As we move farther into 2025, industrial equipment manufacturing (IEM) continues to evolve through innovative technologies. Building on the digital transformation that began decades ago, manufacturers are currently looking to implement smarter, more efficient and sustainable practices. Last year, we outlined the IEM Trends for 2024. Now, we explore the key Industrial Manufacturing trends that are shaping the industry in 2025, helping businesses stay competitive as the market changes.
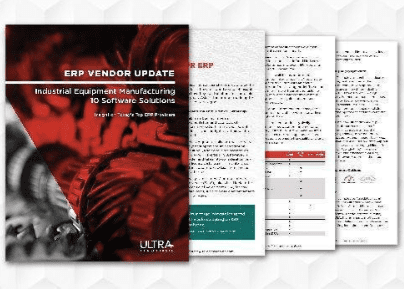
ERP Vendor Update: Industrial Equipment Manufacturing
Download this guide to get a close-up look at 10 of today’s top IEM software solutions.
Industrial Manufacturing Industry Trends
1. The Rise of Smart Factories: AI and IoT Integration
Smart factories are no longer just a concept for the future. As a reality in 2025, manufacturers are moving to adopt AI-driven automation and integrating the Internet of Things (IoT) into their production environments. Smart manufacturing allows for real-time monitoring, predictive data analytics and better quality control. Ultimately, these advancements lead to efficiency improvements and reduction in downtime.
As AI becomes more sophisticated, the technology is more adept at helping manufacturers anticipate and address issues before they happen. Manufacturers can collect large amounts of data through sensors and devices embedded throughout the factory, leading to more informed decision-making and faster problem solving. As the remainder of 2025 unfolds, expect to see even more seamless integration between AI, IoT, and operations systems.
2. Predictive Maintenance: Leveraging AI and Edge Computing
As it was in 2024, predictive maintenance continues to be a game-changer for IEM this year as well. AI and machine learning enable manufacturers to predict equipment failures before they happen and extend the life of equipment. But new this year is the rise of edge computing.
Edge computing allows data to be processed locally, closer to the equipment, reducing the latency of predictive maintenance systems. By processing data at the “edge”, manufacturers can take action quickly, without having to wait for data to travel to a centralized cloud server. This results in faster response times, improved uptime, and a more proactive approach to managing equipment.
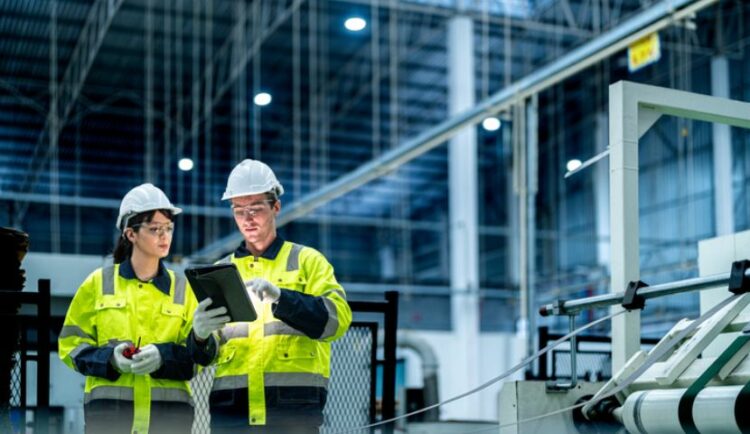
3. Supply Chain Resilience: Digital Transformation and Blockchain
2025 is also bringing a renewed focus on supply chains. Following the disruptions following the pandemic and now with uncertainty around upcoming economic tariffs, manufacturers are focusing on building more resilient and agile supply chains. One of the advancements in this area is blockchain technology (BT).
Blockchain provides a secure, transparent method of tracking products throughout the supply chain. Manufacturers can utilize BT to ensure the authenticity and quality of materials and products, enabling better visibility to potential disruptions while preventing fraud and unauthorized activity.
In addition, companies are embracing advanced data analytics and real-time tracking to quickly respond to supply chain challenges. This increased visibility helps avoid bottlenecks, reduce costs and improve delivery times.
4. Automation and Labor Shortages: Reskilling and Collaboration with AI
As labor shortages continue to challenge IEM, automation and AI are helping manufacturers find solutions. Robotics and autonomous systems can be used for repetitive tasks, freeing up workers to focus on more complex and value-added activities.
In addition to technology investments to address the labor shortage, there’s also a focus on reskilling and upskilling the workforce, helping employees work alongside AI systems and robots. This collaboration lets companies increase productivity without the need for large-scale hiring.
Ready to start your digital transformation journey?
Click the button below to request your free discovery call.
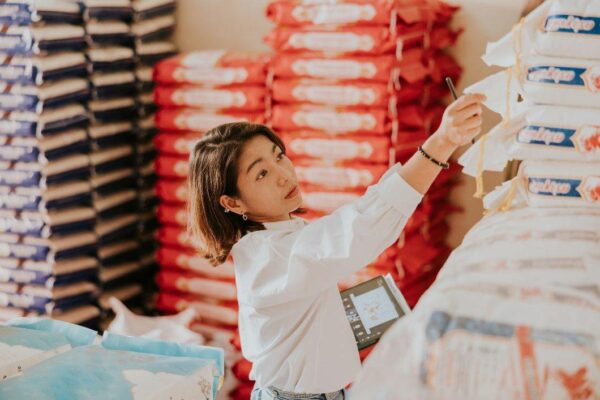
5. Sustainability: Embracing Green Technologies and Carbon Neutral Goals
Finally, in 2025 sustainability is moving to the forefront with advanced in energy efficient machinery, sustainable manufacturing processes and the use of renewable energy sources. Another buzzword is circular economy principles where products and materials are reused or recycled minimizing waste and reducing consumption. The integration of renewable energy sources, such as solar and wind power, is also on the rise in manufacturing facilities, helping businesses reduce their reliance on traditional energy sources. These changes are, in-part, the result of increasing government regulations around sustainability.
Conclusion: Industrial Manufacturing Trends: Embrace the Future
With 2025 well underway, the industrial equipment manufacturing industry is witnessing several advancements in technology. From AI-enabled software, smart factories and predictive maintenance to resilient supply chains and sustainability initiatives, IEM is evolving quickly.
Manufacturers who embrace these trends and invest in technology and process optimization will be better equipped to stay competitive, improve efficiency, and reduce costs. The experts with Ultra Consultants can help you stay ahead of the curve by ensuring your business is ready for the future of industrial equipment manufacturing. Get started today with your free no-obligation discovery call.
Table of Contents
More ERP material...
What Is Enterprise Data Management?
From customer insights to supply chain metrics, organizations depend on accurate, timely,…
Top 10 Uses of AI in Food Manufacturing: Enhancing Safety, Quality, and Efficiency
In the face of changing consumer demands and complex supply chains, food…
AI’s Role in Digital Transformation
Digital transformation is about more than just adopting new technologies—it’s about reimagining…