The manufacturing and distribution industries are experiencing rapid advancements in technology, led by organizations who are embracing these changes as a way to maintain their competitive advantage and provide more value to their customers. Digital transformation brings about many benefits to companies in the manufacturing and distribution sectors that help future-proof their businesses.
Your organization can experience major benefits by implementing digital transformation initiatives—such as driving growth, improving operational efficiency, enhancing customer experience and promoting sustainability. The end results of these projects can help future-proof your company’s long-term success.
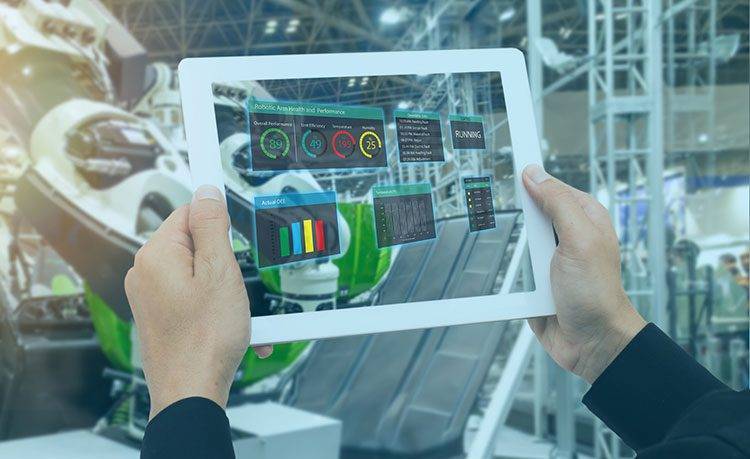
Digital Transformation Checklist
Download the eBook to discover how to navigate the complexities of digital transformation while you drive lasting change within your organization.
Benefits of Digital Transformation
1. Driving Operational Excellence and Cost Efficiency
Streamlining Processes and Boosting Productivity
Optimizing operations and reducing operational costs is one of the biggest benefits of digital transformation. Digital transformation technologies—such as automation, Internet of Things (IoT) and data analytics—are crucial in streamlining processes, improving asset utilization and increasing your workforce productivity.
These digital tools also help you to automate manual and repetitive tasks—such as data entry and inventory management—and integrate systems across your value chain. Through this, you reduce manual labor, minimize errors and boost the overall productivity of your firm, resulting in increased throughput and reduced costs.
Predictive Maintenance and Minimized Downtime
Unplanned downtime is one of the biggest challenges that many organizations struggle with. Through predictive maintenance strategies and production scheduling, digital transformation helps minimize unplanned downtime and extends the lifespan of your equipment. As part of a digital transformation strategy, your business can deploy IoT sensors that monitor machine health and performance in real time, enabling easy identification of potential issues before they can occur.
Predictive maintenance strategies minimize costs and improve overall equipment effectiveness (OEE). When all your equipment functions at optimum levels, you end up having a more reliable production process that can meet your production demands and schedules. From research conducted by McKinsey, predictive maintenance is responsible for reducing machine downtime by 30-50%, increasing machine life by 20-40%.1
Also, production scheduling or planning software—either stand-alone, as part of an MES, or integrated into ERP—can help optimize workflows and manage resource allocation to make the most of workstation and labor capacity. In order to optimize processes and ensure efficiency in the production process, production scheduling software aligns manufacturing schedules with factors including machine availability, labor skill sets and material requirements. It reduces the time spent on manual scheduling, allowing for quick response to changing customer demands or material availability.
“The True Cost of Downtime report shares findings from a study of 72 major multinational industrial and manufacturing companies. It reveals that, on average, large plants lose 323 production hours a year. The average cost of lost revenue, financial penalties, idle staff time and restarting lines is $532,000 per hour, amounting to $172 million per plant annually.”
Steven Aliano, Interchange
Optimizing Supply Chain and Inventory Management
Software solutions—such as enterprise resource planning (ERP) systems—provides your organization with real-time data and advanced analytics that allow you to have end-to-end visibility into your entire supply chain and inventory. These technologies allow you to optimize your inventory levels and improve demand forecasting.
This visibility into your supply chains improves the collaboration between you and your partners, resulting in reduced lead times, lowered inventory carrying costs and improved customer service.
Ready to start your digital transformation journey?
Click the button below to request your free discovery call.
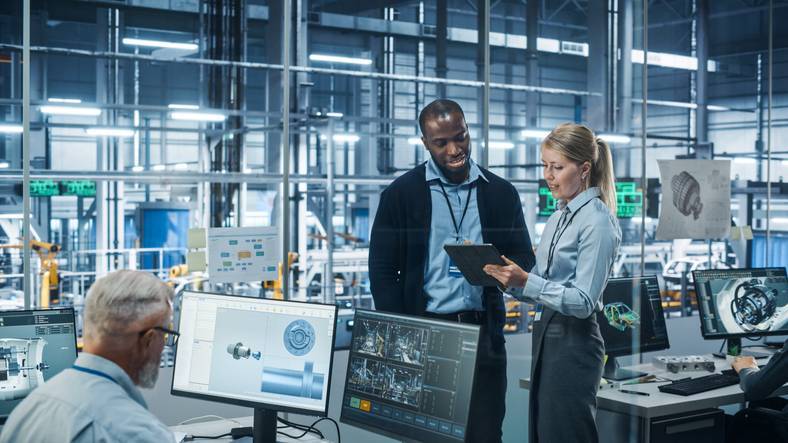
2. Enhancing Product Quality and Innovation
Closed-Loop Quality Management
Another way that digital transformation benefits your business is by enhancing product quality and innovation. Digital solutions facilitate the implementation of closed-loop management systems. These systems make use of data and analytics capabilities, enabling your business to monitor and improve product quality.
These digital transformation strategies integrate quality control processes across the product lifecycle from design, manufacturing and even customer feedback, allowing you to identify and address any quality control issues more quickly and efficiently. When issues are identified and addressed as soon as they are detected, your company reduces rework, scrap and warranty costs, resulting in improved customer experience, satisfaction and loyalty.
Accelerating Time-to-Market
One way that your company can gain a competitive advantage is by providing new products to the market quickly. Digital transformation can help your firm to accelerate time-to-market by streamlining product development processes, fostering collaboration across teams and enabling agile methodologies.
Through cloud-based product lifecycle management (PLM) solutions, your organization can access product data from a single point which allows for real-time collaboration and reduces issues in the development process. Digital tools help reduce product development cycles and respond more quickly to changing customer demands, which gives you the first-mover advantage in the market.
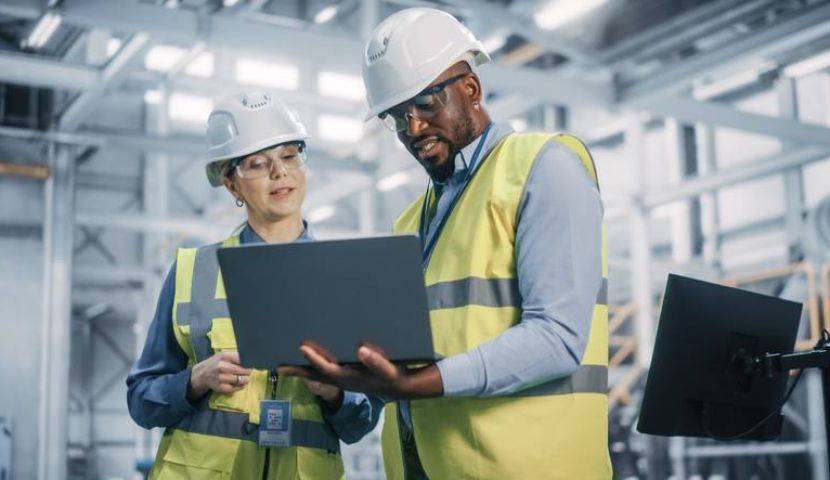
3. Transforming the Customer Experience
Improved Customer Service and Support
Customer service and support ensures that your customers’ complaints and issues are addressed promptly. Having a modern customer relationship management (CRM) system—whether standalone or as a part of an ERP system—empowers your teams to deliver effective and efficient service to your customers. CRM systems centralize important customer data, such as names, contact details, purchase history, service requests and support tickets, enabling your sales reps to easily access relevant data to provide personalized assistance.
To further improve customer service and support, some modern ERP systems come with built-in knowledge bases and chatbots which help offer 24/7 self-service options. This reduces response times to customer requests, resulting in customer satisfaction. These technologies also free up your employees allowing them to handle more complex issues, increasing their productivity.
4. Driving Sustainability and Compliance
Improved Regulatory Compliance
Compliance with industry regulations is a must for companies operating in the manufacturing and distribution industries. With ever-evolving regulations, digital transformation can help your business stay in compliance. Technologies such as product lifecycle management (PLM) and application lifecycle management (ALM) solutions offer a centralized platform for managing business-critical data, such as product and process data. This improves traceability, allowing your firm to stay in compliance with all industry regulations.
ERP systems also ensure compliance by automating workflows and tracking data throughout a product’s lifecycle. ERP systems help you ensure that you have better record keeping and readily available documentation for inspections, translating to detailed audit trails. By implementing digital transformation technologies, your business can automate compliance processes, avoiding costly fines for non-compliance.
Promoting a Sustainable and Responsible Brand Image
Your company’s brand image and reputation can be enhanced by implementing digital transformation for driving sustainability and compliance. In today’s environmentally conscious era, consumers have become more informed on environmental issues and avoid products from organizations that don’t follow environmentally friendly manufacturing processes.
Digital transformation technologies can track and report on key sustainability metrics, allowing you to communicate progress and achievements to your stakeholders. This goes a long way to building trust and credibility. For example, IoT sensors and data analytics can be used to monitor and report on your carbon footprint, water usage and waste reduction efforts.
“If they are to maintain their social license to operate, companies must also comply with ESG pressures from their communities and from consumers who are looking for more sustainable solutions. Consumers are now embracing a more sustainable lifestyle, whether in terms of consumer goods or clean energy alternatives, and are questioning brands about their environmental credentials, increasingly making spending decisions in line with their convictions.”
KPMG Report
5. Managing the Workforce and Fostering a Culture of Innovation
Upskilling and Reskilling Employees
Modern technologies—such as ERP systems, MES systems and stand-alone labor tracking systems can help manufacturers better manage their workforce, adding efficiency and productivity, along with cost control. Labor tracking functionality allows accurate tracking of work hours, bottlenecks, and even worker certifications and completed training, adding visibility to patterns and trends. This data can be used to optimize shifts, allowing for peak times, demand and required skill levels.
With these modern software solutions, your organization can stop relying on paper-based processes. Instructions and important information are offered directly to your employees digitally, which is a more accurate and less-time consuming process. The systems also capture real-time data on both direct production tasks and indirect activities, allowing for accurate allocation of labor costs.
Collaborative and Agile Work Environments
Digital transformation technologies—such as cloud based collaboration tools and platforms—enable different teams and departments to work together, even if they are in different geographical locations. This mode of collaboration helps remove silos and promote innovation. Furthermore, these technologies—ERP systems—enable different departments to access business critical data, ensuring that everyone is working towards achieving your core-business goals.
Unlike traditional methodologies, adopting agile methodologies promote flexibility, adaptability and continuous improvement. With these methodologies, your business can respond swiftly and quickly to the changing market conditions, customer needs and technological advancements, ensuring you remain nimble and competitive.
Attracting and Retaining Top Talent
One way your organization can attract and retain top talent is by implementing digital transformation technologies. The current workforce is more digital-savvy, and many employees are seeking to work for businesses who have cutting-edge technologies.
Digital transformation efforts can help your organization create a culture of innovation, positioning your company as an attractive employer. This way, your firm can attract the talent needed to set your operations for long-term success. Remote and flexible working has become a new norm after the outbreak of Covid 19, and digital transformation technologies enable this working environment. This also helps attract and retain a workforce anywhere in the world.
Conclusion
We are in the digital age, and embracing digital transformation is no longer a choice but a necessity for the future growth of your organization. Digital transformation can help your company thrive in the coming years by driving operational and cost efficiency, enhancing product quality and innovation, transforming the customer experience and promoting sustainability and compliance.
With the right technology in place, manufacturers can effectively predict changes and react with certainty, ensuring success in response to the challenges to come. However, before carrying out any digital transformation project, it’s crucial that you develop a comprehensive digital transformation strategy that aligns with your business goals and priorities.
Ultra Consultants is an independent technology consultant firm helping businesses on their digital transformation journeys. We also understand the importance of staying ahead of your competition and delivering exceptional customer experiences to your clients. Our experts can help your company stay on top of digital transformation trends and developments in your specific industry—whether manufacturing or distribution. We ensure that your digital transformation journey delivers the expected ROI and aligns with your business strategy. Request your free discovery call today to get started on your digital transformation journey.
Table of Contents
More ERP material...
AI’s Role in Digital Transformation
Data analytics holds the ability to highlight inefficient manufacturing processes and enable…
Master Data Management (MDM) Strategy: A Guide to Getting It Right
Companies currently generate vast amounts of data from their systems. But while…
Is Your HCM Platform Future-Ready? 6 Signs It’s Time for a Change
The work world is changing face and HR teams are under pressure…