This edition of Ultra’s Stories from the Field blog post series looks at how a pet food company’s enterprise technology project helped streamline operations, improve production and lift the bottom-line.
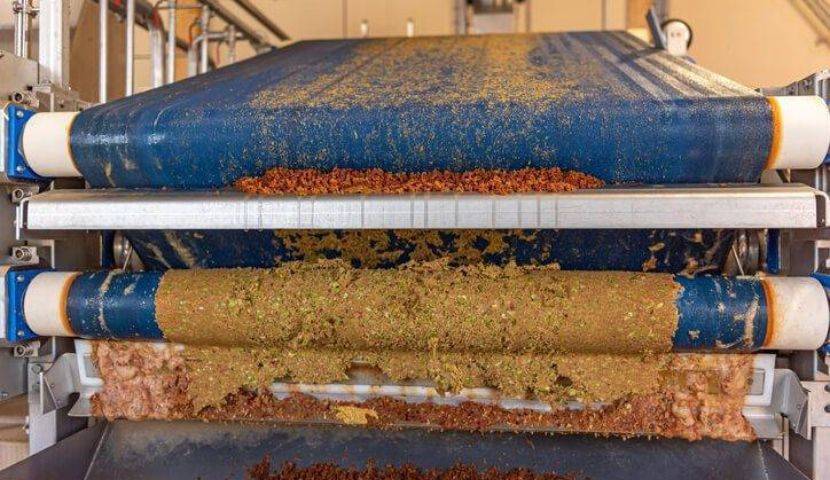
Rates of pet ownership are growing worldwide and the market expansion shows no signs of stopping.
The rise in demand for fresh, organic and healthy foods is disrupting the pet food processing industry as companies meet the challenge of producing high quality, natural, and nutritious pet food while meeting ever-increasing mandates from the Food Safety Modernization Act (FSMA) and other regulators such as pet welfare groups.
Consumers expect variety and consistent quality at a competitive price. With Chewy.com and other online distribution channels, consumers want a personal and speedy delivery.
Pet food processors are meeting the challenges by assessing their internal operations to be sure production is streamlined, so they can meet market trends and efficiently manage costs.
When functions such as inventory, purchasing, planning, and labeling requirements are managed by manual or siloed systems, it’s difficult for processors to compete.
About the Pet Food Company’s Enterprise Technology Initiative
Recently, a multi-national pet food processor with over $100M in revenues engaged with the independent ERP consultant team at Ultra Consultants to help lead an enterprise technology initiative.
The company processes a wide variety of product offerings out of three manufacturing locations in the US and Europe. It’s a complex production environment with more than 1,000 SKUs produced across several continents.
The multi-national processor exports products to numerous markets including the US, Asia-Pacific, Canada, and the European Union.
Operations include high volume extrusion, drying, and packing of kibble, dog snacks and other products. The production facilities also handle freeze-drying, dehydration, bakery operations and other processing operations.
The project team engaged with Ultra to move away from standalone spreadsheets, manual paper-based methods, and siloed systems which were in use to manage supply chain, maintain demand-supply balance, track production, and monitor quality.
As part of the pet food company’s enterprise technology project, the team also looked to reduce waste, meet quality mandates, and in all, optimize production, distribution, and all operations across the enterprise.
The Limits of Legacy Processes
In past years, the company had undergone several initiatives attempting to standardize systems to run operations. The projects did not deliver on expectations, however, since a variety of methods and systems were still in use across inventory, purchasing, planning, labeling, quality management, and other areas.
Formula and recipe management were especially challenging. The company’s three facilities each tracked this area using separate systems. The Research & Development division had its own workflow and data storage systems as well, making for many redundancies in data management. The company also experienced ongoing challenges with standardized reporting.
Quality was monitored with spreadsheets and paper tracking sheets and was more of a Quality Control process than Quality Assurance. It was difficult to comply with FDA mandates and manage risk-based preventative controls.
Managing non-conformance/Corrective and Preventative Action (CAPA) was done with a master spreadsheet which was labor-intensive. While quality issues were identified adequately, the organization had no access to quality trends or issues notifications across the enterprise.
In addition to the areas noted above, additional challenges were in the areas of:
- Vendor management
- Nutritional labeling
- Reporting, visibility into real-time data
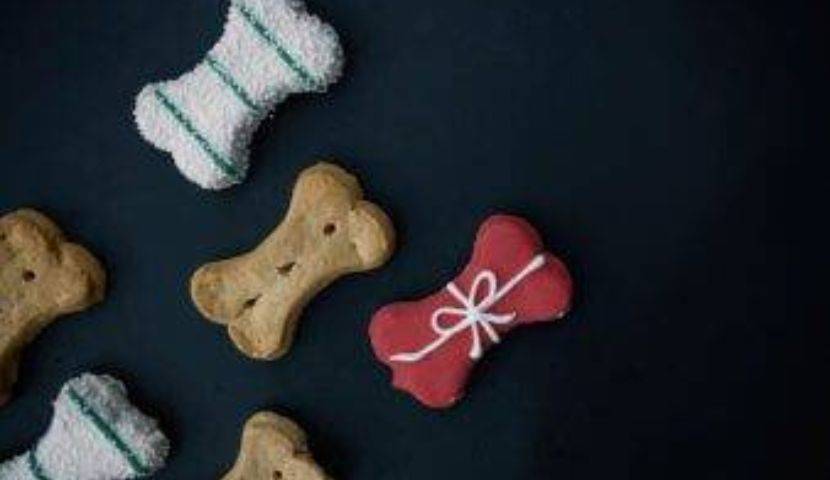
Driving Success with Technology
The Ultra team led the pet food company’s enterprise technology project to help them achieve true business transformation. As independent ERP consultants, we came to feel like we were part of the organization – working shoulder to shoulder with ERP project teams throughout the enterprise.
After becoming well-versed in the company’s processes, our team conducted an ERP requirements definition to identify criteria the new enterprise software should address, including quality, recipe and formulation management functionalities.
Eliminating stand-alone spreadsheets and manual tracking helped the global pet food company achieve sustained business process improvement
After the team analyzed the current state and defined the future state through Ultra’s comprehensive ERP readiness assessment, the processor had the confidence it needed to objectively evaluate software options and navigate the competitive vendor landscape.
With Ultra’s expert guidance, the processor ultimately selected and Implemented the best enterprise software for the company – one that let it scale to manage expansion and growth.
The processes and system improved all critical business processes, including catch weight, multiple units of measure, recipe management, quality management, promotions and demand planning.
The team reports they are realizing value from the pet food company’s enterprise technology project led by Ultra. The single integrated solution across multiple countries provided complete visibility of the global position in terms of production, operations, supply chain, and financial analysis.
Read More About the Benefits of ERP
- A comprehensive case study library showcases additional real-world ERP success stories.
- Download “Maximizing ROI in Your ERP Project” for further insight.
- Ready to create your own success story? Contact us.
The 7 Deadly Sins of ERP Implementation
Some mistakes are just bad strategic or financial decisions. Some are the inevitable consequence of situational or organizational factors. Some, however, are the result of process-oriented or people-centric choices – and are easily avoided. These are The Seven Deadly Sins of ERP Implementation.
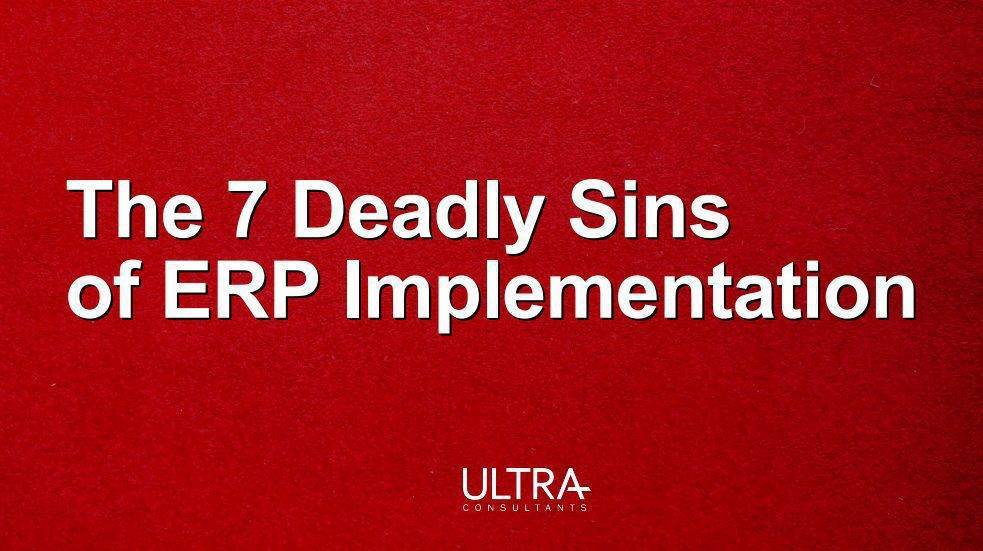
Table of Contents
More ERP material...
Selecting the Right TMS System: Key TMS Features and Trends to Consider
Data analytics holds the ability to highlight inefficient manufacturing processes and enable…
Choosing a CRM System for Your Business
Data analytics holds the ability to highlight inefficient manufacturing processes and enable…
The Undeniable Benefits of Implementing ERP in Food and Beverage Manufacturing
Data analytics holds the ability to highlight inefficient manufacturing processes and enable…