As the cannabis industry continues to grow, it’s important for growers to implement lean practices to increase efficiency and reduce waste. Lean practices are all about maximizing value while minimizing waste, and they can be applied to any industry, including cannabis cultivation. Here are some tips for implementing lean practices in your cannabis grow:
- Process Mapping
- Identifying Waste
- 5S Methodology
- Data Based Decisions
- Continuous Improvement
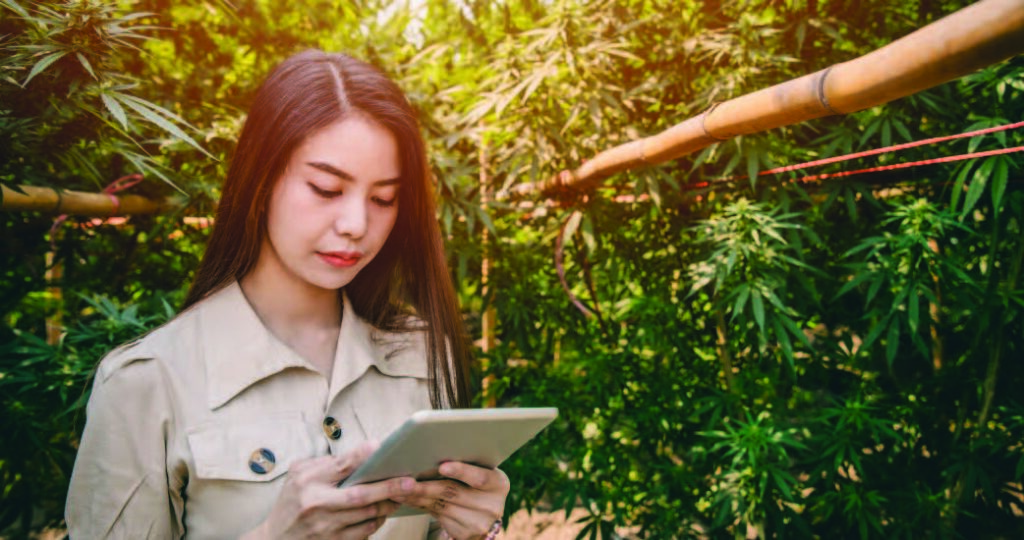
What to Look for in Cannabis Production Software
Confused by what to look for in cannabis software? Let Ultra show you the way.
Process Mapping
The first step in implementing lean practices is to map out your processes. This means identifying all the steps involved in growing cannabis, from planting to harvesting. Once you have a clear understanding of your processes, you can start looking for areas where you can eliminate waste and increase efficiency.
Process maps are graphic depictions of the steps taken to finish tasks. These could be as granular as you like—either with detailed instructions or broad overviews. They can be short, straightforward summaries of a single person’s duties or lengthy, intricate, granular chains outlining numerous processes in various departments. By outlining each step of the process, you may be better able to see what is happening in your business and spot possibilities for improvement.
Identifying Waste
Once you have mapped out your processes, it’s time to identify areas of waste. This could include anything from overproduction to excess inventory to unnecessary movement of plants or equipment. By identifying areas of waste, you can start to develop strategies to eliminate them.
No part of the business is exempt from these considerations. Managers can also consider long waiting times during packaging, carrying costs from excess inventory, inefficient transportation processes, and under-using workers as contributing to the wastefulness of a system.
5S Methodology
5S is sometimes summed up as “a place for everything and everything in its place.” It’s a lean methodology that focuses on organizing and standardizing the workplace. As explained by Lean Production, “at their core, 5S activities build the discipline needed for substantial and continuous improvement by creating (and sustaining) efficient and effective work areas.”
Benefits of implementing a 5S system include creating organized space within your environment, reducing unnecessary (wasteful) movement and action for more efficiency, reducing downtime through proper equipment maintenance, empowering workers with more autonomy over their workspace, and creating a clean, safe work environment. Originally created by Toyota, 5S refers to 5 lean principles: Sort, Set in Order, Shine, Standardize, and Sustain.
Sort – sorting removes unnecessary objects and materials from the workspace. This frees up space for important use, rather than a catch-all for clutter.
Set in Order (Straighten) – straightening lays out the items in the workspace—after your Sorted—so they are easily accessible, eliminating unnecessary steps to access frequently used items.
Shine – this step emphasizes cleaning and inspecting the work area. Its benefits go beyond just aesthetics. Within a clean work area, problems are more easily identified such as spills, equipment breakage, or hazards.
Standardize – once you have the items above in place, you want your hard work to last, right? The standardize step refers to documenting your 5S process. So, for example, you can write down how you’ve organized the workspaces and set a plan or tasks for how and when the organization and cleaning should be repeated in order to maintain the standard. Checklists are a good option for this, organized by role, by shift, and by frequency (daily, weekly, monthly).
Sustain – after your documentation is completed, you will need to check in periodically to make sure that the documentation is being followed. You can also revisit your process to look for ways to make it more efficient.
By implementing 5S, you can create a more organized and efficient workspace, which can lead to increased productivity and reduced waste.
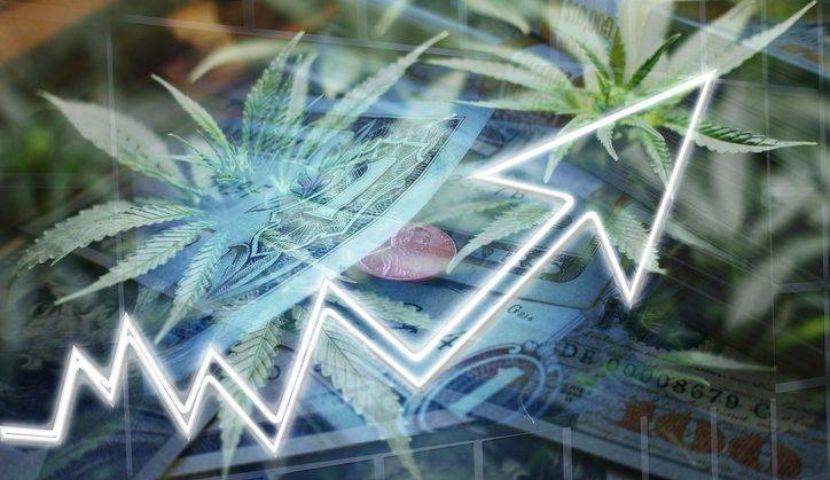
Data-Based Decisions
According to IBM, the average factory generates 1TB of production data every day. While plant floor data has long been used for process control, teams across the organization are increasingly utilizing information to enhance product quality, cut waste, predict maintenance needs, avoid downtime, and provide consumers with new services and products. But collecting data isn’t the end of the story. The data won’t benefit you unless you put it to use.
One of the key principles of lean is to use data to drive decisions. This means collecting data on your processes and using that data to identify areas for improvement. The process starts by asking the right questions. Identify the points in your process that could benefit from analysis. For example, you could track the time it takes to complete each step in your process and use that data to identify bottlenecks or areas where you can streamline your processes.
While data holds great potential to aid business process improvement, it’s important to be able to gather the right data, from the right source, when you need it. Manual documentation and processes make it difficult to be able to pull data quickly with reliable information.
While technology such as seed-to-sale software or ERP might seem daunting, the advantage of real-time, accurate data that eliminates siloed error prone and time-consuming data collection is worth the investment. Companies that are data-driven are more adaptable and can change more quickly as the cannabis market develops. They can also spot possibilities and acquire substantial competitive advantages that will aid in their success in the long run.
Continuous Improvement
Finally, it’s important to remember that lean is a continuous improvement process. Building on your real-time data analytics, you’re able to continue to improve processes in order to maintain a competitive edge.
Once you have implemented lean practices, you should continue to monitor your processes and look for ways to improve. This could involve implementing new technologies, training employees on new processes, or making other changes to increase efficiency and reduce waste.
Continuous improvement is a team effort, getting buy in from all departments and empowering staff to identify and implement improvements. The lean operations mentality extends to seeking out those practices that can further increase efficiency and reduce waste.
To monitor your progress, identify key performance indicators (KPI) and observe the improvement over time. These small gains added together can produce huge increases in productivity, product quality, and profit.
Learn More About Lean Practices
Implementing lean practices in your cannabis grow can help you increase efficiency, reduce waste, and ultimately improve your bottom line. By mapping out your processes, identifying areas of waste, implementing 5S, using data to drive decisions, and continuously improving, you can create a more efficient and profitable cannabis grow.
Contact the experienced Ultra team to learn more about lean processes and how intelligent, optimized processes deliver bottom-line benefits. Contact us for your free discovery call.
Table of Contents
More ERP material...
Selecting the Right TMS System: Key TMS Features and Trends to Consider
Data analytics holds the ability to highlight inefficient manufacturing processes and enable…
Choosing a CRM System for Your Business
Data analytics holds the ability to highlight inefficient manufacturing processes and enable…
The Undeniable Benefits of Implementing ERP in Food and Beverage Manufacturing
Data analytics holds the ability to highlight inefficient manufacturing processes and enable…