Business Process Improvement Project Pays Off for Manufacturer: A Story from the Field
Ultra’s independent ERP consultant team recently partnered with a manufacturing company for a business process improvement project during an ERP evaluation and selection engagement. This is their business process improvement success story.
The US-based valve manufacturer designs and manufactures fluid control valves and components for leading OEMs in aerospace, defense, nuclear and power, land and sea and other key vertical markets. The company operates out of a state-of-the-art production and test facility.
The company partnered with Ultra for a business process improvement project, as well as ERP selection and evaluation.
Business Process Improvement Project in Action
The business process improvement project got underway by taking the time to document the company’s processes through current state mapping. The business process review involved key business users, department management and production personnel, with Ultra providing independent guidance.
When we conducted the business process analysis, we looked at several parts of the “as-is” business including production and operations. We asked key questions such as if the current business processes added value to the business if there was a waste in any of the processes, and if there were redundancies in the processes and data versus more streamlined, automated processes.
Challenges with Daily Production Dispatch List
According to Operational leaders at the company, an “as is” process that was identified as particularly problematic was the daily production meetings and the creation, use and tracking of the dispatch list.
The firm’s dispatch list sets the production prioritization schedule for each work center. It lists orders in the exact sequence they should be produced, based on due date or other considerations.
In previous years, it was a manual and error-prone process to assemble the detailed listing of all the orders to be produced based on priority.
Because of the manual processing and inefficient handling of the daily dispatch list, the production team was forced to sit through more than 20 hours per week of meetings and manual review. More than 8 people gathered each morning for the daily production meeting for over an hour and met again at the end of the day to look at the dispatch list and prioritize the items.
Accuracy was also a concern. Data in the dispatch list did not reflect current production metrics and was constantly being reviewed and modified by supervisors from each work center, Operations Director, planners, product line leads, schedulers and other key production personnel.
Noted the Operations Manager, “This dispatch list is crucial as it basically translates our production plan into action. The company thinks of this list as the “heartbeat of production. Since the list is required to assign jobs to each work center, it was a huge issue that we didn’t trust the data on the dispatch list.”
The twice-per-day meetings were spent looking at whiteboards of hand-generated production lists which were outdated and didn’t accurately reflect real-time production. In fact, the data would be out of date by the time the meeting ended, since parts were constantly moving through work centers.
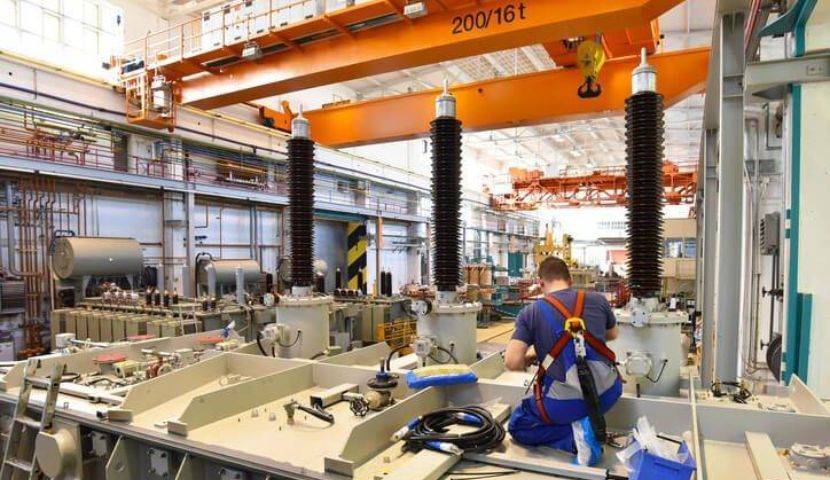
Business Process Mapping
Ultra led the business process improvement project to uncover the wasted effort and inaccuracies with the dispatch list during “Current State” mapping.
The mapping exercise revealed the root cause of the problem as lack of data standards within the legacy systems. Ultra worked with the company to set production data standards within the existing solution and automate production data tracking. The improvements were put into place without adding any additional technology.
Now, the reports are no longer hand-generated. Instead, they are automatically pulled as needed with real-time data. The company cut the need for the twice-daily meetings and has confidence they can accurately track production information the team must know before they start on work orders.
It’s important to note Ultra conducted this business process mapping phase of the business process improvement project to uncover any problems or issues with the processes well before the process of ERP implementation began.
Production reports are now automatically pulled as needed with real-time data. The company cut the need for 20 hours of meetings each week.
Lessons Learned
The valve manufacturer experienced several “lessons learned” from this business process improvement project.
- Improved processes before technology: Primarily, the company sees the value of putting the focus on business process improvement and not solely technology.
- Reduction in clerical effort, meetings and manual handling: The improved processes cut clerical effort and reduced the time spent in meetings – cutting out nearly 20 hours of meetings once needed a week.
- Improved production scheduling accuracy: By establishing data standards and reducing duplicate data entry and manual efforts, the company sees improvements in accuracy.
While the company is still moving through ERP implementation, this business process improvement project is example of the benefit of improving processes before adding new information systems.
Finally, the manufacturer sees the benefit in having the business improvement project led with change management methods, so the users could understand why the new processes were important and the ultimate value to the business.
Noted the company’s Operations Manager, “This dispatch list project uncovered a lot of issues and problems with tracking production schedules. Having Ultra’s “fresh set of eyes” helped our team understand the importance of this change, and the value that would be achieved once the new processes were put in place.”
7 Steps to Effectively Organize an ERP Project
The 7 Steps to Effectively Organize an ERP Project is designed for ERP project teams from today’s forward-thinking manufacturing and distribution organizations.
Read tried and true strategies for manufacturers to effectively manage an ERP selection project. See what it takes to be successful and more with this Download.
Table of Contents
More ERP material...
Selecting the Right TMS System: Key TMS Features and Trends to Consider
Data analytics holds the ability to highlight inefficient manufacturing processes and enable…
Choosing a CRM System for Your Business
Data analytics holds the ability to highlight inefficient manufacturing processes and enable…
The Undeniable Benefits of Implementing ERP in Food and Beverage Manufacturing
Data analytics holds the ability to highlight inefficient manufacturing processes and enable…