The Ultra ERP Blog keeps pace with enterprise software market activity – especially as it relates to ERP selection and enterprise software implementation.
This guest post looks at ways manufacturers are using ERP to complement their lean production methods.
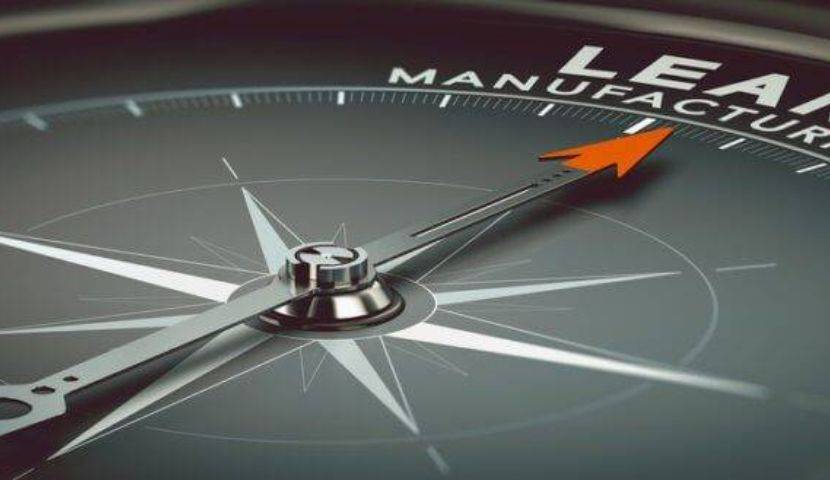
Lean manufacturing is a philosophy where a business intends to eliminate or minimize waste in any form. Who would ever say they want waste?
Taiichi Ohno originally defined seven forms of waste. They are defects, over-processing, transportation, motion, waiting, inventory, and overproduction.
Many lean practices have been developed to help a business become lean. Some of these include Kanbans, single minute exchange of dies, visible manufacturing, quality built-in, Gemba walks, value stream mapping, Poka-yoke, and pull scheduling.
When MRP and ERP were first developed, a common goal was to absorb manufacturing costs into inventory. The experts then taught us to use those systems with that goal in mind. Times and best practices have changed and ERP systems along with those best practices. Today, nearly any ERP for manufacturing will help a business practice lean manufacturing. Let’s look at a couple of examples.
Kanban
A Kanban is merely a signal to begin production that often means creating a shop work order. In the ERP configuration, there are controls. They might be set to start production for a certain item in a quantity needed to bring finished goods to a predetermined reorder quantity. The job could also be equal to the quantity required to ship today when there is no finished goods inventory. The transactions issuing component material and charging production labor work the same as any other production job in a push system, but the use of the Kanban turns the process into a pull system where production is directly driven by actual customer demand.
Quality built-in
This too is easily done with today’s ERP systems. Years ago, a manufacturer would produce a large lot of a product and then inspect the lot for defects. A manufacturer today will add an operation at the start of each process where the employee will check the previous operation for defects. That worker will then perform their assigned operation. The final step at any process will be a self-inspection of the work just completed.
A welder might begin with two pieces of cut metal. First, they perform a visual check on the quality of the cuts and take measurements of the length and angles of the cuts. Now they weld those two pieces together. Their final work is to measure the angle of the welded joint and inspect the depth of the weld.
Statistically, they can prevent all but 1 in 1,000 defects. When the subsequent worker checks the welds again, that person has another 1 in 1,000 chance of allowing a defect. Combined these two inspections yield only 1 in 1,000,000 chance of a defect being passed along. The instructions to perform the measurements and the actual measured values are kept in the ERP as normal transactions and available later for analysis.
Visible manufacturing
Visible manufacturing means that anyone walking near a worker can easily and quickly tell what the work is and how well the worker is performing that work
People working in such a visible, exposed theater will want to do their best. One simple way to effect visible manufacturing is to place a computer monitor near a workstation where passersby can see the ERP job description and the current operation from the aisle. The expected production rate, as well as an actual rate net of defects, shows off how well production is running. Manufacturers can also place visible labels marking danger such as sharp edges or caution such as a point where there could be electrical sparks.
Manufacturers who choose to use lean production methods and avoid waste can set up their ERP and the way they use ERP to complement their lean manufacturing.
Tom Miller is a columnist for ERP Focus, and has completed implementations of Epicor, SAP, QAD, and Micro MRP. He works as a logistics and supply chain manager and he always looks for processes to improve.
6 Software Selection & Implementation Pain Points + Solutions
Software selection and implementation processes often present challenges of their own. To steer you around trouble and help you drive success, Ultra’s experts compiled a list of pain points and solutions to be aware of as you embark on this journey.
Table of Contents
More ERP material...
Selecting the Right TMS System: Key TMS Features and Trends to Consider
Data analytics holds the ability to highlight inefficient manufacturing processes and enable…
Choosing a CRM System for Your Business
Data analytics holds the ability to highlight inefficient manufacturing processes and enable…
The Undeniable Benefits of Implementing ERP in Food and Beverage Manufacturing
Data analytics holds the ability to highlight inefficient manufacturing processes and enable…