For Food & Beverage Manufacturers continually seek solutions to meet a long list of challenges that includes rising raw materials prices, perishable ingredients and products, a disrupted supply chain, and stringent regulatory requirements. To meet these challenges, Food & Beverage companies—big, medium and small—are looking to modern Enterprise Resource Planning (ERP) solutions to help them manage more effectively, streamline key functions, and accelerate core processes to maintain their competitive edge.
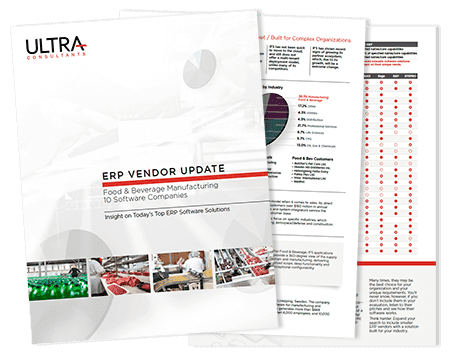
ERP Vendor Update: Food & Beverage Manufacturing
The ERP Vendor Update offers a close-up look at 10 of today’s top F&B software solutions.
ERP for Food Manufacturing
Modern ERP systems empower food manufacturers to optimize their processes, improve productivity, ensure compliance, and enhance customer satisfaction, ultimately leading to increased profitability and growth. Because there are so many ERP system options for food manufacturing, from smaller vendors like Deacom to giants like SAP among others, selecting the best manufacturing ERP systems can be challenging. At Ultra Consultants, we’ve chosen 10 of the Top ERPs for Food Manufacturers in this blog, in no particular order.
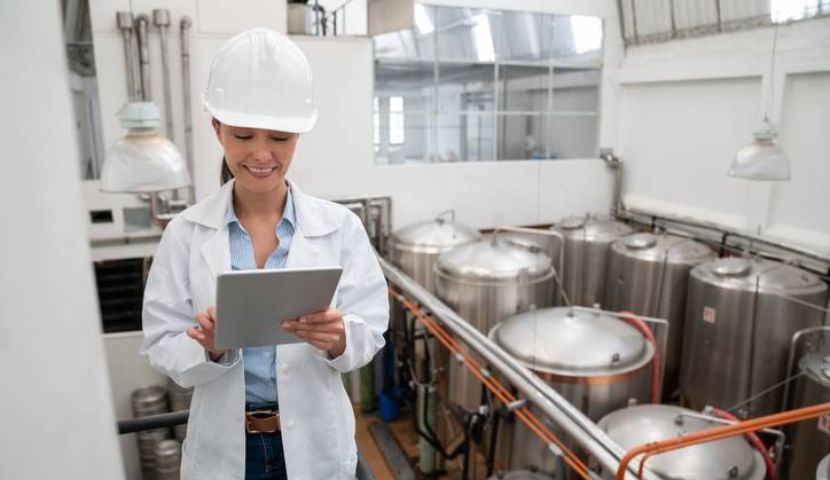
Overview of the 10 Top ERP Vendors
1. Aptean
Aptean aggressively expanded its portfolio of F&B solutions with several strong acquisitions in 2019. It will be interesting to see how its strategy matures as it rolls these into one product. These food-specific solutions have solid technology behind them—all are built on the Microsoft cloud platform.
The Food and Beverage ERP suite brings together six solutions—JustFood, bcFood, LINKFRESH, DIN, Agiles and Foodware 365—all built on the Microsoft Dynamics 365 platform and tailored to specific segments of the industry. Part of the company’s larger product network, the food and beverage offerings are supplemented with connectivity to payment, ecommerce, MES, EAM and transportation management systems.
Key Features
- Supply Chain – Helps you manage product variations including attributes such as breed, cut, age, variety, region of origin or packaging specification, product tracking, allergens and much more.
- Operations/Manufacturing – Effectively plan, monitor and manage production within your environment with features such as labeling, optimized production touchscreen and backflushing enhancements.
- Lot Profitability – Realize every detailed cost—haulage, labor, machine costs, duty, rework and more.
- Advanced Quality Control – Allows for a variety of quality controls to be performed: time based tests, calculated tests, or conditional tests automatically served to quality operatives on mobile tablets on the shop floor for real time data entry.
2. Deacom
Deacom is a strong player in the mid-market, especially for process manufacturers in Food & Beverage, Chemicals and Life Sciences. It offers a rich feature set, as every release includes major functionality enhancements, which are rolled out to its entire customer base.
Deacom is a 100% direct organization, and all services and support are provided by Deacom employees. Its software functionality is native to the core ERP, and a large number of features are industry-specific. Deacom uses a fixed-price implementation model, with first-year maintenance included. Its targets are companies with $40 million to $2 billion in annual revenue.
Key Features
- Lot Control with Track and Trace – React quickly and precisely with forward and backwards traceability – between supplier to customer. Identify specific products and customers affected by a lot quality issue.
- Process Control – Gain real-time information and strict process control from planning with Material Requirements Planning (MRP), Receiving goods, Quality Check to Production, Production, Quality Check after Production, Document Generation, Shipment.
- Documents and Label Management – eliminate the manual creation of these documents outside of your ERP system.
- Quality Control – set up quality control measures and compare with actual quality control results.
3. IFS
IFS thrives in complex organizations in both process and discrete manufacturing. IFS benefits from an experienced and tenured implementation team, and a customer base that is loyal to the organization and the product.
IFS deploys a hybrid model when it comes to sales. Its direct sales team services customers over $150 million in annual revenue, and resellers and system integrators service the under-$150 million customer base.
Key Features
- Manufacturing – Control over the production process across multiple manufacturing modes.
- Supply Chain Management – Smooth, efficient operation with complete visibility locally or globally.
- Procurement – Identify and realize tangible cost savings, foster closer supplier relationships.
- Customer Relationship Management – Drive engagement with customers and prospects.
4. Infor
Infor has undergone some significant changes in recent years, with new ownership and leadership. But its strategy of providing industry-specific software in the cloud has not changed, which is an encouraging sign.
The company builds industry-specific solutions in the cloud using technologies that put user experience first, leverage data science and offer easy integration into existing systems. Infor combines direct resources with a robust partner network when going to market. The Infor Partner Network is a global ecosystem of people, services and systems—designed to provide world-class solutions, and high-quality training, support and enablement.
Key Features
- Lot traceability – Trace backward from end products to identify potentially contaminated lots and forward to determine the potential consequences of product issues.
- Warehouse mobility – Automate common processes in the warehouse and production floor, including receiving, pick and pack, dispatch, inventory transfers, and physical inventory counts.
- Production scheduling – Balance avoiding stock outs vs. being left with excess inventory while meeting customer orders on time and in full.
- Product lifecycle management – Calculate, simulate, and optimize nutritional values, allergens, and cost of formulations.
- Supply chain management – Demand planning, supply planning, and scheduling solutions offer visibility and enable you to optimize service levels against lowest cost.
5. Microsoft D365
Microsoft goes to market in a purely channel model. Microsoft has provided a strong foundation in their base product, and then it’s up to their vast network of VARs and ISVs to build their own Intellectual property, providing industry-specific enhancements.
Key Features
- Purchasing – Create a purchase invoice or purchase order to record the cost of purchases and to track accounts payable.
- Inventory – Enhance your overview of items and find them by categorizing items and giving them attributes to search and sort by.
- Project management – Perform common project management tasks, such as configuring a job and scheduling a resource, as well as providing the information needed to manage budgets and monitor progress.
- Production planning – Supply for anticipated and actual demand from sale, assembly, and production as well as features for distribution planning using stockkeeping units and location transfers.
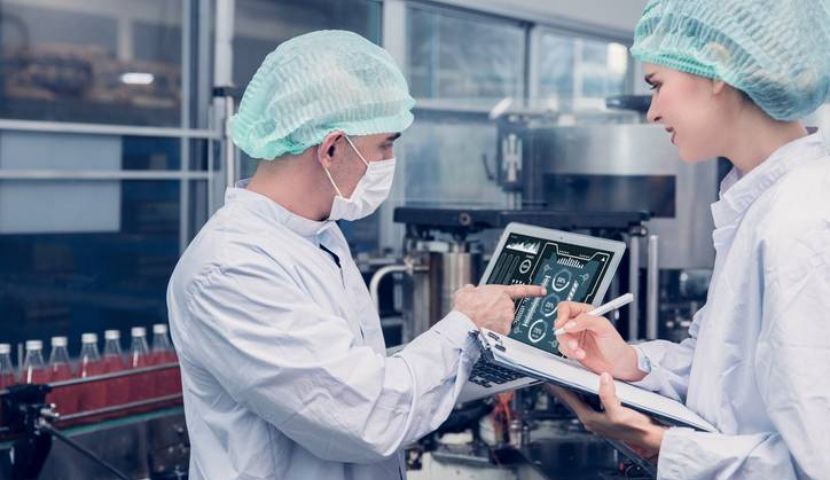
6. Plex
Plex has long been known as a player in the automotive and metals industries, but over the past five years Plex has started to make waves in Food & Beverage. This new focus makes good sense, given that a number of requirements in their bread-and-butter industries are also necessary in F&B—compliance, quality, strong EDI and traceability, to name a few.
Focused solely on manufacturing (process and discrete), the Plex Smart Manufacturing Platform includes MES, ERP, supply chain planning, Industrial IoT and analytics. The company goes to market with a direct-sales model (plus referral partners) and boasts of a 96% subscription renewal rate.
Key Features
- Batch-oriented MES – Schedule pre-process/prep operations tied to specific batches and batch sizes automatically.
- Plant floor automation – Connect to the plant edge to control information and processes while adding efficiency, saving cost, and eliminating manual errors.
- Food safety & quality management – Execute quality checks on any device and see results on a fully digital, single source of the truth.
- Supply chain planning – Incorporate advanced requirements planning, statistical forecasting, and demand planning with machine learning into your smart manufacturing foundation.
7. QAD
QAD is no stranger in the ERP world, having been around since 1979 and building a loyal customer base along the way. QAD deploys its software either on-premise or in its own private cloud, something that makes it stand out against its competitors who prefer a public cloud option.
The company’s Next Generation ERP product portfolio is headlined by QAD Adaptive ERP, and includes demand and supply chain planning (DSCP), global trade and transportation execution (GTTE) and quality management system (QMS)—all designed to help customers become Adaptive Manufacturing Enterprises.
Key Features
- Quality management – Incorporate the ability to do trial audits that can identify problems well in advance of official audits, giving the team a chance to correct process gaps.
- Supplier management – Facilitate real-time communication, improve procurement processes, and reduce inbound supply risks.
- Procurement planning – Utilize several different replenishment models to determine procurement requirements, including reorder-point quantity, days of supply, forecast driven and others.
- Track and trace – Help control cost by showing the current location of every unit affected by process or component anomalies.
8. Sage X3
Sage X3 is well-suited for mid-sized companies that want broad ERP functionality without the high cost of the big solutions. Complex organizations with complicated requirements, however, are likely to require third-party integrations to achieve all their ERP goals.
Sage recently made a change to its go-to-market strategy, moving to an all-channel model, with the direct team acting as sales and implementation support. Sage X3 is now fully in the cloud after a number of years as an on-premises system with some hosting options. Sage offers on-premises and cloud deployment, but its long-term product vision is focused on SaaS.
Key Features
- Production management – Manage manufacturing processes with one system, including BOM planning, shop floor control, quality control, and project management.
- Supply chain management – Real-time inventory monitoring ensures you keep up with demand. Includes tools for purchasing, inventory management, sales management, and customer service.
- Financial management – Control your bottom line with real-time visibility and compliance tools including budgeting, reporting, multi-currency and multi-tax functionality.
9. SAP S/4HANA
Everybody knows SAP—it’s been a leader, not just in Food & Beverage, but in all industries for decades. In terms of ERP market share, no software vendor owns more than SAP. It offers a fully integrated platform on its proprietary HANA database, and its robust feature set allows it to service organizations ranging from pre-revenue startups to multi-billion-dollar global corporations.
The vast majority of its implementations are handled via system integrators, aided by a partner ecosystem that is among the largest of any ERP provider.
Key Features
- Material management – Effectively manage procurement and inventory with purchasing, inventory, material planning functionality.
- Production planning – Use Master Production Scheduling (MSP), Material Requirements Planning (MRP), Shop floor control, Production Orders, and Capacity Planning for improved production scheduling, better inventory management, enhanced quality control, and improved traceability.
- Quality management – Ensure the quality of products and processes through the following sub modules: Quality Planning, Inspection, Certificates, and Notification.
- Recipe Development – Use Recipe, Ingredient, Formula, and Label Management sub modules for faster time to market, improved recipe accuracy, efficient ingredient management, better quality, and cost optimization.
- Batch management – Manage product traceability and quality control through Batch Creation, Quality Inspection, and Batch Information Cockpit sub modules to achieve improved quality control, better inventory management, improved production planning, regulatory compliance, and efficient recall management.
10. Syspro
SYSPRO is a South African-headquartered organization that continues to expand both its direct and channel programs in North America. The company offers a robust feature set, and focuses on the manufacturing and distribution industries, which is one of its differentiators.
SYSPRO’s strength is its long-term focus on manufacturing and distribution industries, including food & beverage. The company offers the choice to deploy in the cloud, on-premises or both (hybrid). SYSPRO goes to market in the U.S. with both direct sales and channel sales. The U.S. partner base includes over 250 partner contacts and industry solution providers.
Key Features
- Traceability – Track materials from receipt through to delivery to the customer, as well as at any level in between. Also, rapidly identify, quarantine and retrieve potentially defective goods from customers.
- Inventory Forecasting – Take the guesswork out of forecasting, recognize seasonality, outliers and trends.
- Contact Management – With early identification of a defect and the ability to quickly communicate with affected customers, you can minimize the damage of a recall.
- Manufacturing & Operations Management (MOM) – Facilitate the management of the end-to-end manufacturing process through the provision of a fully integrated solution which can schedule, publish, collect, track, analyze and improve production efficiencies.
Are you ready to see what an ERP consultant can do for your organization?
Call or set up a free 30 minute consultation with one of our ERP experts today!
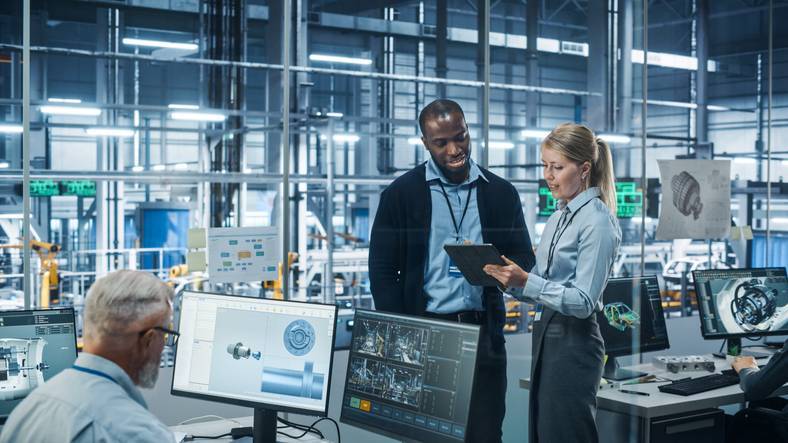
Conclusion
Selecting the right food manufacturing ERP system is crucial for your company’s success. Specific software for food manufacturing can make a significant difference in your business. Choosing the right ERP system for your food manufacturing business can be a tricky process. With so many options available on the market, it can be challenging to make the right decision.
At Ultra, our careful and thorough methodology provides an experienced framework so that manufacturers like you can find the right food manufacturing ERP software that suits your specific needs, streamlines operations and helps you achieve your business goals. The best ERP systems for food manufacturing for your business will depend on your specific needs, so it typically makes sense to partner with an expert ERP consultant who can not only save you time but save you money as you work to discover the best ERP system for your food manufacturing company.
When you’re ready for that first conversation, we’re right here to help with ERP selection, implementation and value realization—for an ERP project that yields results.
Table of Contents
More ERP material...
What Is Enterprise Data Management?
From customer insights to supply chain metrics, organizations depend on accurate, timely,…
Top 10 Uses of AI in Food Manufacturing: Enhancing Safety, Quality, and Efficiency
In the face of changing consumer demands and complex supply chains, food…
AI’s Role in Digital Transformation
Digital transformation is about more than just adopting new technologies—it’s about reimagining…