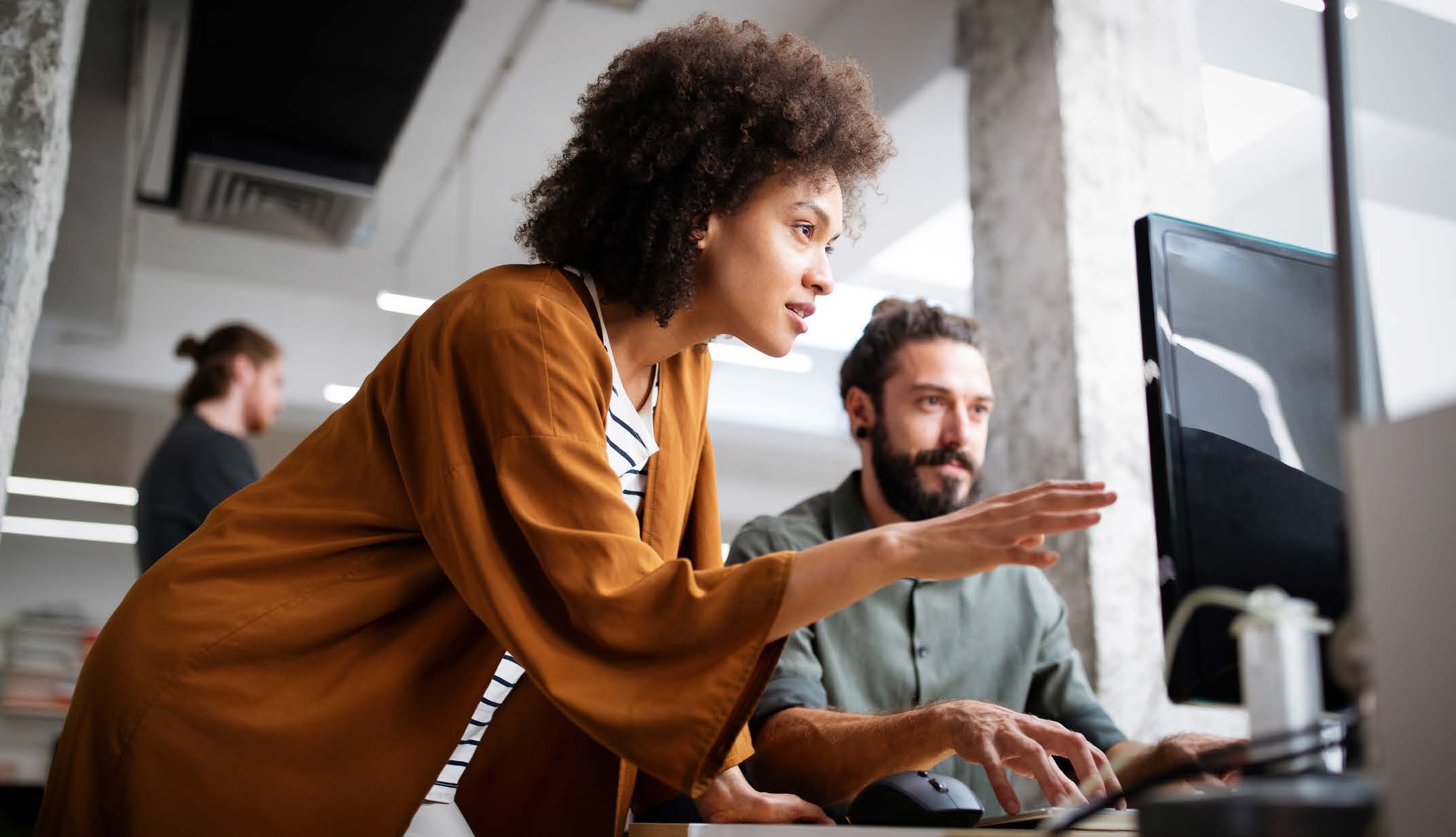
How to Choose a WMS
This ebook walks you through everything you need to know about WMS, including the criteria for selecting a best-fit system and the challenges you might face when implementing it.
1. You’re creating workarounds
Are you finding that you want the ability to manage more processes in your warehouse? These can include such functions as kitting, labor tracking, or custom label printing. Tracking and ensuring that your data is accurate will get more difficult the more processes that call for additional customization or workarounds. Plus, your continuous improvement efforts shouldn’t be hindered by an outdated WMS.
Keep in mind that as your current system ages, these workarounds require custom coding—which doesn’t carry forward with standard updates. As more and more coding is added, it reaches a point where even minor changes are a major hassle, effectively hampering future modifications.
2. You’re growing; your WMS is not
If your business experiences a period of rapid growth, your outdated WMS could cause you to be overwhelmed by an influx of new orders or fulfillment issues. What if you want to add a new warehouse? Will you be able to track inventory in multiple locations?
These are just a few of the issues that could arise with your current WMS that may make your growth opportunity hard to sustain. A WMS must be adjustable and adaptable in order to support your evolving business while allowing the processes that give you an edge over the competition.
3. Your vendor isn’t supportive
In some cases, the original software vendor no longer offers support for outdated systems. If your WMS has reached end-of-life (EOL) the vendor will no longer offer updates or patches, or even end technical support services for the system. This leaves your company exposed to potential cybersecurity issues, without a means to make critical changes to improve your business processes, or left hanging when an issue arises.
Also, if your system was developed in-house, you’re susceptible to the tribal knowledge of a few key people (or maybe one person!) to maintain or update the software. If a key person leaves your company, they take that knowledge with them.
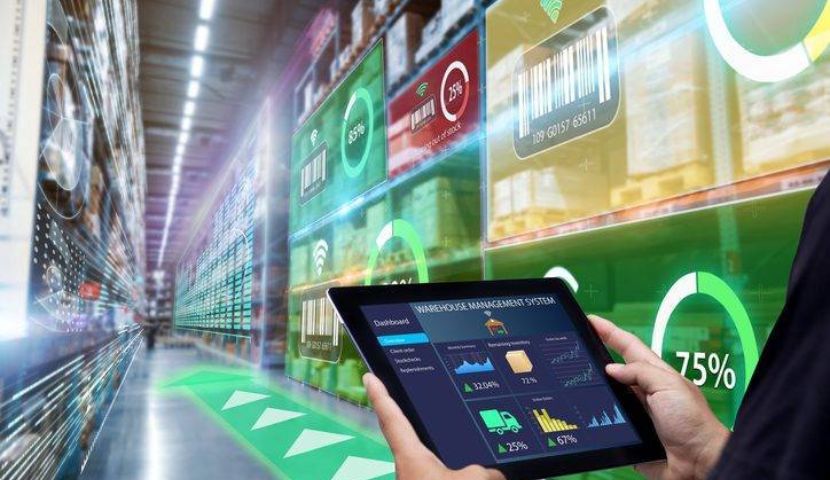
4. Your WMS is all alone
An effective WMS should be able to impart data to inform decision making across your business. One problem with a static WMS is that it can result in siloed data, making it difficult to get an accurate view of how warehouse management data relates to other areas of your business such as accounting, customer service or sales. Your siloed system could be standing in the way of opportunities to cut costs, reduce errors and achieve greater efficiency.
The key to eliminating data silos is integration—whether through a shiny new ERP system with built-in WMS functionality or a separate WMS that integrates into your ERP and other business systems. The end goal is access to a single source of truth for your company.
5. Your WMS is stuck in the past
A WMS with an outdated interface (green screen anyone?) can be hard for workers to understand and use. This makes it difficult for new employees to learn, increases user errors and bogs down productivity. In turn, older, outdated technology could make it more difficult to attract younger workers, looking for environments with intuitive and user-friendly technologies.
Also, to keep your aging WMS working, you may have to continue running older equipment and legacy operating systems, which translates to lost productivity. This also can require sourcing third party vendors for support, and personnel who have specific technical skills to operate older systems.
Conclusion
The bottom line is that replacing your WMS comes down to deciding when the benefits of a new system justify the investment. Fortunately, the technology experts at Ultra Consultants can help determine what value you’d see from your technology project BEFORE you invest.
Ultra’s distribution and warehousing consultants have decades of experience bringing bottom line results to companies just like yours. Reach out today to put their expertise to work for you.
Table of Contents
More ERP material...
AI’s Role in Digital Transformation
Data analytics holds the ability to highlight inefficient manufacturing processes and enable…
Master Data Management (MDM) Strategy: A Guide to Getting It Right
Companies currently generate vast amounts of data from their systems. But while…
Is Your HCM Platform Future-Ready? 6 Signs It’s Time for a Change
The work world is changing face and HR teams are under pressure…