Ultra provides expertise related to enterprise resource planning (ERP) systems for process manufacturers. Process manufacturers work with ingredients instead of parts, and the production process is more focused on recipes and formulas than traditional bills of materials. ERP for process manufacturing specifically caters to industries that produce goods through recipes, formulas, or batch production, such as food and beverage, pharmaceuticals, and chemical manufacturing.
Production is often continuous or executed in batches. Many batch process manufacturers operate in a hybrid environment where the process-produced goods are then packaged or formed into a discrete unit, more common in discrete manufacturing operations.
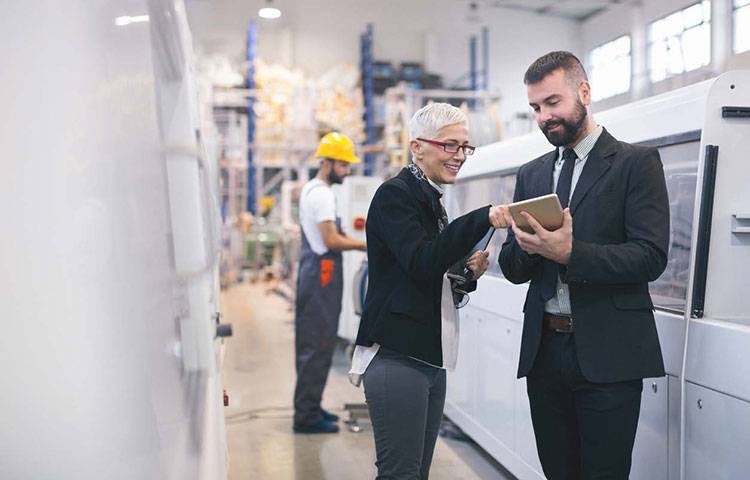
How ERP Solves Process Manufacturing Challenges
Download this eBook to discover how ERP software can revolutionize your process manufacturing operations and launch your company towards growth.
Competition in the process manufacturing industry, whether in food manufacturing, chemical processing, or other areas, has become tough and process manufacturers must be rigorous and stringent throughout their manufacturing processes.
Companies in this category typically fall in these sectors:
- Chemical
- Coatings/Paint
- Food and Beverage
- Metal Processing
- Oil/Gas Processing
- Pharmaceutical
- Plastics
- Other Process
Process manufacturing requires ERP software that can track raw materials, as well as their potency, shelf life, batch or lot number and overall quality.
Lindsay Moore, TechTarget
Efficient operations are crucial for process manufacturers. ERP systems provide a centralized platform that allows you to manage and automate your entire production chain. From procurement and inventory management to quality control and compliance, process manufacturing ERP software helps you streamline workflows, reduce manual errors, and eliminate bottlenecks that hinder productivity. When considering batch process manufacturing ERP software, enterprise technology helps these companies meet many of the business challenges they face, including:
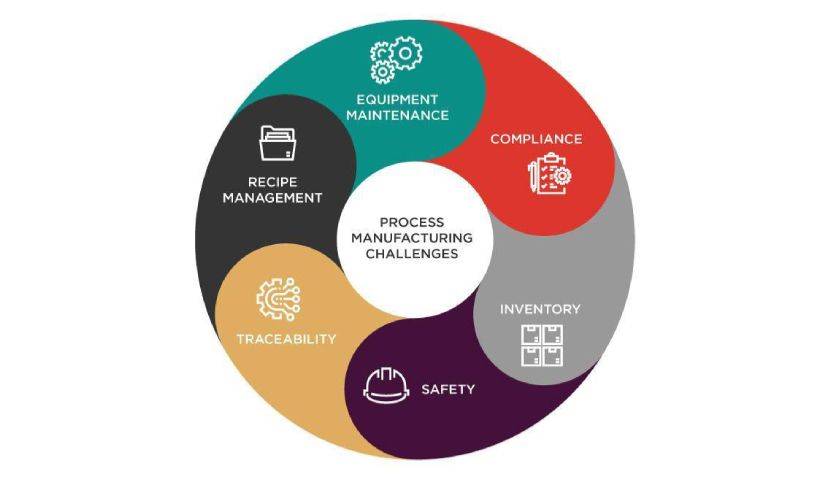
Facilitating Traceability:
Adding traceability to a production method involves providing evidence and documentation that every process is in compliance with regulations, reporting requirements. With a process manufacturing software like ERP, you can track the movement of raw materials, ingredients, and components throughout the entire production process. This provides real-time visibility into inventory levels, usage, and location, enabling better planning, reduced waste, and improved efficiency. ERP traceability enables manufacturers to identify and resolve quality issues swiftly. By linking test results, batch numbers, and production data, a process manufacturer can pinpoint problematic batches and take corrective actions promptly. This not only boosts customer satisfaction but also minimizes the risk of costly product recalls.
Trackability isn’t limited to in-house processes. ERP enables manufacturers to trace materials back to their suppliers, ensuring accountability through the supply chain optimization. Traceability systems in process manufacturing typically involve the use of mobile devices, barcode or RFID technology, along with software solutions to manage and analyze the data collected from manufacturing operations.
Formula and Recipe Management:
One of the key features of a process manufacturing ERP system is its ability to handle complex recipes and formulas. Gone are the days of manually calculating ingredient quantities and struggling to maintain consistency. ERP systems enable you to digitize and standardize your recipe management—as in the food and beverage industry—ensuring accurate measurements, optimal inventory levels, and faster production cycles. With real-time visibility into your formulas, you can easily adjust them to meet changing market demands or regulatory requirements.
Compliance and Quality Management:
In process manufacturing, compliance is non-negotiable. ERP solutions equipped with robust compliance modules help you stay on top of industry regulations and certifications, such as FDA compliance or ISO standards. These process manufacturing systems provide traceability throughout the production process, allowing you to track raw materials and ingredients from suppliers to finished products. Forward and backward lot traceability is part of this process. By automating quality control processes, you can identify and address any issues before they escalate, ensuring consistent product quality and customer satisfaction.
Inventory Control and Supply Chain Management:
Managing inventory can be a nightmare for process manufacturers. ERP systems come to the rescue by providing real-time visibility into your stock levels, ensuring you have the right materials at the right time. By integrating your supply chain processes with the right software solution, you can optimize procurement, reduce lead times, and enhance supplier collaboration. This not only minimizes stock-outs and wastage but also leads to cost savings and improved customer service.
Ready to start your digital transformation journey?
Click the button below to request your free discovery call.
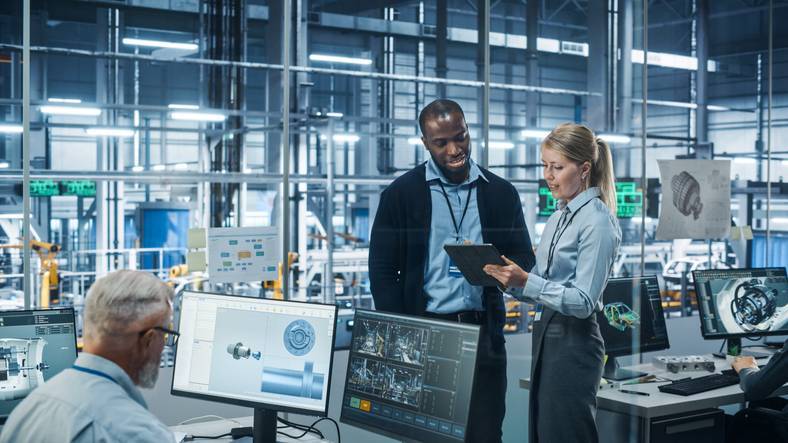
Meeting Environmental, Safety Mandates:
Process manufacturing businesses, in particular, faces unique challenges in meeting stringent environmental and safety mandates. For food processors, chemical processors and others, this involves satisfying food safety and environmental regulations. One of the primary advantages of using ERP in process manufacturing is its ability to centralize data management. With an ERP system in place, businesses can consolidate all their crucial information related to environmental and safety regulations into one integrated platform. This streamlines data collection, analysis, and reporting to regulatory agencies, making compliance a breeze.
Also, ERP systems offer real-time monitoring and reporting capabilities, allowing process manufacturers to track and manage their environmental and safety practices in a more efficient manner. By automating data collection, businesses can easily generate accurate reports, identify potential risks, and take proactive measures to mitigate them promptly. Plus, With the ability to track and analyze data, process manufacturers can identify areas of improvement, such as energy consumption, waste reduction, and safety protocols. By leveraging these insights, businesses can implement proactive measures, optimize business operations, and stay ahead of changing regulations.
Managing Equipment Maintenance:
The challenge for many process manufacturers to keep all equipment functioning efficiently throughout the process does also require careful management. Replacement, maintenance, and managing equipment at optimized costs are included in these efforts. One of the key advantages of using ERP software is the ability to centralize your asset management. With ERP, you can maintain a comprehensive database that houses all the information about your equipment, including maintenance schedules, service history, and spare parts inventory. This centralized approach makes it easier to track and manage your assets, enabling you to schedule preventive maintenance more efficiently.
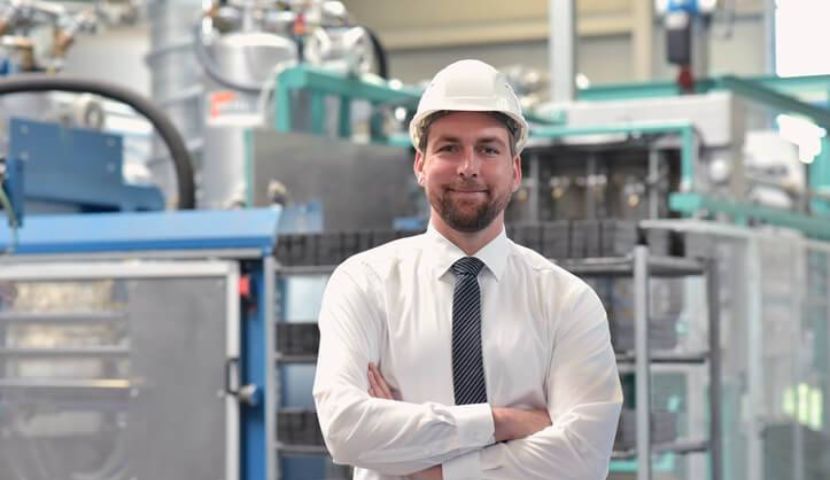
Requirements of a Process Manufacturing ERP Solution
To help meet these business requirements, the process manufacturing sector has specific ERP needs and requirements, including features related to :
- Formulation
- Compliance documentation
- Quality control
- Order management
- Demand forecasting
- Expiration dates handling
- Inventory management
- Reporting tools
- Creation of food labels
Manufacturers of discrete and process goods must be able to keep track of various SKUs, lot sizes and units of measure, material inputs, expiration dates, client pricing and locations, and various labeling and package styles. Fortunately, an ERP solution can be applied to both discrete and process manufacturing, with favorable results.
ERP Systems for Process Manufacturers: A Look at Chemical Manufacturing
When considering ERP for process manufacturing, let’s look deeper at the issues facing chemical manufacturing.
Chemical processors today face tremendous pressure in protecting margin in the midst of economic uncertainty.
The chemical industry produces essential components of practically every consumer and industrial product. Many chemical industry products are intermediates, and chemical company customers are often other chemical companies. Several companies in this industry are also at the forefront of emerging biotechnology industries.
It’s a complex manufacturing process within the sector.
Chemical products result from chemical processes, which are a complex combination of reaction, distillation, absorption, filtration, extraction, drying, and screening operations. For cost-cutting purposes, most chemical processes must be efficient, and so the design of many production operations is focused on controlling and reducing losses of precious materials.
Much like the general requirements outlined above, issues specific to chemical processors include:
- Formula Management
- Batch Processing
- Product Attributes (e.g. PH, or Hardness)
- Estimating and Sampling
- Lot Traceability and Shelf Life
- Units of Measure (Volume and Weight)
- By Product/Co-Products
- Quality Control & Hazardous Materials
- Commodities Speculation (e.g. LME)
- Equipment Maintenance
Ask These Questions about Process Manufacturing ERP Systems
We’ve touched on high-level concerns when it comes to process manufacturing ERP software. But there are many others, especially as related to streamlining processes and improving overall business performance. As an independent ERP consulting firm, it’s a topic that comes up often as project teams look to Ultra to understand the best way to work through enterprise system selection to improve key business processes related to processors.
When we consult with processors, we often encourage the ERP project team to ask a set of key questions, which include:
- How well do current solutions track individual lots from procurement through manufacturing and ultimately into the finished goods supply chain?
- How quickly can the company respond to inquiries ranging from country of origin to specification compliance?
- How well does the current software help production operators meet quality standards by using receipts and process instructions?
- With customers seeking shorter lead times, how good is visibility into manufacturing capacity and planning?
- How well does the existing software help balance inventory levels with demand to reduce risk of inventory obsolescence?
- Is the current software meeting current best practices and helping you be as productive as possible?
Process Manufacturing ERP Selection Expertise
By embracing this technology, you can streamline your processes, boost efficiency, and navigate the complex world of process manufacturing with ease. So, if you’re in the process manufacturing industry, it’s time to consider implementing an ERP solution tailored to your specific manufacturing business needs. Remember, in a competitive market, staying ahead of the game is crucial, and process manufacturing ERP can give you the edge you need. The expert Ultra team can help fast track your ERP project with process improvement, technology selection and ERP implementation, along with experienced project management. Contact us today to get started.
Table of Contents
More ERP material...
Selecting the Right TMS System: Key TMS Features and Trends to Consider
Data analytics holds the ability to highlight inefficient manufacturing processes and enable…
Choosing a CRM System for Your Business
Data analytics holds the ability to highlight inefficient manufacturing processes and enable…
The Undeniable Benefits of Implementing ERP in Food and Beverage Manufacturing
Data analytics holds the ability to highlight inefficient manufacturing processes and enable…