Your organization has selected a new enterprise resource planning (ERP) software, and plans are in place to start the implementation process. The ERP implementation process is complex with many different parties working together, and any slight misstep can result in the project failing. During implementation, your organization collaborates with your ERP vendor and an implementation partner to configure the system to meet your specific business needs and business functions, migrate data from the old to the new system and train employees on how to effectively use the new ERP system.
With the complex nature of ERP implementations and news about ERP projects failing, it’s natural to have questions about implementing an ERP system so you don’t make the same ERP system implementation mistakes. This article will address the most frequently asked ERP implementation questions and provide you with information that can help turn the tide, ensuring a successful ERP implementation.
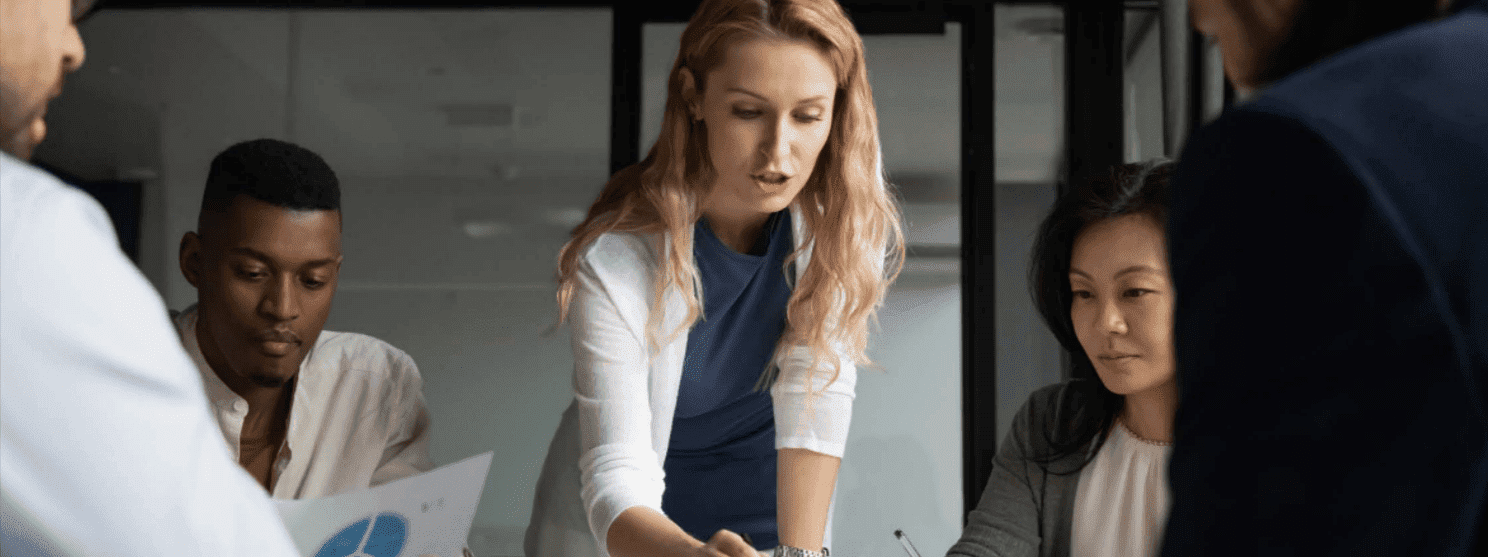
Best Practices for an Effective ERP Implementation
Download the eBook to discover actionable insights to make your ERP implementation a journey of success.
How Long Does ERP Software Take to Implement?
Overview of a typical implementation process timeline
An ERP implementation can take place between 6 to 12 months, and the most complex projects can take 18 months or more. The duration that your project will take depends on the:
- Size and complexity of your organization
- Scope of the project
- Specific ERP solution you’ve chosen
A typical ERP implementation process goes through different phases, starting with a planning phase. The planning phase is where the project goals, objectives and scope are set and the project timeline is established. The next phase is the design phase, where your existing business processes are mapped to understand the pain points in your business. Then comes the development phase, which involves the customization of your selected ERP system to meet your unique needs. The last phase is the testing and deployment phase, which involves thoroughly testing the system to see if it meets your goals and then rolling it out for the end users to utilize in their day-to-day work.
How Do We Prepare Our Data for ERP Implementation?
Key considerations for data cleaning, migration and integration
Accurate, clean, complete and properly formatted data is a must if you want your ERP implementation to bring the expected ROI. Data cleaning, migration and integration helps avoid costly errors down the line and promotes smooth transition from the old legacy systems to the new ERP system.
Before you start migrating your data, conduct a thorough audit of your existing data sources, such as legacy systems, spreadsheets and other databases. Your legacy systems may include customer relationship management and other disparate systems. Look for duplicates, inconsistencies and errors, then clean and standardize the data. Also, during this phase it’s crucial to map the data to the new ERP system’s data model.
Strategies to ensure data integrity and security during transfer
As a manufacturer or a distributor, your organization has sensitive information, such as customer information and product information. This makes data security critical during the ERP implementation process. Put measures in place to guarantee that all data transfers are conducted securely by employing security measures such as data encryption and implementation of access controls. These methods help prevent unauthorized data access and protect your data against breaches and theft.
Establishing clear protocols for data validation and testing—such as conducting spot checks, reconciling data between the old and new systems and running test scripts—guarantees that your data is being transferred accurately and completely.
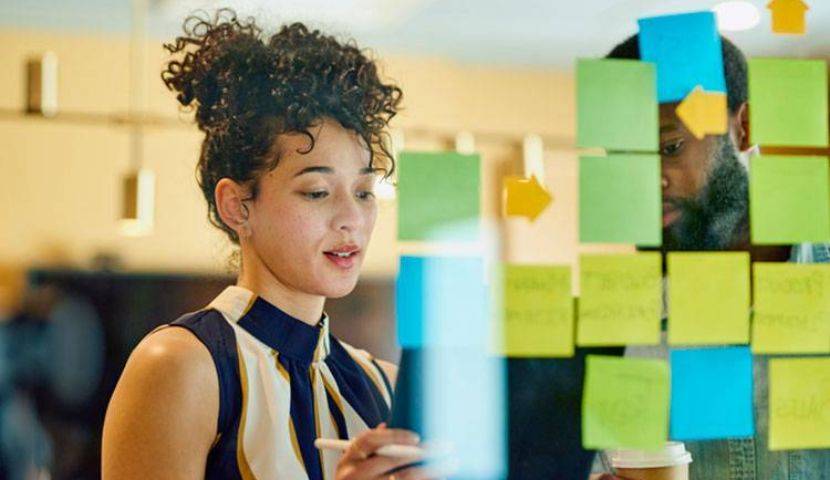
What are ERP Implementation Risks?
Why do ERP implementations fail? ERP projects require strict management to avoid these well-known risks.
1. Lack of management support
A lack of support from your top management, such as your COO, CFO or CEO, is one of the major challenges that can derail your ERP project. These are the people who will be allocating resources needed on the project and guaranteeing organizational commitment to the project. And without this, your ERP implementation can fail.
2. Insufficient project management
An ERP implementation requires careful planning, coordination and oversight because of its complex nature. When your ERP implementation doesn’t have proper project management, you may end up with a project with a poorly defined scope with an unrealistic timeline. This may result in the project’s cost ballooning and taking much longer than expected.
3. Poor employee training
Employee training helps the end users of the new ERP solution understand the different functionalities and modules—such as customer relationship management, human resources management, inventory management, supply chain management, and a manufacturing execution system among others—and how to use them. When employees aren’t properly trained on new ERP systems, they aren’t able to use them. You will end up with a shiny toy that is not helping you achieve your business goals. Poor employee training also results in lower adoption rates and increased resistance causing your ERP implementation project to fail.
Ready to start your digital transformation journey?
Click the button below to request your free discovery call.
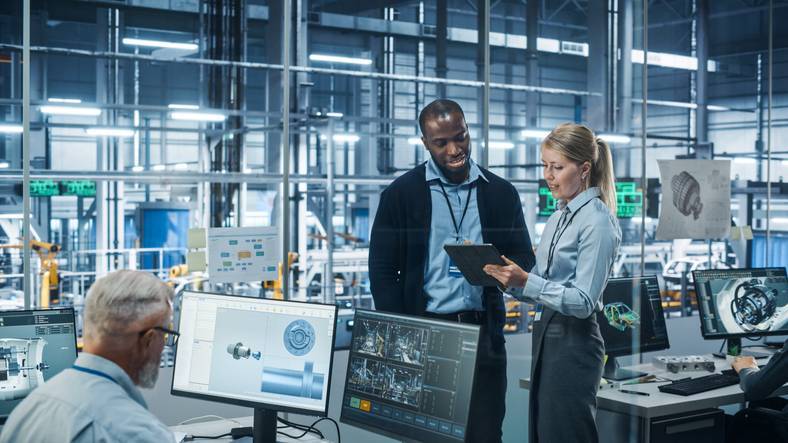
Which Aspects of ERP Solutions Can Be Customized?
Overview of customization options
ERP systems come with core modules and functionalities and can be tailored to align with your organization’s business processes, workflows and reporting requirements.
The following are some common areas for customization:
- User interfaces and dashboards
- Workflows and approval processes
- Data fields and input screens
- Reports and analytics
- Integrations with other systems and tools
Force-fitting ERP systems is not recommended, so select a system that aligns closely with your business requirements.
Balancing customization with maintainability
Your organization should take caution when customizing your ERP system, because over-customization can result in the system becoming too complex, making it harder to upgrade in the future. Striking a balance between customization and maintaining the system’s long-term sustainability is crucial.
What Does the ERP Configuration Process Involve?
Steps to configure the ERP system to align with business processes
The ERP configuration process involves mapping your current processes, identifying areas that need improvements and then fine-tuning the ERP system to support those processes. Without the system configuration process, the ERP system may not be able to help your organization achieve the desired future state.
The following are some of the steps in the ERP configuration process:
Process Mapping — Understanding your current business processes to identify your pain points
Gap Analysis — Looking for gaps between your current processes and the ERP system’s capabilities to determine how configuration and customization can help bridge these gaps
System Setup — Configuring the core core modules and features, such as finance, inventory, production and supply chain management
Workflow Design — Fine-tuning the new ERP system to support your desired workflows, approval processes and data flows
User Setup — Establishing different user roles and permissions by setting up user accounts and access controls
Importance of testing configurations in a controlled environment
Issues can easily be identified and resolved quickly when configurations are tested in a controlled environment before full organizational deployment. This process minimizes any disruptions to your business operations, promoting smooth transition from legacy systems to the new system.
What Are Common Implementation and Post-Implementation Challenges?
ERP implementation requires careful planning to avoid potential risks and challenges. Here are a few ERP implementation challenges to watch out for.
Overview of common challenges and mistakes made during implementation
1. Allowing the scope of your project to go beyond the original plan, resulting in delays and cost overruns
2. Failing to allocate sufficient resources—such as budget, human resources and time—to the implementation project, resulting to the project missing key milestones
3. Failing to keep your key stakeholders in the loop about project goals, status and expectations, leading to misalignment and confusion
4. Failing to address resistance to change issues from your employees, leading to lower adoption rates
5. Failing to address data quality issues and accuracy during the migration process, resulting in errors and inconsistencies in the new system
Strategies for addressing and overcoming these challenges
1. Developing a comprehensive project plan that clearly outlines your project goals, budget, timelines and deliverables
2. Allocating sufficient resources—budget, personnel and time—to the project and getting buy-in from your key stakeholders
3. Establishing open communication channels and protocols to solicit feedback and concerns from key stakeholders
4. Providing your end users with comprehensive training programs and post implementation support to help them adapt to the new processes and technologies
5. Conducting thorough data validation and testing during the data migration process, to safeguard the accuracy of your data and integrity of the new system
How Do You Measure the Success of an ERP Implementation?
Outline KPIs for successful implementation
Key performance indicators (KPIs) help measure the success of your ERP implementation and determine whether the project is delivering the expected return on investment (ROI). The following are some of the critical KPIs to consider:
1. On-time and on-budget delivery to determine if the project met the planned timelines and budget
2. User adoption and satisfaction to determine how effectively your employees are utilizing the new system and if they are satisfied with its functionality and usability
3. Process efficiency and productivity to determine whether the new ERP system has helped with business process management by streamlining business processes, reducing manual processes and improving your productivity
4. Data accuracy and integrity to determine the accuracy of the data in the new system and whether it’s accurate, complete and consistent
5. Business outcomes to determine how the new ERP system has helped improve your key business metrics, such as revenue growth, cost savings or customer satisfaction
Establishing a baseline and tracking progress over time
It’s crucial you establish the baseline of every current performance metric you plan to use, prior to the implementation process, so you can accurately measure the success of your ERP project.
Gather feedback from the key stakeholders by conducting regular surveys and assessments throughout the implementation process, and track progress against your KPIs. This data is crucial in identifying areas for improvement and optimization.
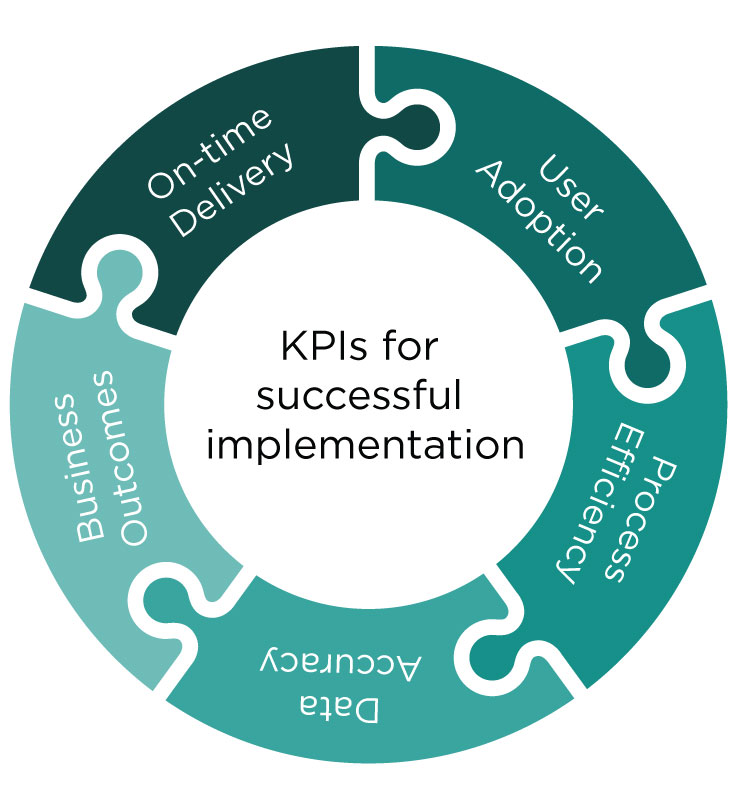
What Can We Expect During the Go-Live Phase and What Are Common Go-Live Challenges?
Knowing when you’re ready to go live
The go-live date is the date when your new ERP system goes live in your organization. Knowing this date and preparing for it is crucial for a smooth and successful transition.
The following are the indicators that you are ready to go live:
- You have tested and validated all critical business processes in the new system
- You have completed data migration and validated that there are no errors and inconsistencies
- You have fully trained your employees on how to use the new ERP system and are comfortable with all the functionalities and workflows
- You have tested and verified the performance of the system and stability and there are no issues and outages
- You have developed a comprehensive go-live plan with disaster recovery plans for any potential issues and have informed all the key stakeholders
Timeline and expectations for go-live
When implementing an ERP system, the go-live phase may last several days or weeks. This will depend on the scope of your project and scale of the project.
Setting clear expectations with your stakeholders is important during this period. Providing additional resources and ongoing support to your employees helps them with any challenges that they may phase during the transition period.
Common challenges and how to mitigate them
- System performance issues and outages that may be caused by high transaction volumes and unexpected errors
- Resistance to change by your employees causing lower adoption rates
- Data quality and accuracy issues caused by errors and inconsistencies in your data during migration process to your private cloud
- Integration issues with your existing systems and processes, resulting in data silos and manual workarounds
Having a clear go-live plan in place can help mitigate any issues and potential disruptions that may occur. A go-live plan usually has contingencies in place for these issues and additional system monitoring and support resources. The plan also contains communication channels that can be used to alert relevant parties in case of any issues.
To tackle employee resistance issues, provide ongoing training and support to equip your employees with all the necessary skills and knowledge to use the new ERP system and processes. When the end users understand how the ERP system will help make their jobs better, they will fully accept the system as part of their daily routines.
Do You Have More ERP Implementation Questions?
As a manufacturer or distributor, an enterprise resource planning implementation project is crucial to help streamline your processes, improve your productivity and outpace your competition. This article has looked at some of the frequently asked questions when it comes to ERP implementation projects with insightful information from our implementation experts to help your organization implement a new ERP system while dealing with issues that may detail the project.
Ultra Consultants is an independent ERP selection, implementation and digital transformation firm that helps manufacturing and distribution companies like yours on their digital transformation journeys. Our consultants are subject matter experts and can guide your organization through each phase of the implementation project, ensuring that it is delivered on-time and on-budget. Connect with us to learn how we can help you, too, achieve a successful ERP implementation.
Table of Contents
More ERP material...
Selecting the Right TMS System: Key TMS Features and Trends to Consider
Data analytics holds the ability to highlight inefficient manufacturing processes and enable…
Choosing a CRM System for Your Business
Data analytics holds the ability to highlight inefficient manufacturing processes and enable…
The Undeniable Benefits of Implementing ERP in Food and Beverage Manufacturing
Data analytics holds the ability to highlight inefficient manufacturing processes and enable…