Why ERP Implementations Fail
Enterprise resource planning software links most of today’s business management systems, and thus ERP software implementation is a necessary part of today’s digital transformation for manufacturing and distribution companies. To remain competitive and relevant in a fast-paced, globally competitive economy, senior executives know that an ERP system implementation with new technologies is unavoidable.
However, many organizations are hesitant to begin such an ambitious project to replace legacy systems and get a new ERP system. Most companies cite these primary reasons why they are wary of ERP technology solutions:
- Budget overruns/resources needed
- Staffing limitations / missing expertise
- Fears of a failed ERP implementation (the psychological factor)
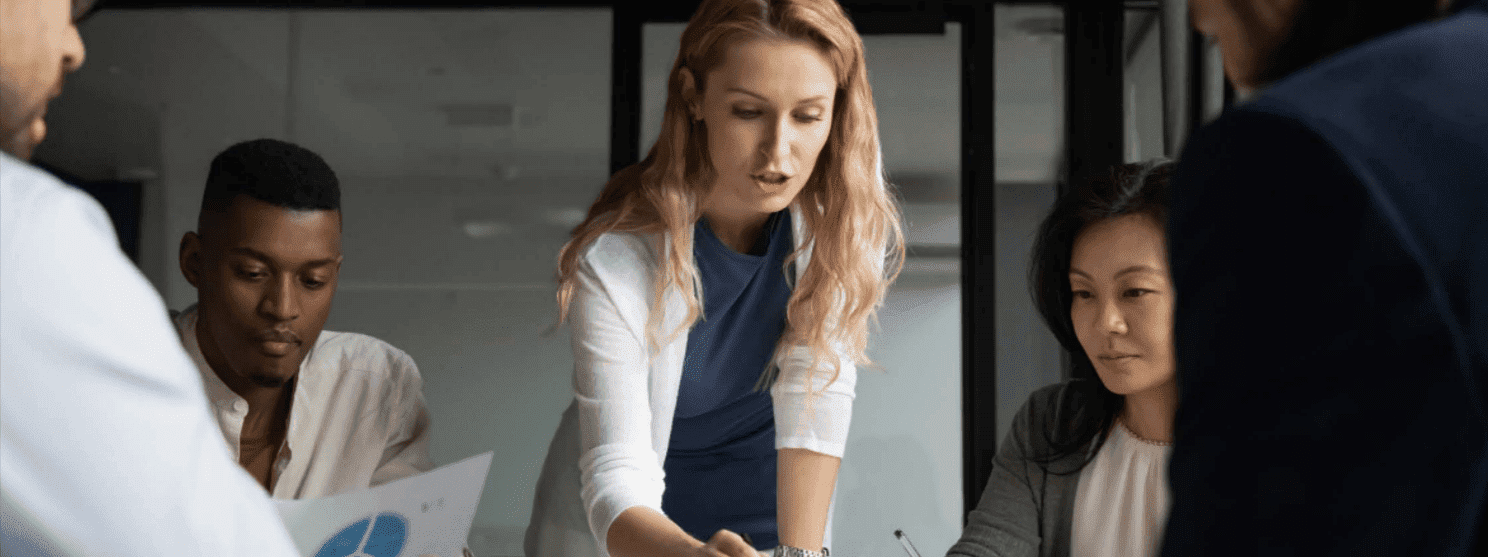
Best Practices for an Effective ERP Implementation
This paper provides actionable insights to make your ERP implementation a journey of success.
How Many ERP Implementations Fail?
Don’t let implementation companies scare you with stories of failed ERP implementation. We commissioned a leading ERP research firm to do a survey of 315 companies that had recently undergone an ERP system implementation. Here’s what we found:
- 67% Successful/Very Successful
- 31% Partially Successful
- 2% Not Very Successful
- 3% ERP Failure
For more on this landmark study, download the full 14-page report.
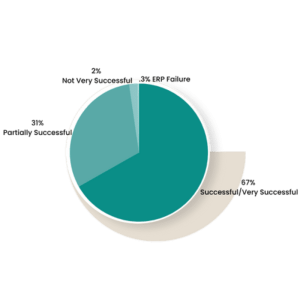
Reasons for ERP Implementation Failure
So why are there ERP implementation failures? Here are the main reasons why ERP implementation fails:
1. The Project is Not the Top Priority
When replacing the legacy system with a new ERP system and it is not the clear number one priority for your organization, the project is likely doomed to become an ERP failure. When users perceive the project as something that is not important, users and managers alike do not buy in and will not invest the time and resources necessary for success.
"The biggest reason ERP implementations fail is because companies don't have a clear understanding of their business needs and how the software can meet them."
Forbes
Putting all efforts into an ERP system implementation can result in unrealistic expectations and does not automatically result in a successful completion. Therefore, to avoid ERP implementation failure due to this reason:
- Your company must secure adequate funding or properly allocate resources for the project costs and demonstrate that the project is a top priority
- Employees need to be aware of the impact of the project and how it affects the future of the company
- Employees must invest their time and effort into understanding the system requirements and how the system will produce beneficial results for your organization
2. The Project is Viewed as an IT Project
Viewing an ERP project as an IT project often leads to ERP project failure as it fails to take into account the wider business implications and the need for engagement from all areas of your organization. The IT department may lead the project and handle the existing data, but ERP implementation requires collaboration across departments, disparate systems and functional areas.
Additionally, a technology-focused approach overlooks the need for organizational change management, which is critical to driving user adoption and achieving desired business outcomes. Without seeing the project as a business transformation initiative, teams may underestimate the resources and effort required to achieve success, leading to ERP failures.
"The biggest mistake companies make when implementing ERP is viewing it as an IT project. ERP is a business transformation, and it needs to be led by the business. That means having a clear vision for what you want to achieve with ERP and getting buy-in from all stakeholders from the start."
Forbes
3. Inadequate Internal Support
Too often, organizations focus only on C-suite sign-off. Often, employees may not be fully committed to the implementation process and may lack the necessary training and resources to effectively use the new system.
Additionally, internal resistance from employees may cause delays and misunderstandings that lead to costly mistakes and botched ERP implementation. This lack of support produces a negative impact on employee morale and increases the risk of errors during the transition period, contributing to ERP failures.
4. The Project is Rushed
Due to tight deadlines and pressures from stakeholders, your company may try to expedite a complex ERP implementation project without proper planning or preparation. Rushed projects result in insufficient testing, inadequate training and incomplete data migration, all of which leads to system failures and disruptions in business operations.
5. Not Assessing the Current State
The failure to assess the current state occurs when your business doesn’t identify existing systems, processes and data to assist in developing an efficient and effective new system. Moreover, it corresponds with the inability to analyze factors like supply chain constraints, specific organizational needs and user requirements. Assessing the current state, including employee testing and data cleansing, involves gathering key performance metrics and evaluating the suitability of existing systems.
The failure to assess the current state leads to a lack of proper design and planning, compromising the project from the start. As a result, without appropriate analysis of the present state, implementation plans may not be effectively executed. This lack of planning also results in low consistency in incorporation areas such as procedures, roles and responsibilities, leading to further complications and cost overruns.
6. Insufficient Research and Education
Your company may underestimate the amount of time, resources and education required to install and use current systems effectively. Without conducting thorough research on potential ERP vendors and ERP systems partners and failing to understand the entire process, your company may end up with ERP software that does not meet your needs.
Education is vital for all stakeholders involved in system implementation because:
- Lack of understanding could lead to user errors, compromising the system’s integrity
- Insufficient training may cause employees to not be prepared to handle the new system, resulting in increased human error, dissatisfaction, lack of use and resistance to change
7. Less-Than-Thorough Requirements Gathering & Definition
If the requirements gathering process is not done thoroughly or at all, then the implementation process of new ERP solutions will not accurately reflect your organization’s needs. This could lead to delays, increased realistic budget costs and ultimately derail the entire project.
Additionally, incomplete requirements cause confusion and misunderstandings among different teams working on the same project, jeopardizing the testing phases and ongoing support needed for successful implementation.
“Many businesses select the ERP then try and make it fit their business. What they should do is understand their business and map that to the available ERPs to find the one that best fits their business model with the least amount of customization.”
Forbes
8. Incorrect, Incomplete or Inaccurate Requirements
Inaccurate or incomplete requirements can arise from rushed requirements gathering or neglecting to involve key stakeholders. The result is a poorly defined scope, inadequate resources and an ERP software that does not meet the needs of your business. These are all ingredients for ERP failure.
When requirements are not clearly defined, it can lead to:
- User frustration and resistance to change
- Difficulty gaining traction for the system in the organization
- Software customization challenges, which can be costly and time-consuming
9. Excluding Critical Users and Managers From The Process
The absence of key stakeholders in the implementation plan jeopardizes the success of the project and increases the overall failed ERP implementation cost.
Excluding critical users and managers from the process leads to:
- Inadequate knowledge transfer
- Lack of ownership
- Incomplete requirements
- Unrealistic project expectations
- Resistance to change.
10. Flawed Software Selection
Experts say that 40% of companies regret their software purchase because it doesn’t align with business processes or can’t scale to meet their needs.
You may choose software that does not meet your company’s specific needs, resulting in the system being difficult to use and not delivering the expected benefits. The software may also lack important features or have compatibility issues with other systems used by your company.
The following factors contribute to flawed software selection:
- Poor communication between the IT team and business units
- An unreliable ERP vendor or a software vendor who offers insufficient support
- Software that requires too much customization
- Poor planning, inadequate ERP research and testing of the software and lack of training for users
11. Not Considering the User Experience
Lack of attention to the user interface during ERP implementation results in under-utilization of the solution and increased implementation cost. During the implementation process, developers and managers focus more on fulfilling the technical requirements of your organization, leaving the end-users in the pitfalls of chaos and confusion.
The consequences of neglecting the needs and expectations of the users are:
- Poor adoption rates
- Low levels of satisfaction with the new system
- Employees struggling to use the new system
- Frustration and inefficient work
- Resistance to change
12. Neglecting Change Management
Some ERP projects fail because change management is neglected. Of all the possible errors, poorly executed change management is the most avoidable cause of ERP implementation failures.
Many organizations make the mistake of focusing too heavily on technological issues and not giving enough attention to the people involved in the process. Like any organizational change, successful ERP implementation requires a comprehensive change management strategy that addresses the concerns, fears and resistance that employees may experience.
The lack of awareness and training is a significant obstacle to the adoption of new processes and procedures, leading to resistance and lack of acceptance. In particular, poorly defined roles, responsibilities and workflows cause confusion and frustration, leading to an ineffective work environment.
Ready to start your digital transformation journey?
Click the button below to request your free discovery call.
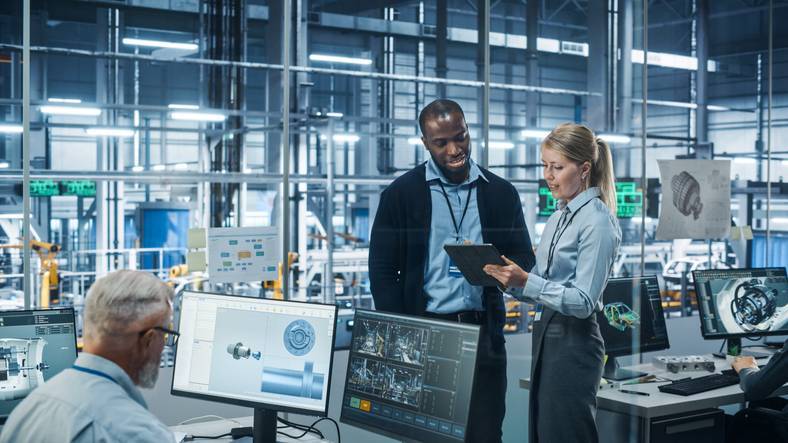
13. Lack of Focus on Critical Technical Areas
Some ERP implementation failures can be attributed to a lack of focus on critical technical areas. It’s important to focus on data cleanup/conversion, integrations and reporting from Day One of the project.
Many projects don’t focus on these areas until it’s too late. Ignoring or underestimating these areas could result in significant issues during or after implementation. Some of the critical technical areas include data cleaning and migration, system integration, customization, testing and training.
The consequences of a lack of focus on critical technical areas:
- Failure to migrate data properly results in data loss and inaccuracies
- Poor system integration leads to incompatible systems or a lack of real-time data synchronization which lead to lost sales, lost market credibility and even a dip in stock price
- Inadequate customization hinders the use and adoption of the system by employees
- Insufficient testing leads to system errors and user frustrations.
- Inadequate training causes low adoption rates and low user satisfaction.
14. Inadequate Project Communications
A new ERP must be positioned properly, as a productivity improvement investment that will make your company more competitive, profitable and successfully. Communicate throughout your organization that the ERP project is as important as a new plant or a new product line.
Insufficient communication between stakeholders may result in misunderstandings, misinterpretations and lack of alignment, leading to decreased project support and user adoption. The absence of clear, timely and relevant information regarding project goals, timelines, roles and responsibilities may also create confusion and cause delays.
Moreover, poor communication often leads to resistance to change, which significantly hinders the ERP implementation process. Inadequate communication also increases the risks of scope creep, budget overruns and inadequate resource allocation.
15. Poor Implementation Planning
It’s not possible to overstate how essential proper project planning and executive management involvement are to the success of your ERP rollout. And most organizations significantly underestimate the time, system requirements and resources required to plan methodically and comprehensively for the new software.
Poor implementation planning occurs when your company:
- Does not invest enough time or resources in planning the deployment of the new ERP software
- Makes the mistake of underestimating the complexity of the implementation process associated with ERP software
- Fails to adequately train your employees or assign the appropriate resources to ensure a smooth transition
- Does not have a clear understanding of how the ERP system fits into legacy systems and business processes
Other issues that arise due to poor implementation planning include miscommunication between stakeholders, incorrect data migration and inadequate testing before going live with the ERP software.
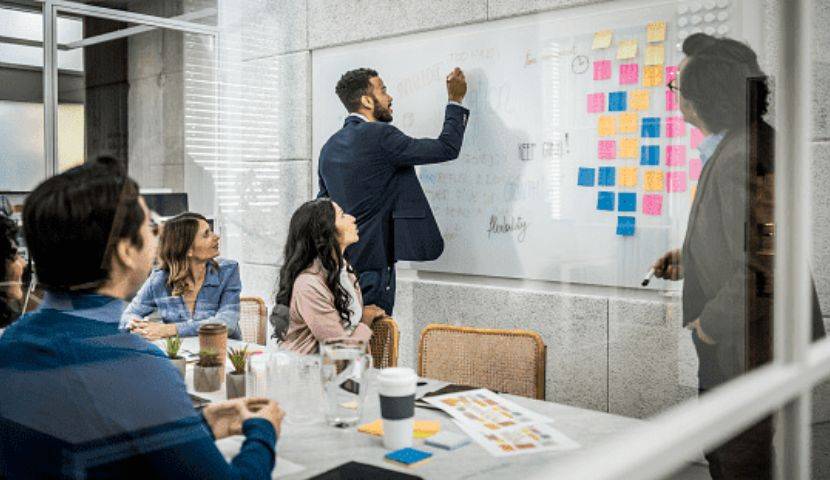
Set Up Your ERP Project for Success
So, do ERP projects fail? Yes. Some ERP implementation projects fail to meet the business goals. ERP projects can fail to go live on time, costing valuable resources. But one of the most common reasons why ERP implementation isn’t successful is because the core executives in the business are inexperienced with ERP implementation and unprepared for the magnitude of the responsibility placed upon them.
To speak with a knowledgeable ERP and digital transformations specialist about the complexities of your business and how best to select an ERP system or begin the ERP research and analysis processes, reach out to us. With new software and new processes, the future possibilities for your business are endless. And after your ERP selection, we’ll stick around to manage your ERP implementation project for you as well.
Table of Contents
More ERP material...
The Undeniable Benefits of Implementing ERP in Food and Beverage Manufacturing
Data analytics holds the ability to highlight inefficient manufacturing processes and enable…
Emerging Technologies in Manufacturing Driving Business Growth
Data analytics holds the ability to highlight inefficient manufacturing processes and enable…
How Food Production ERP Improves Manufacturing Efficiency
Data analytics holds the ability to highlight inefficient manufacturing processes and enable…