How Do You Fix ERP Failures?
ERP implementation failure can be a devastating blow to any organization. This failure results in wasted resources, disrupted operations and demoralized employees. However, all hope is not lost. With the right approach and a solid recovery plan, you can fix a failed ERP implementation and get your organization back on track.
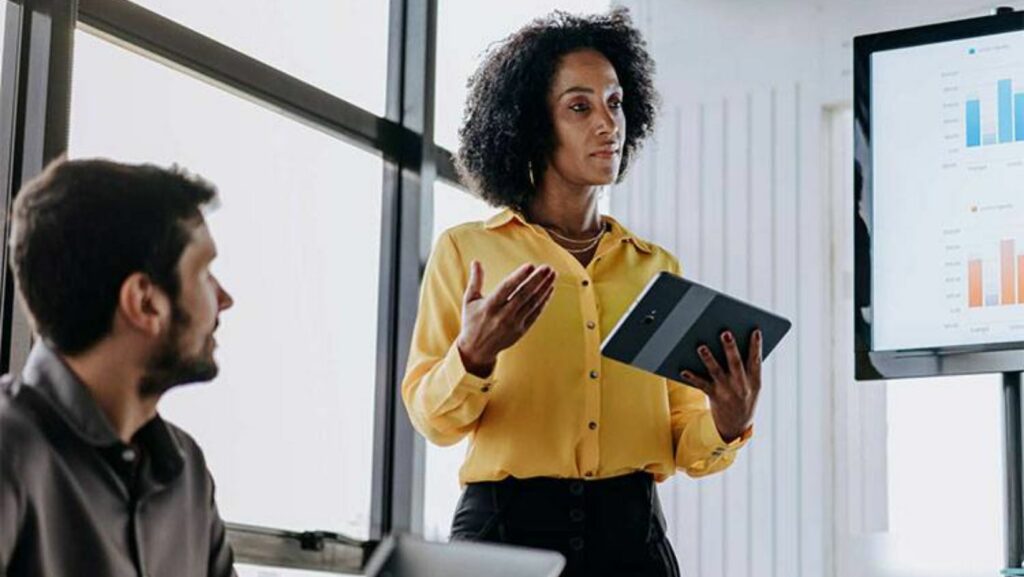
Basics of ERP Rescue
Download our helpful eBook to discover the key steps to rescue a failed ERP project and get repositioned for business success.
1. Assess the Root Causes of Failure
The first step in fixing a failed ERP implementation is to identify the root causes of the ERP failure. There are several common reasons why ERP projects fail, including:
- Poor project management: Inadequate planning, lack of clear objectives and ineffective communication could all be contributing factors to your project failure.
- Inadequate training and user adoption: If employees were not properly trained on how to use the new system, they may not embrace the change, making the implementation more likely to fail.
- Lack of executive support: If you failed to solicit buy-in from top-level management, it can be challenging to overcome obstacles and ensure the success of the implementation.
- Inaccurate requirements gathering: If your organization’s requirements were not properly documented or understood, the implemented system may not have met your organization’s stated needs.
- Insufficient testing and quality assurance:
Inadequate testing leads to system errors and functional gaps that hinder the implementation’s success.
By conducting a thorough analysis of the failed implementation, you can pinpoint the specific issues that led to the failure and develop a targeted recovery plan.
2. Develop a Recovery Plan
Once you have identified the root causes of the failure, it is crucial to develop a comprehensive recovery plan. This plan should outline the steps and strategies that will be implemented to address the issues and get the ERP project back on track.
Some key components to consider when developing a recovery plan include:
- Prioritize Critical Areas: Your organization needs to identify the most critical areas that need immediate attention and prioritize them accordingly. This may include addressing functionality gaps, data integrity issues or performance problems. By focusing on the most pressing issues first, you can quickly restore functionality and regain user confidence.
- Allocate Sufficient Resources: Ensure that you have the necessary resources, including both human and financial resources. These resources play a key role in supporting the recovery efforts. This may involve reallocating internal resources, engaging external consultants or securing additional budget to address the issues identified.
- Establish Clear Objectives and Milestones: Define clear objectives and milestones for the recovery plan. This will help keep the project on track and provide measurable targets for progress assessment. Regularly review and update these objectives as the recovery plan progresses.
- Enhance User Training and Support: Invest in comprehensive user training and support to ensure that employees have the knowledge and resources they need to effectively use the ERP system. This may involve providing additional training sessions, creating user guides and documentation, or establishing a dedicated support team.
- Improve Communication and Change Management: Effective communication is essential during the recovery process. Keep all stakeholders informed of the progress, challenges and changes being implemented, even though it may seem embarrassing to admit failures and setbacks. Additionally, focus on change management strategies to ensure that employees are engaged and receptive to the necessary changes.
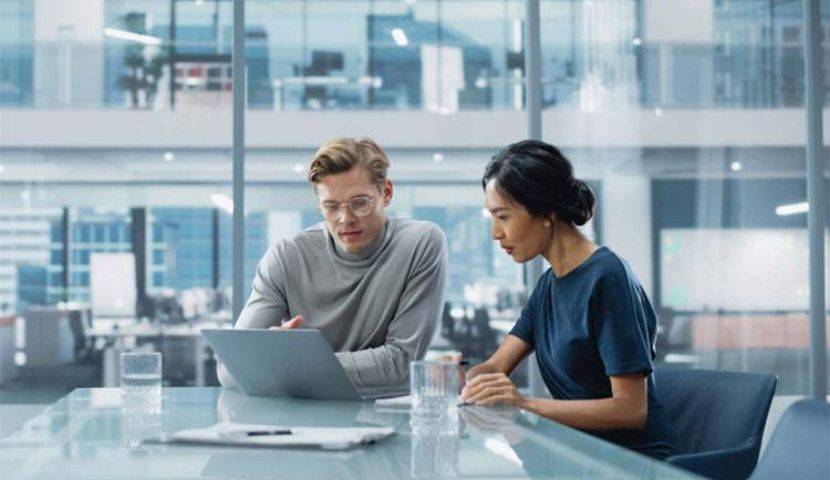
3. Engage Executive Support
Executive support plays a crucial role in the recovery of a failed ERP implementation. Secure the backing of top-level management to ensure that the necessary resources and support are provided, especially if this was lacking during your first attempt. Executives can champion the recovery efforts, advocate for additional funding if needed and help communicate your organization’s commitment to addressing the issues.
4. Implement Corrective Actions
With the recovery plan in place and executive support secured, it’s time to implement corrective actions. Address the identified issues systematically, focusing on the most critical areas first.
Some possible corrective actions may include:
- System customization: Modify the ERP system to meet your organization’s specific requirements, and address functionality gaps.
- Data cleansing and migration: Conduct a thorough review of the data, identify and correct any errors, and ensure a smooth and accurate data migration process.
- Process optimization: Streamline and optimize your business processes to align with the capabilities of the ERP system and improve overall efficiency.
- User training and support: Provide ongoing training and support to ensure that employees are comfortable and proficient in using the system.
- Quality assurance and testing: Implement robust testing procedures to identify and resolve any system errors or functional gaps.
Ready to start your digital transformation journey?
Click the button below to request your free discovery call.
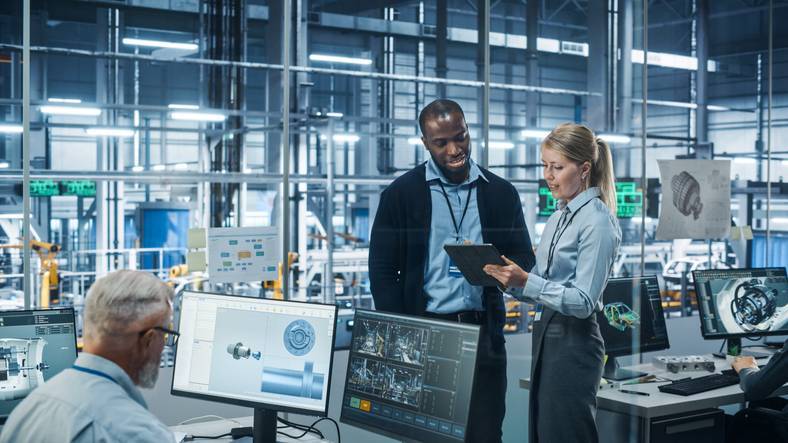
5. Monitor and Evaluate Progress
Continuous monitoring and evaluation of the recovery plan’s progress are vital to ensure its effectiveness. Regularly assess the implemented corrective actions, and measure their impact on your organization’s operations and performance. Make adjustments to the plan as needed based on the feedback and results obtained.
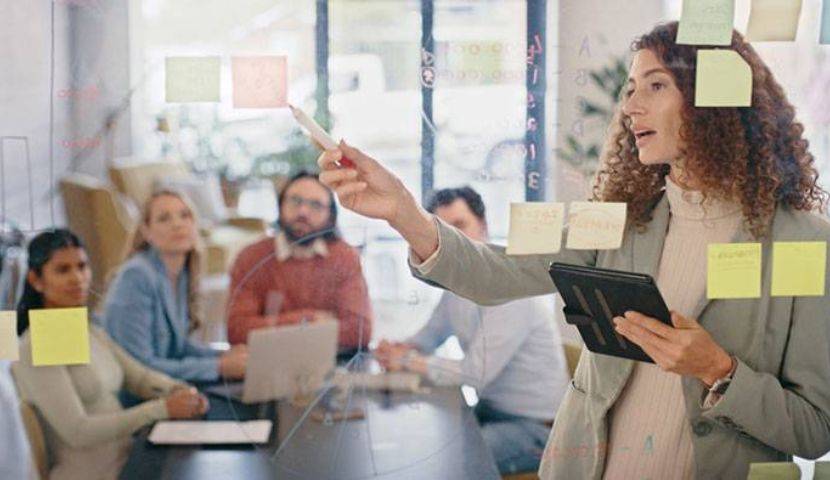
6. Learn from the Failure
A failed ERP implementation provides valuable lessons that can be applied to future projects. Take the opportunity to learn from the failure, and make the necessary improvements to prevent similar issues in the future.
Some key takeaways may include:
- Improved project management: Enhance project planning, communication and risk management strategies to minimize the likelihood of failure.
- Better requirements gathering: Invest in thorough requirements gathering processes to ensure that the implemented system aligns with your organization’s needs.
- Enhanced change management: Focus on change management strategies to facilitate user adoption and minimize resistance to change.
- Robust testing and quality assurance: Implement comprehensive testing procedures to identify and address any system errors or functional gaps before going live. By incorporating these lessons into future ERP projects, your organization increases the chances of success and avoids repeating past mistakes.
7. Collaborate with Experienced Implementation Partners
Partnering with an experienced implementation partner increases the chances of successfully recovering from ERP implementation failure. Implementation specialists bring valuable expertise, industry knowledge and best practices to the table and help your organization navigate the complexities of the recovery process.
When selecting the best ERP implementation consultant, your organization should consider their experience, client testimonials and industry-specific reputation. It is important to choose partners who have a deep understanding of your organization’s specific needs and can provide tailored solutions.
Collaboration between the project team and an independent implementation partner is crucial for efficient issue resolution, knowledge transfer and system optimization. By leveraging the expertise of specialized implementation consultants, your organization expedites the recovery process and ensures a successful outcome.
Conclusion
Fixing a failed ERP implementation requires a strategic and systematic approach. By assessing the root causes of failure, developing a recovery plan, engaging executive support, implementing corrective actions, monitoring progress and learning from the failure, you can turn a failed implementation into a successful one. Remember, prevention is always better than recovery, so it’s crucial to invest time and effort into proper planning and execution to minimize the likelihood of ERP implementation failure.
The Ultra Consultants team can help guide your company through an ERP implementation recovery with our proven methodology for success. Reach out today for your free discovery call to get started.
Table of Contents
More ERP material...
The Undeniable Benefits of Implementing ERP in Food and Beverage Manufacturing
Data analytics holds the ability to highlight inefficient manufacturing processes and enable…
Emerging Technologies in Manufacturing Driving Business Growth
Data analytics holds the ability to highlight inefficient manufacturing processes and enable…
How Food Production ERP Improves Manufacturing Efficiency
Data analytics holds the ability to highlight inefficient manufacturing processes and enable…